Products
XEBEC Brush™ Surface
Questions?
Our Application Specialists can help identify the best tool for the job.
XEBEC Brush™ Surface
For simultaneous cutter mark removal, deburring, surface finishing and edges. Precise and repeatable cutting tool performance. Tip cutting brushes fit in a sleeve with tool shank for automated deburring in CNC, robots and other machines.
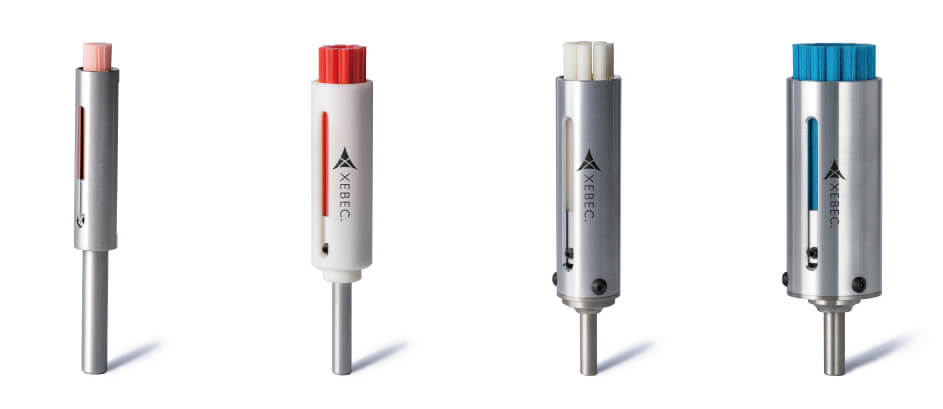
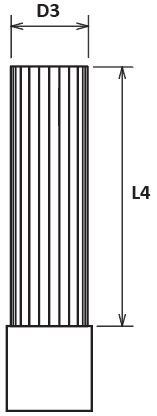
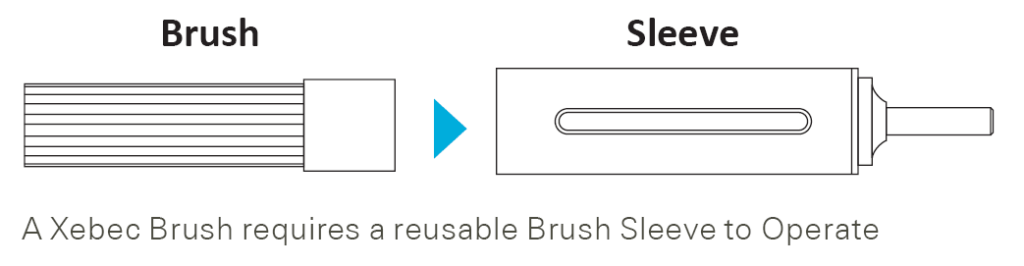
Tool Dimensions Shown: Metric
Inch
Color
EDP
D3 Brush Diameter (mm)
L4 Brush Length (mm)
Max RPM
Matching Sleeve (EDP)
Product Number
List Price
Pink
30013
15
50
6,000
A13-CB15M
$215.58
Pink
30015
6
30
10,000
A13-CB06M
$94.44
Red
30001
100
75
1,000
A11-CB100M
$1,717.55
Red
30002
60
75
2,000
A11-CB60M
$959.56
Red
30003
40
75
3,000
A11-CB40M
$581.39
Red
30004
25
75
5,000
A11-CB25M
$365.68
Red
30005
15
50
6,000
A11-CB15M
$164.09
Red
30006
6
30
10,000
A11-CB06M
$70.33
White
30007
100
75
1,000
A21-CB100M
$1,717.55
White
30008
60
75
2,000
A21-CB60M
$959.56
White
30009
40
75
3,000
A21-CB40M
$581.39
White
30010
25
75
5,000
A21-CB25M
$365.68
White
30011
15
50
6,000
A21-CB15M
$164.09
White
30012
6
30
10,000
A21-CB06M
$70.33
Blue
30040
100
75
1,000
A32-CB100M
$1,717.55
Blue
30041
60
75
2,000
A32-CB60M
$959.56
Blue
30042
40
75
3,000
A32-CB40M
$581.39
Blue
30043
25
75
5,000
A32-CB25M
$365.68
Blue
30044
15
50
6,000
A32-CB15M
$164.09
Blue
30045
6
30
10,000
A32-CB06M
$70.33
Color
EDP
D3 Brush Diameter (in)
L4 Brush Length (in)
Max RPM
Matching Sleeve (EDP)
Product Number
List Price
Pink
30013
0.591
1.969
6,000
A13-CB15M
$215.58
Pink
30015
0.236
1.181
10,000
A13-CB06M
$94.44
Red
30001
3.937
2.953
1,000
A11-CB100M
$1,717.55
Red
30002
2.362
2.953
2,000
A11-CB60M
$959.56
Red
30003
1.575
2.953
3,000
A11-CB40M
$581.39
Red
30004
0.984
2.953
5,000
A11-CB25M
$365.68
Red
30005
0.591
1.969
6,000
A11-CB15M
$164.09
Red
30006
0.236
1.181
10,000
A11-CB06M
$70.33
White
30007
3.937
2.953
1,000
A21-CB100M
$1,717.55
White
30008
2.362
2.953
2,000
A21-CB60M
$959.56
White
30009
1.575
2.953
3,000
A21-CB40M
$581.39
White
30010
0.984
2.953
5,000
A21-CB25M
$365.68
White
30011
0.591
1.969
6,000
A21-CB15M
$164.09
White
30012
0.236
1.181
10,000
A21-CB06M
$70.33
Blue
30040
3.937
2.953
1,000
A32-CB100M
$1,717.55
Blue
30041
2.362
2.953
2,000
A32-CB60M
$959.56
Blue
30042
1.575
2.953
3,000
A32-CB40M
$581.39
Blue
30043
0.984
2.953
5,000
A32-CB25M
$365.68
Blue
30044
0.591
1.969
6,000
A32-CB15M
$164.09
Blue
30045
0.236
1.181
10,000
A32-CB06M
$70.33
XEBEC Sleeve
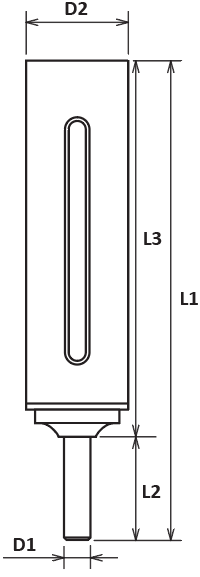
Tool Dimensions Shown: Metric
Inch
Matching Brush Diameter (mm)
EDP
Material
D1 Shank Diameter (mm)
D2 Sleeve Diameter (mm)
L1 Overall Length (mm)
L2 Shank Length (mm)
L3 ShAft LeNgth (mm)
Matching Brush (EDP)
Product Number
List Price
6
40006
- Aluminum
6
10
70
29
41
S06M
$52.10
15
40007
- Plastic
6
18.5
90
29
61
S15M-P
$94.74
25
40004
- Aluminum
8
30
140
30
110
S25M
$225.29
40
40003
- Aluminum
10
45
140
30
110
S40M
$242.24
60
40002
- Aluminum
12
65
150
35
115
S60M
$631.65
100
40001
- Aluminum
16
110
162
40
122
S100M
$1,010.63
Matching Brush Diameter (mm)
EDP
Material
D1 Shank Diameter (in)
D2 Sleeve Diameter (in)
L1 Overall Length (in)
L2 Shank Length (in)
L3 ShAft LeNgth (in)
Matching Brush (EDP)
Product Number
List Price
6
40006
- Aluminum
0.236
0.394
2.756
1.142
1.614
S06M
$52.10
15
40007
- Plastic
0.236
0.728
3.543
1.142
2.402
S15M-P
$94.74
25
40004
- Aluminum
0.315
1.181
5.512
1.181
4.331
S25M
$225.29
40
40003
- Aluminum
0.393
1.772
5.512
1.181
4.331
S40M
$242.24
60
40002
- Aluminum
0.472
2.559
5.906
1.378
4.528
S60M
$631.65
100
40001
- Aluminum
0.630
4.331
6.378
1.575
4.803
S100M
$1,010.63
Additional Brush Styles Available
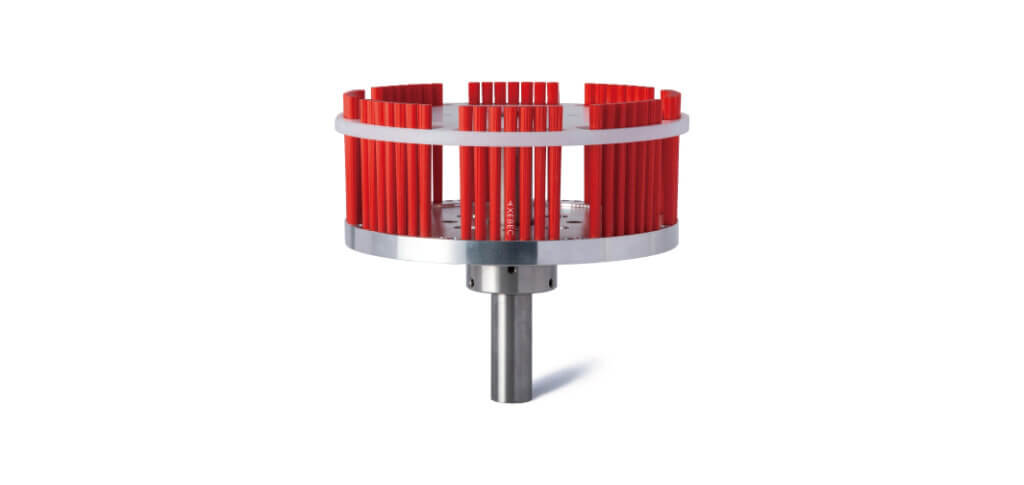
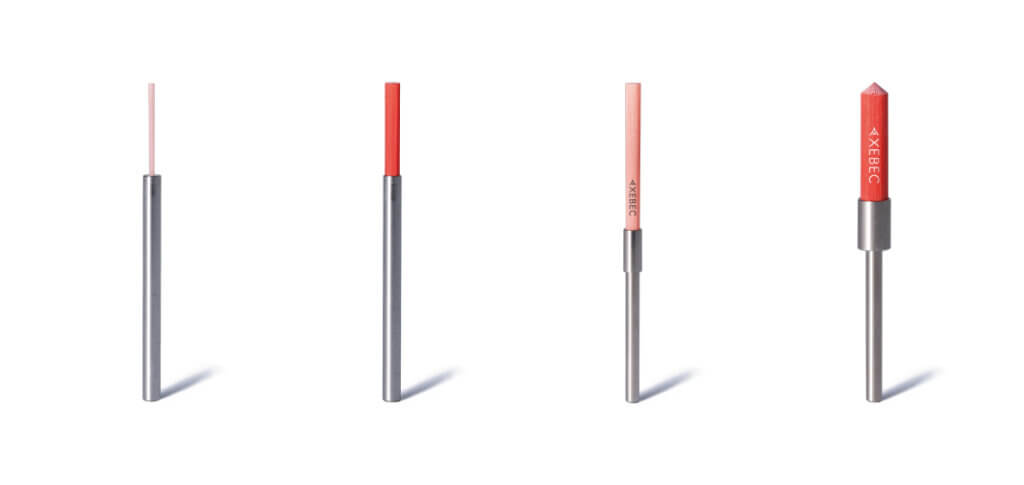
How to Select
How to Choose Brush Color
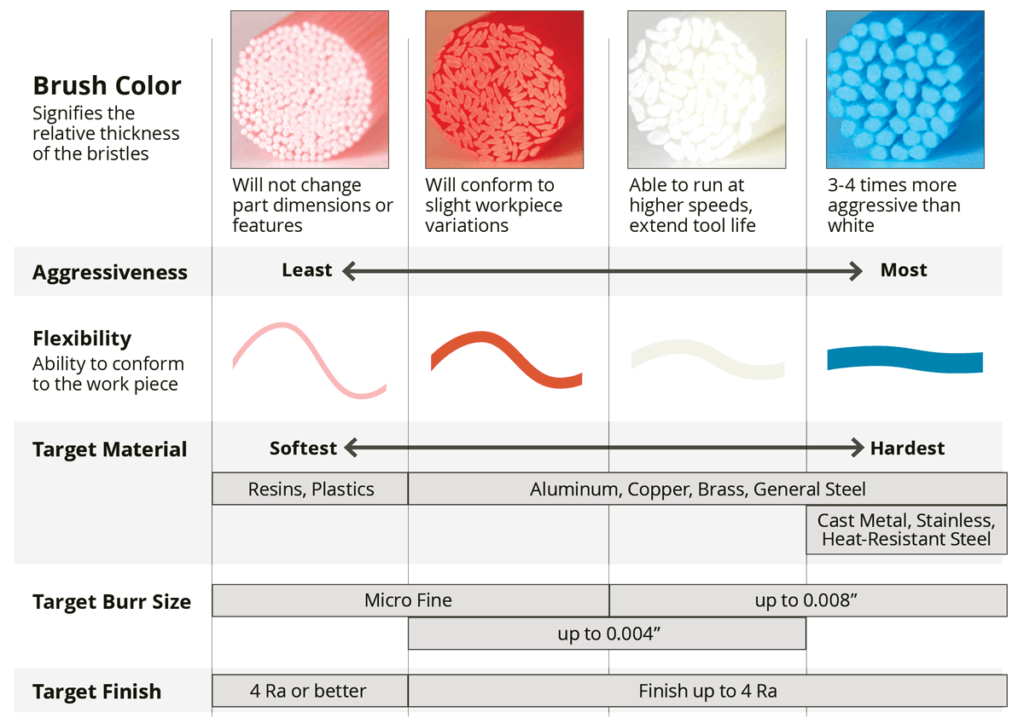
Target Burr Size
Burr Root Thickness of 0.008” or less (Burrs can be bent with a fingernail)
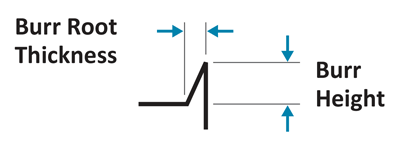
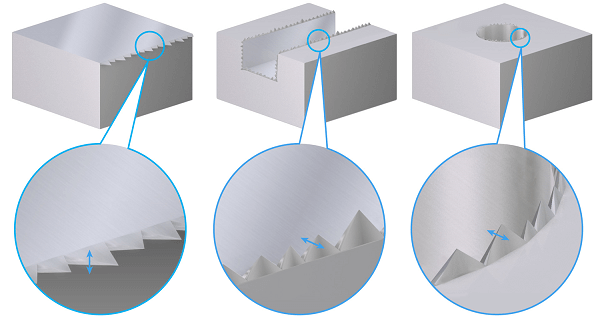
How to Choose Brush Size
Select a brush size based on workpiece size and shape, interfering objects such as jigs, attachable tool length and cycle time.
It is recommended to use a brush size which is 1.5 to 2 times wider than the width of the surface of the workpiece. This allows the brush to engage the edge at 90 degrees for optimal grinding power. Using a larger brush than the surface width will also require the fewest number of passes and minimize cycle time.
Structures of Xebec Ceramic Fiber

The XEBEC Brush™ uses abrasive ceramic fiber material instead of abrasive grain. One single bristle consists of 500 -1,000 ceramic fibers that works as cutting edges, providing excellent cutting ability.
The XEBEC ceramic fiber has 3 features that enable CNC deburring & polishing:
- Unsurpassed Grinding Power
- Consistent Cutting Performance
- No Deformation
Strength 1: Unsurpassed Grinding Power
Our uniquely developed ceramic fibers themselves are the abrasives and its fiber content ratio is over 80%. Cutting edges that are made up from the tip of each fiber bristle create unsurpassed grinding power.
XEBEC Brush™ has 60 times higher grinding power compared with nylon brushes and steadily removes burrs.
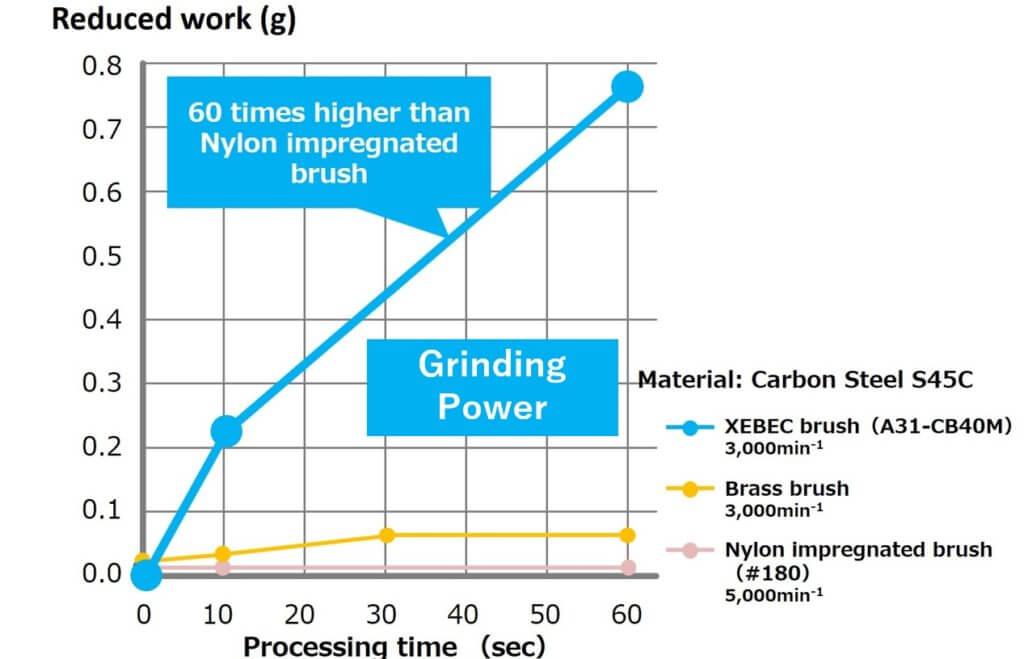
Strength 2: Consistent Grinding Power to the End

Strength 3: No Deformation
XEBEC Brush™ maintains its straight shape and does not spread out like a toothbrush even after repeated use. Thus, it is ideal for CNC deburring and polishing in mass production line.

Amazing Polishing Power
XEBEC Brush™ is made of ceramic fiber bristle which was developed for mold polishing. Its high grinding power improves surface roughness in a short time.
Best achievable surface roughness Ra=0.1μm (Rz = 0.4μ)

Target
XEBEC Brush™ has high grinding power on the tip. The brush tip needs to be in contact with the processing area. Both vertical and horizontal burrs after drilling or end milling can be removed by setting up the depth of cut.
Avoid coming into contact with a protruding part because it may damage a brush.
Applicable Equipment
It is necessary to control the rotation speed to use XEBEC Brush™. The tool can be used on machining centers, combined lathes, robots, special machines, and drilling machines.
Assembly
XEBEC Brush™ Surface and XEBEC Sleeve are separate items. Two hexagon socket set screws are included with the sleeve. Attach the brush to the sleeve and fix it with the set screws from both sides.
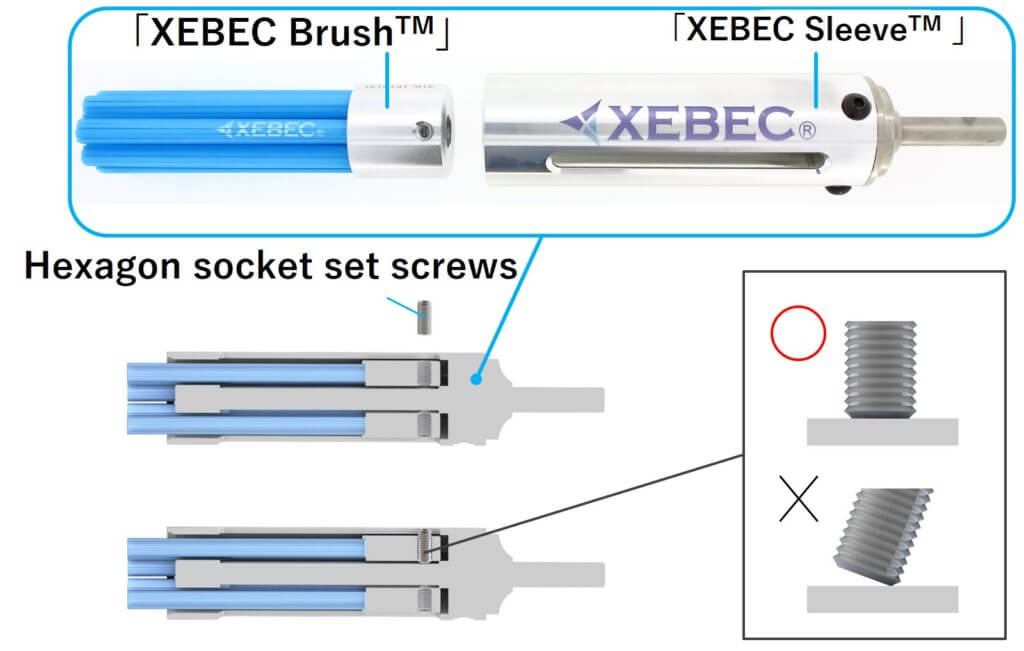
Process Conditions
Set the processing conditions depending on the purpose: deburring or cutter mark removal and polishing.
Deburring
Set the following 5 conditions:
- Rotation Speed
- Depth of Cut
- Feed Rate
- Brush Projected (the length of the brush projected from the sleeve)
- Direction of Brush Rotation
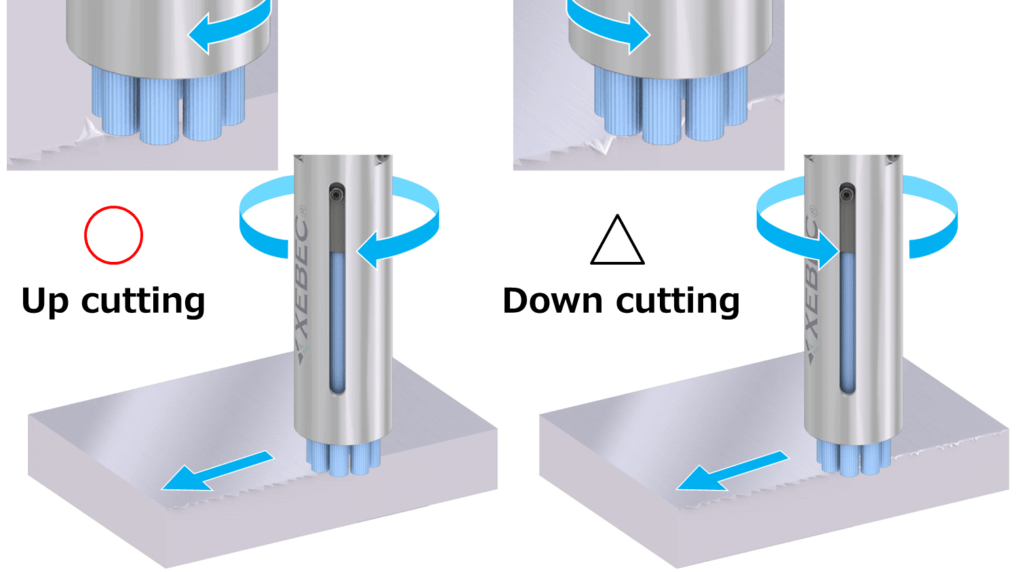
Rotation Direction
Rotational direction of the brush has significant impact on the deburring capability.
For burrs in horizontal direction (i.e. side burr) generated after milling, the machining must be done by up cutting whereby the brush pushes upward against the burrs from the bottom.
When down cutting, there is a possibility that the burrs may not be removed properly because the burrs being bent and stuck to the surface.
For vertical burrs (i.e. top burrs), there is no significant difference by rotation direction.
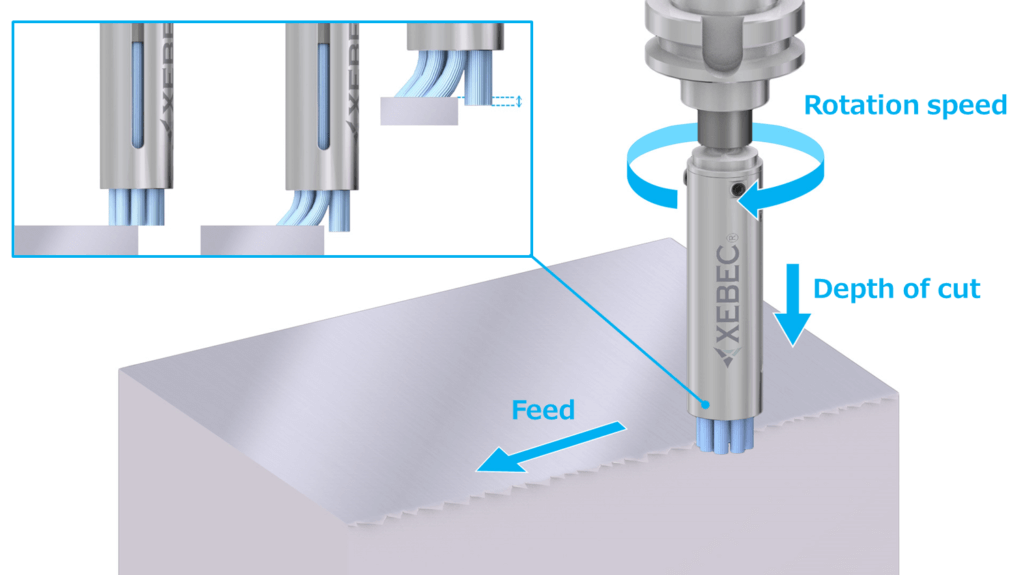
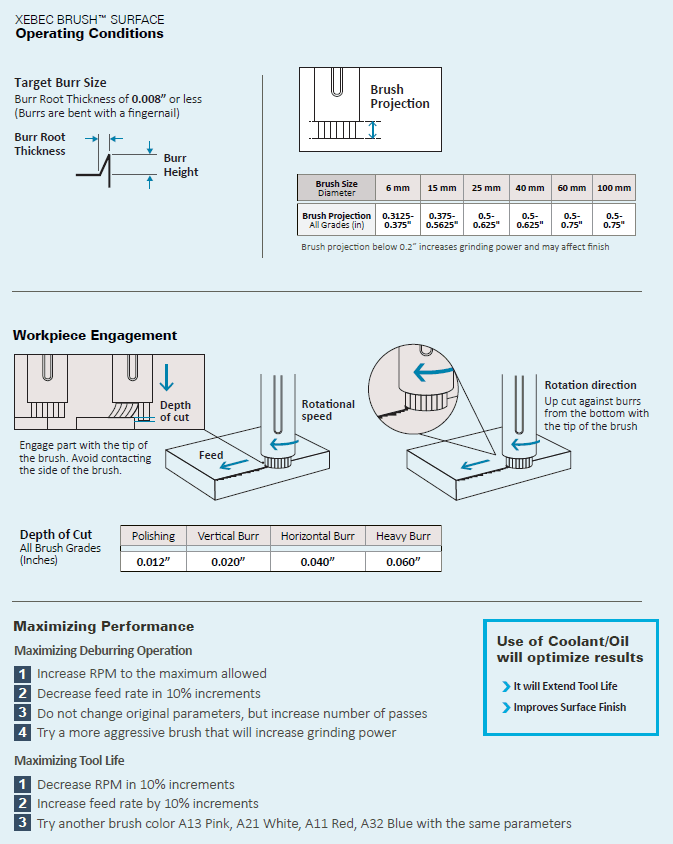
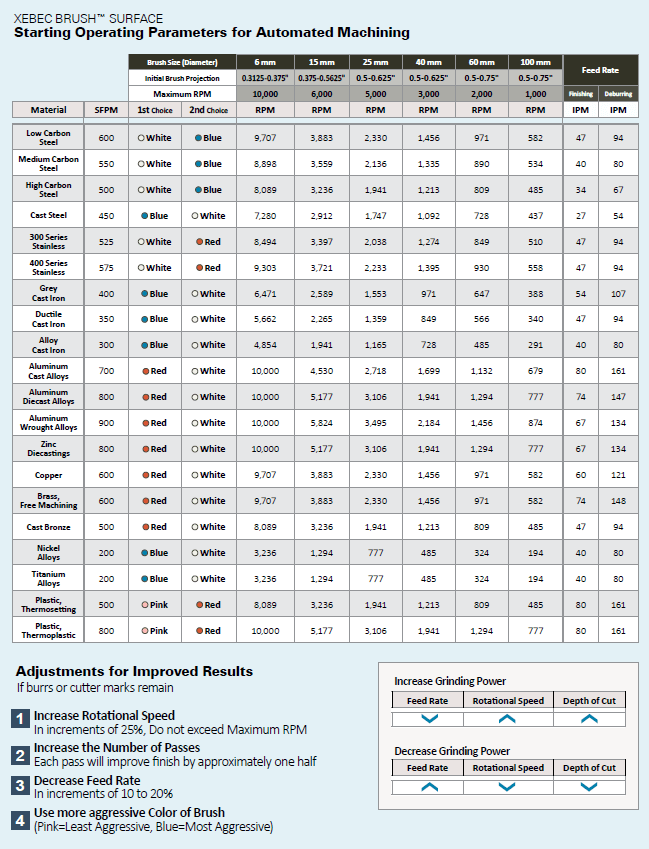
Initial Processing Conditions
Set the initial conditions according to burr direction (top burr or side burr) and burr size (root thickness burr).
Product Code
Depth of Cut D
Vertical Burrs
Horiztontal Burrs
Rotation Speed S (Min-1)
Recommended Rotation Speed
Maximum Rotation Speed
Feed Rate F (MM/Min)
Burr Root Thickness 0.05MM
Burr Root Thhickness 0.1MM
Brush Projection (MM)
A13-CB06M
0.5
0.5
8,000
(MAX10,000)
4,000
2,500
10
A13-CB15M
1.0
1.0
4,800
(MAX6,000)
4,000
2,500
10
A11-CB06M
A21-CB06M
A32-CB06M
0.5
0.5
8,000
(MAX10,000)
4,000
2,500
10
A11-CB15M
A21-CB15M
A32-CB15M
0.5
1.0
4,800
(MAX6,000)
4,000
2,500
10
A11-CB25M
A21-CB25M
A32-CB25M
0.5
1.0
4,000
(MAX5,000)
4,000
2,500
15
A11-CB40M
A21-CB40M
A32-CB40M
0.5
1.0
2,400
(MAX3,000)
4,000
2,500
15
A11-CB60M
A21-CB60M
A32-CB60M
0.5
1.0
1,600
(MAX2,000)
4,000
2,500
15
A11-CB100M
A21-CB100M
A32-CB100M
0.5
1.0
960
(MAX1,200)
4,000
2,500
15
If burrs remain, increase the rotation speed to the upper limit.
If burrs still remain, then decrease the feed rate.
If the workpiece cannot be deburred even by the 2 above-mentioned procedures, the machining condition may be incorrect or the burr size is too large.
To extend tool life/If the edge is too rounded: Decrease the rotation speed in increments of 1,000min-1. If tool life or edge quality is still not improved, the machining conditions or the brush color may not be appropriate.
The grinding power of the brush is in the order of: Red < White < Blue.
Truing
When the brush is worn out unevenly, you can form the tip of the brush using a diamond disc blade. Use drilling machine or lathe.
Truing by Drilling Machine
Truing by Lathe
If you want to cut off the brush, cut from the side of the brush using a diamond disc blade and sever it.
Operator Safety Measures
For Protective Equipment
Always wear protective goggles, gloves and masks when operating the tool. Wear long sleeves, tight cuff, and clothing to minimize skin exposure.
Beware of Grinding Powder
Grinding powder and burrs may scatter within an area around the work as the brush revolves; please stay clear of this area.
Be Aware of Your Surroundings
The area around your work is hazardous in case flying pieces of fiber rods from the tools and grinding powder may scatter, enclose your working area to prevent other people entering, or have the people surrounding your work area protective equipment as well.
Warning
By not following the above safety measures, you are vulnerable to the following risks:
- A tool or a part of a tool may crack, drop off, distort or break.
- Broken pieces of a tool or grinding dust may stick into your skin and eyes, causing irritation and/or blindness.
- Dust generated by machining process may cause allergic reactions.
No, it does not. The ceramic fibers work as abrasive materials.
For the cup type, attach the shank of the sleeve to an automatic tool changer (ATC) on a machining center or other equipments. Then rotate the tool and remove burrs after cutting work on machine. It can also be used with robots, special machines and drilling machines.
For the end type, attach the tool to an electric tool (or machine tool). It can not be used with a pneumatic tool.
The tool aims to remove burrs with the size that can be bent by pushing one’s fingernail against it.
The cup type brush can be used for chamfering or rounding an edge.
The tool can be used for both dry and wet (both oil-based and water-soluble) machining.
Wet machining may improve surface finish quality and tool life.
The brush is capable of surface finishing, and it can improve surface roughness to around Ra=0.1μm. XEBEC Brush™ is developed by applying the technology for XEBEC ceramic stone which is used for mold polishing. It does not contain any abrasive grains,thus the brush does not leave any scratches on the surface. However,depending on the pattern of the brush, there are cases where the appearance looks a little cloudy on aluminum surface which was finished with a diamond cutter.
XEBEC Brush™ does not define the grits. It is capable of finishing the surface up to around Ra=0.1μm.
Tool life significantly varies depending on machining conditions, burr condition (size and direction) and workpiece material.
In one case study, where the tool was used for deburring after milling of an oil pan with 1m circumference (material:aluminum), a single brush lasted for 10,000 workpieces (straight line distance of 10,000m=10km)
Example:
Workpiece: Oil Pan (automotive engine part)
Material: Aluminum
Cutting process: 1m / piece
Result: 10,000 workpieces / brush (total length 10km)
The end type brush can be used for hand work. However, the cup type brush can not be used manually because it judders violently. Furthermore, the appropriate depth of cut cannot be kept when using the cup type manually, so deburring and polishing cannot be done suitably.
Remove the attached dust or coolant by blowing air, etc.
You can form a brush using a diamond disc blade.
Yes, it is possible. XEBEC’s genuine parts are recommended. Contact us for the details.
The inner part of the tip of the sleeve is worn out and become thinner as it is gradually ground by the sides of the brush over a long period of use. Replace the sleeve.
It is possible to purchase the outer cylinder of the sleeve alone. Contact us for the details.
It is possible to produce a brush that is shorter than the standard specification. However, it is not possible to provide shorter metal parts (i.e. sleeve, shank).