Turbine blades are popular parts in the aerospace industry. Just one aircraft engine can have upwards of 1,000 turbine blades. For this application, precision and quality are critical to ensure each blade performs safely and efficiently.
Currently, some of the most common methods of finishing turbine blades involve a belt sander. The part will either be hand-finished with a belt sander, or the belt sander will be automated in a separate specialized machine.
Both methods require that the operator move the turbine blade from the CNC machine to another station to hand-finish or machine separately. Both methods also require that the part is already finished to an Ra of 100µin (microinches) to be worked by the belt sander.
Moving and handling parts between phases adds time to production processes. It also runs a higher risk that the part will be damaged or there will be errors from one setup to another. Additionally, reducing a part to an Ra of 100µin so it can be machined by a belt sander adds time, as this work is tedious and must be achieved carefully.
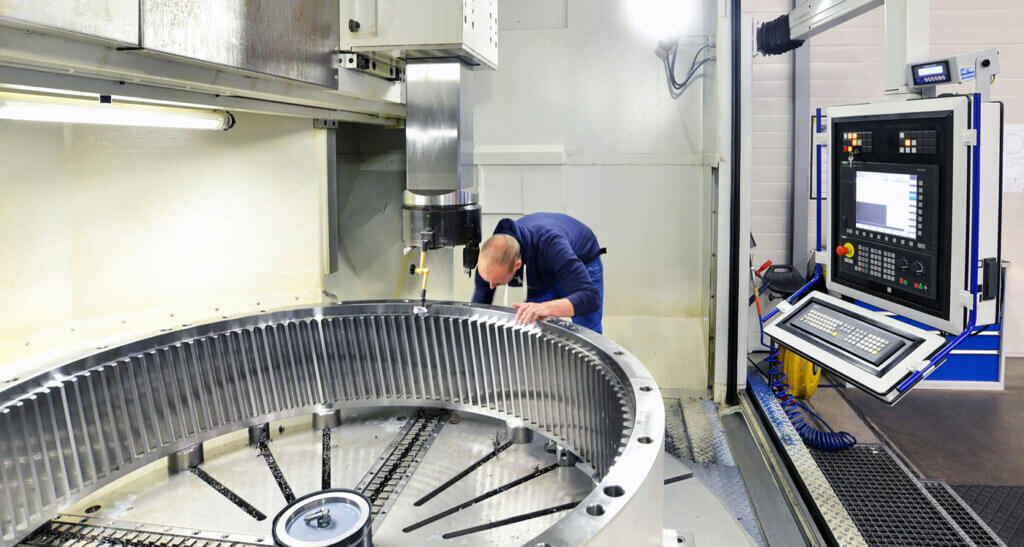
For many manufacturers, these issues might seem like necessary trade-offs. Machining a turbine blade can be trickier than other parts due to its curved surface. Finding an alternative that is more efficient can seem like a wild goose chase.
Fortunately, the team at Xebec Deburring Technologies has a proven method ready to go. We understand the importance of these parts, and we also see the forecasts predicting growth for the aviation industry. Considering what’s ahead, it’s easy to see the value of improving how you finish turbine blades – with the advice and guidance of application specialists who know all the tricks to getting it right.
Automating turbine blade finishing in your CNC machine with Xebec tools will result in:
- Faster production
- Greater consistency
- Improved quality
- Reduced scrap and rework
- And more
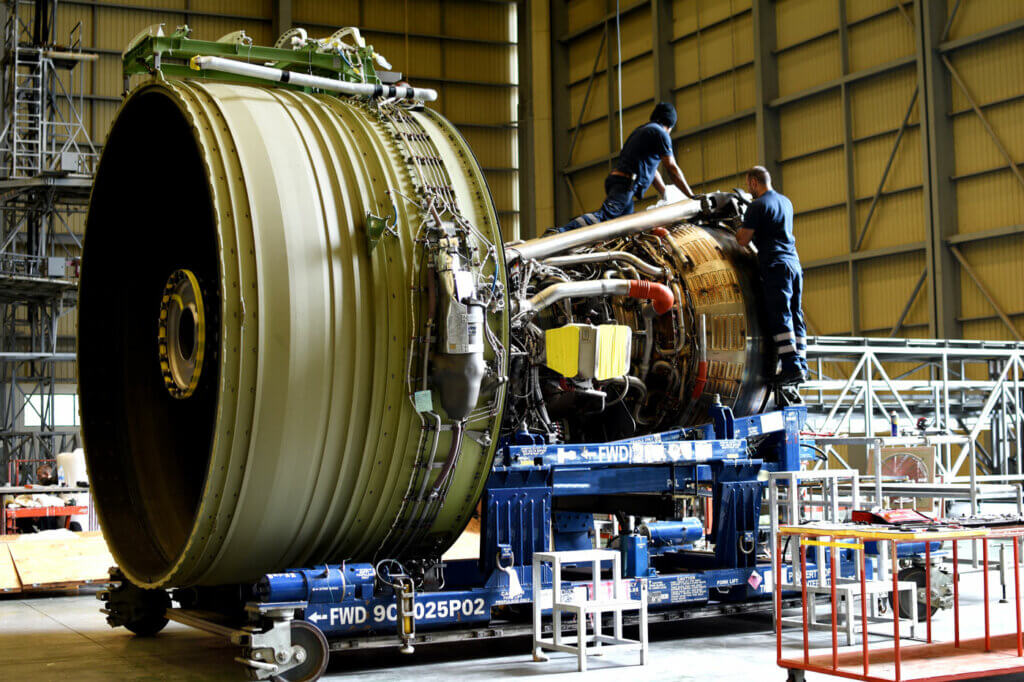
The Xebec Brush Surface Does the Trick for Turbine Blades
The Xebec Brush Surface is a deburring brush that is proven to produce quality results efficiently in turbine blade applications.
A Tool that Performs
The Xebec Brush Surface performs like a cutting tool and achieves precise results consistently. This is due to its continuous ceramic fiber bristles, which set this tool far apart from alternative automated deburring brushes. Some of the most important characteristics of this brush that will appeal to manufacturers of turbine blades are:
- Incredible grinding power, with which our brush performs more like a cutting tool than your average deburring brush.
- Consistent cutting performance, which means more reliable results and reduced chance or scrap or rework.
- No deformation, which is why the performance can be so consistent and the tool can accomplish such work.
These are the characteristics that make the Xebec Brush Surface capable of both removing the cusp after cutting and polishing the blade’s curved surface. It’s these curved surfaces that have always made the most trouble for manufacturers, and why they are hesitant to modernize the process. Old-fashioned belt sanding techniques may be reliable, but there is a more efficient and consistent method available now using Xebec tools.
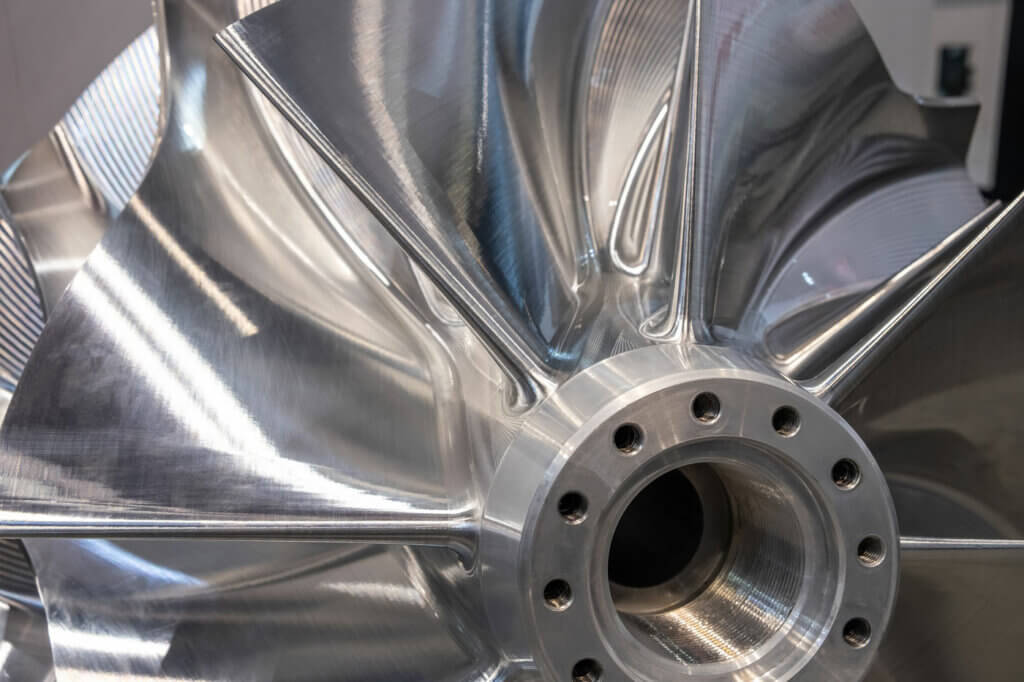
Xebec brushes do not require the low Ra of 100µin that a belt sander requires. Blue and Red Xebec brushes can finish a part from an Ra of 200µin and take the surface roughness down as low as 3.9 µin. This saves time on the machine, which would be spent trying to achieve the Ra at a slow and careful pace.
Additionally, automating finishing in the machine means you won’t have to spend time moving the turbine blades from the machine to a hand-finishing station or separate machine.
Finally, Xebec brushes perform faster than alternatives, shaving minutes off processes.
This adds up to cost savings as much as it does time savings. The time you don’t waste is like money back in your business, that you can invest elsewhere and grow with. However, depending on your current process, you’ll also save on the costs of:
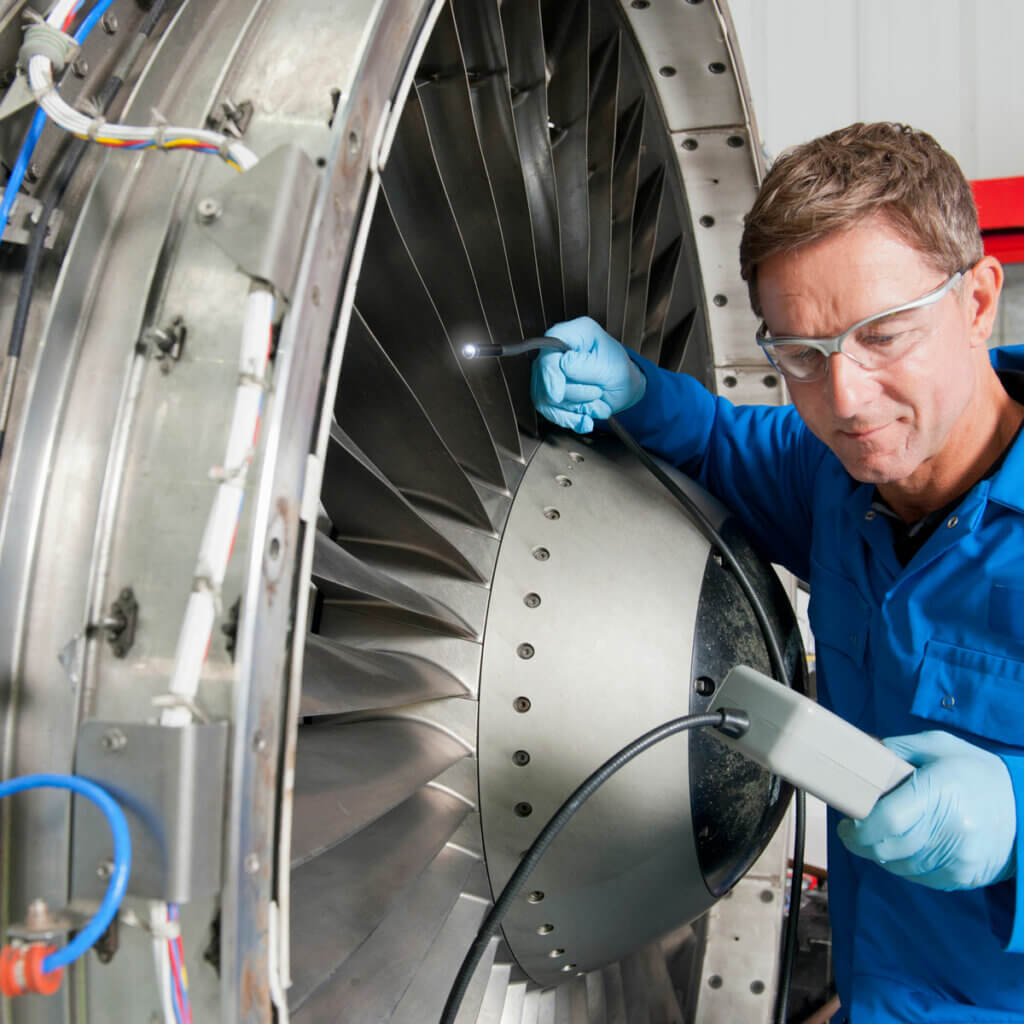
- Purchasing and maintaining a separate specialized machine
- Maintaining a hand-deburring and -finishing department
- Scrapping or reworking parts that are damaged or improperly finished
- Injuries resulting from manual processes or handling parts
- Missing production deadlines due to inconsistency and quality concerns
- Losing customers to shops and facilities that can more readily meet tight expectations
A Method that Works
Xebec has developed an effective method to achieving optimal results. We work with our customers to implement our tools into their Mastercam, showing them how to use our proven method to get an excellent finish. Our process recommends segmenting out the surface into convex, concave and edge R, using three brushes to ensure proper performance and achieve the appropriate shape.
We can help you get the process right by using a specific direction and angle of approach for curved surfaces, and carefully calculated depth of cut, speed and infeed. Let us help you using our proven formula and we can guarantee success in your application.
If you’re interested in implementing our tools to produce turbine blades or other aerospace parts, please contact our team to explore the finer details of the process.
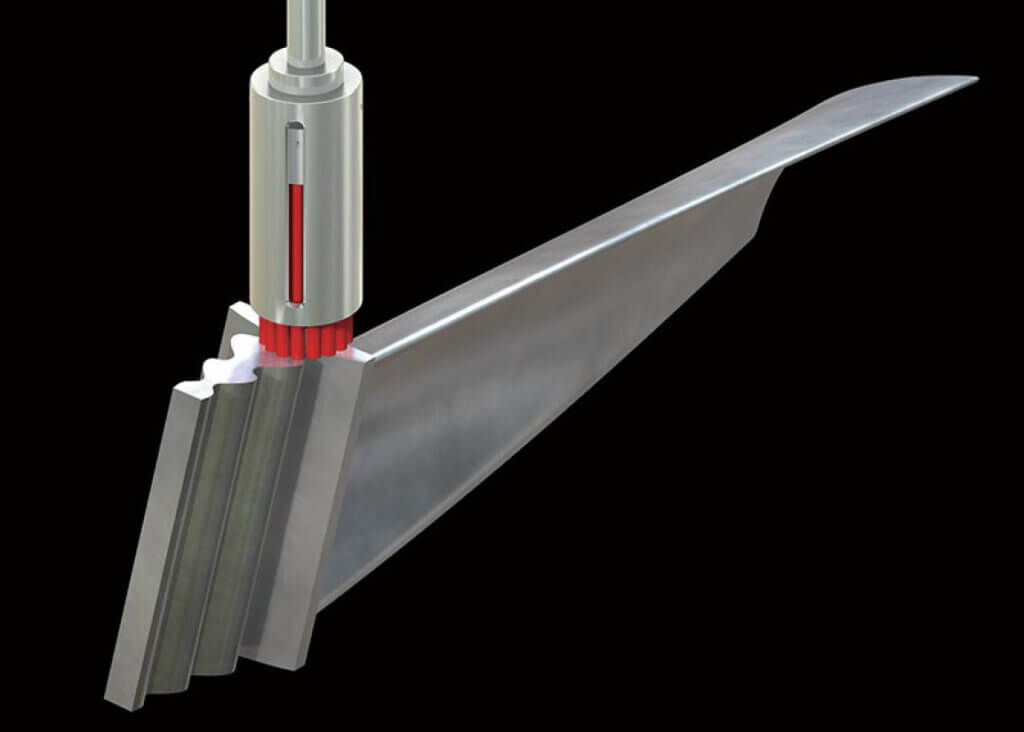