A recent study by the Workforce Institute of UKG reveals that 63 percent of manufacturers surveyed are “struggling” to find qualified labor for essential roles and 23 percent are “really struggling.”
Manufacturers can often outsource work where they have critical gaps. They can also improve inefficient processes and invest in technologies that automate tasks, improve speed and reduce inefficiencies.
For example, Xebec ceramic fiber brushes that operate like a cutting tool can automate manual deburring and finishing processes. This helps solve labor concerns for staff shortage in the deburring and finishing department or in other short-staffed areas if workers can be reallocated.
This is also a prime example of a third tactic manufacturers can employ to combat the labor shortage: upskilling and reskilling. Often, there is untapped potential within manufacturers’ ranks. You can provide employees opportunities to gain new skills, certifications and degrees so they can move up or change course as your company evolves structurally, technologically and otherwise. Here, we’ll discuss how manufacturers can do more with what they have by upskilling and reskilling their existing employees.
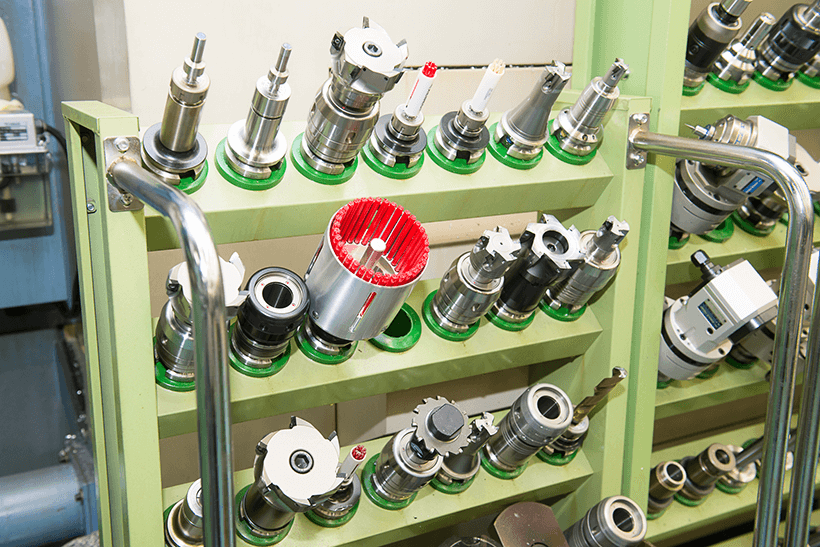
Why upskilling is a top solution for manufacturers
In many instances, upskilling involves more than a one-week training program. It can be a lengthy process – and it typically demands a financial investment. So, besides filling gaps as needed, what else should motivate manufacturers to pursue this more intensive track?
Employee loyalty
When you invest in your employees and take their growth seriously, they are more likely to reward you with loyalty and dedication. So long as your culture is also supportive, you can retain their respect – and employment. Consider that the pandemic revealed a clear difference between the cultures of manufacturers’ office staff and frontline staff. Employers must be mindful to ensure equality in the workplace.
Employee retention
Employees leave companies for various reasons, including personal needs, lack of progress in their role, burnout and higher costs of living. Investing in their growth helps them progress and pursue higher pay at your organization. And avoiding burnout keeps employees happier and healthier. An overworked workforce often leads to turnover and low productivity.
Technology onboarding
Upskilling and reskilling go hand-in-hand with introducing new technologies that improve processes and operations, from the office computer to the shop floor. Planning to upskill will help manufacturers onboard industry 4.0 technology and prepare for the next iteration. Combining these technologies with upskilling will translate to less overtime and less chance of burnout, and it will keep employees in your workforce even as technology takes over some of their duties.
Reduced overtime
Manufacturers are paying extensive overtime to meet demand as the labor shortage continues. And two-thirds say it is affecting their bottom line, according to the Workforce Institute at UKG study. The study reports, “in March 2021, production lines were understaffed or overstaffed more than one-third of the time.” With upskilling and strategic technology investments, manufacturers can even out their labor needs. Employees will be less overworked, and payroll will be more on-budget.
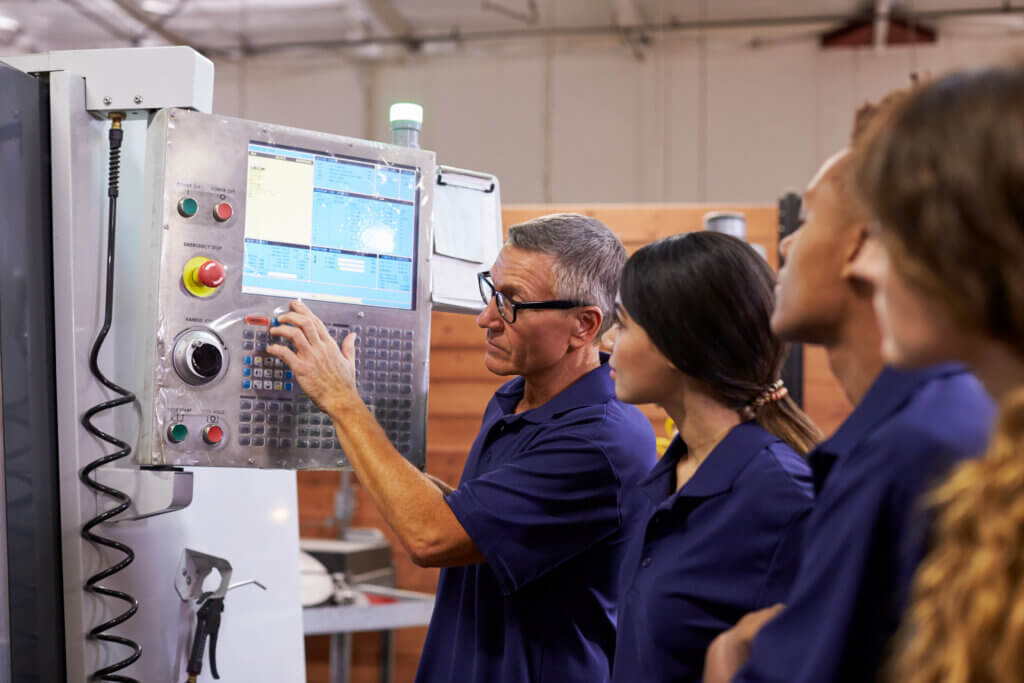
Strategies for upskilling in the manufacturing industry
The Workforce Institute at UKG reports that manufacturers’ top recruiting challenges are:
- Finding talent with the ideal skillsets
- Competition for talent
- Having a strong pipeline for skilled talent
- Getting available jobs in front of skilled talent
- Determining the best hires from candidate pool
Upskilling and reskilling can help counter most of these challenges, as can using diverse recruiting tactics like hiring and training non-traditionally skilled candidates and offering apprenticeships to candidates. Here’s a look at strategy options for both recruiting and upskilling to deal with these challenges:
Internship: Employee receives educational and hands-on experience in a role, such as engineer or supply chain management expert.
Mentorship: Newer employees are connected with long-time employees to learn. Thirty-three percent of those surveyed provide mentorship programs.
Apprenticeship: Employee is paid as they learn hands-on and by-the-book how to perform the role. For instance, you might provide a four-year apprenticeship program for a machinist either internally or using outside support and resources.
Manufacturers can access resources that support these initiatives through associations, colleges and other programs. These programs make the process easy, and you often have the option to do the training at your facility or at the college or association. If you’re already providing opportunities like these but you don’t have a formal process, consider implementing one. Employees will appreciate official certifications and such offerings will appeal to candidates.
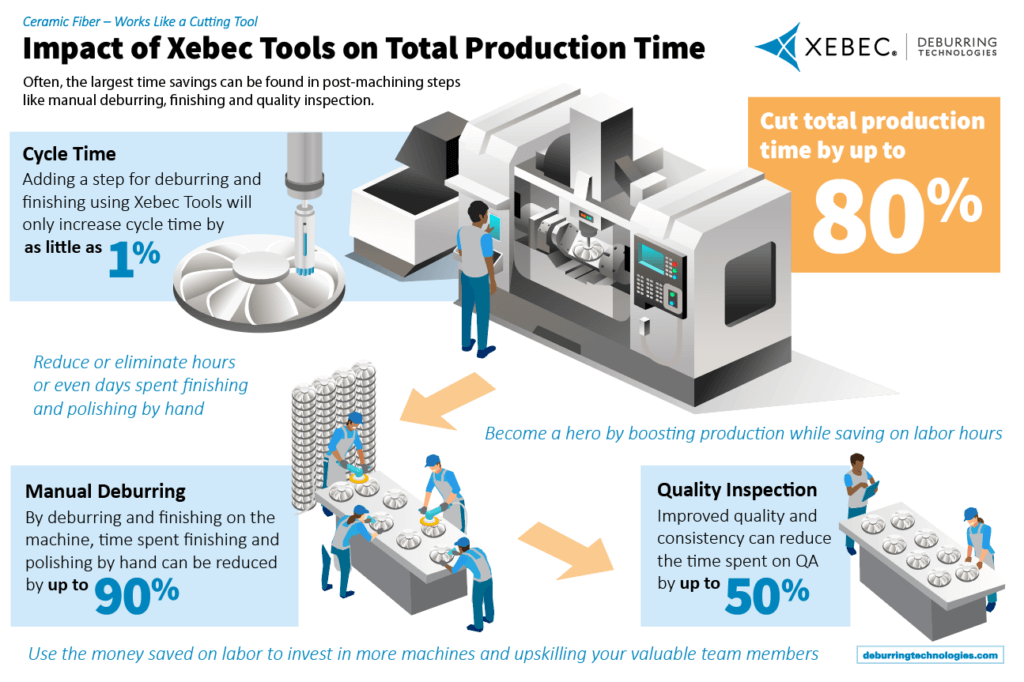
Xebec products as step one in an upskilling strategy
To get to upskilling so you can reallocate employees to where you have critical gaps, you may need to introduce technology into processes that keep employees stuck in redundant activities. Automating one time-consuming task can make a big difference.
Xebec Deburring Technologies can eliminate the need for hand-deburring and other deburring or finishing activities that otherwise occupy employees for hours of their shift, days of their week, and even full-time. This frees up those employees to pursue new skills and grow at your organization. They can enter into an apprenticeship or other training program to become a CNC operator, machinist, engineer or quality control specialist.
For example, with the Xebec Brush Surface, one firearms industry customer was able to reduce manpower on a task that once required six full-time employees, whom they could then redeploy to other tasks. And in the converse, if manufacturers are using over-skilled staff, such as CNC operators or engineers, to do manual tasks such as hand deburring, automating the process lets them concentrate on their work.
Here’s a look at the hierarchy of responsibilities and associated qualifications at a typical shop working with CNC machines that could incorporate automated deburring and finishing:
- Manual machine operator (Drill presses): High school diploma or equivalent
- Machinist: High school diploma or equivalent
- CNC Operators: High school diploma with 2 years of experience
- CNC Programming: 2-year degree
- Engineers (Manufacturing, Mechanical): 4-year degree
According to the Workforce Institute at UKG, most manufacturers report that employees skilled to manage a range of responsibilities are more productive, cross-training enhances organizational focus. And their frontline managers are fully capable of helping employees upskill.
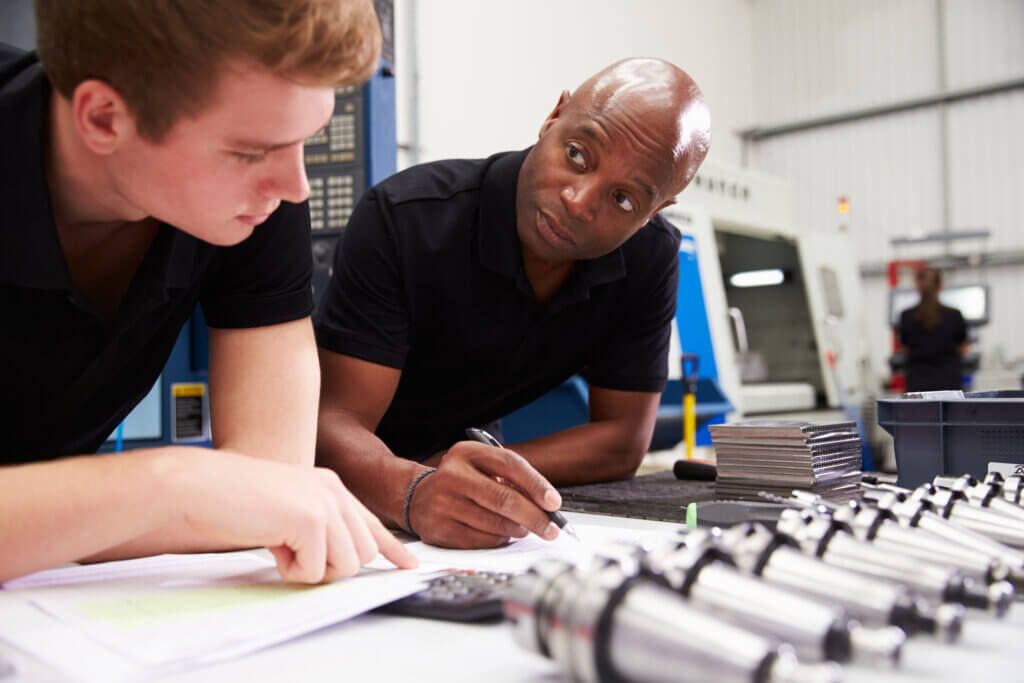
Evaluate your upskilling potential
Upskilling may be a good idea in general, but that doesn’t mean it’s a fit for every manufacturer – or even feasible. Ask yourself and your team members:
- Is your staff interested in growing and learning new skills? Your employees may enjoy their roles and prefer not to change.
- How will you find the time and resources to train and reskill current employees? There are programs you can outsource to as a manufacturer, or you may prefer to certify in-house.
- Which roles do you need to fill? Identify where your gaps and opportunities are, and which employees might be the best fit.
- What role can/does technology play in your next steps? You might plan to automate a process to move an individual out of a manual, redundant role into a role that requires more critical thinking and a broader skillset.
- Can you afford to sit on such investments as the labor shortage endures? According to the recent Workforce Institute at UKG study, 63 percent of manufacturers are already working on reskilling employees and 60 percent are cross training.
Xebec Deburring Technologies supports training efforts on Xebec products. We can help you upskill your staff and introduce transformative technologies, reach out to one of our experts.