High quality deburring used to be an art. The Xebec deburring team has it down to a science.
Designing a manufacturing process for a part means engineers must factor for several tasks, objectives and parameters. Even if you produce similar parts from one job to another, each has its own shape, material and complexity. The change-over is rarely cut and dry.
Each new job starts with mapping out the material, machine(s), tools, post-machining requirements, projected cycle times and anticipated job cost. All this is done with an eye on optimizing timing, cost and efficiency for maximum productivity and return on investment (ROI).
If you determine that an automated deburring tool is ideal for the job, you might research your options, reach out to one of your reps, purchase a tool like the Xebec Surface Brush then think you can simply plug it into your process.

Let’s pause.
Don’t overlook the key benefit of using Xebec products:
Our knowledgeable team of application experts is available to help you plan, design and implement Xebec deburring tools in your processes – and to support your use of our tools in the future.
Your team knows its way around programming, so you’ve likely chosen the right technology and designed an appropriate process to get the job done. However, we often find that our experts, based on years of experience in manufacturing settings, could’ve enabled your engineers in designing an optimal process had we been consulted sooner. Often, by the time we are contacted, the production is set up and adjustments must be made. Or you may have already run a few parts and encountered issues.
Sometimes, customers can’t find the time to put their Xebec tool to use. So, it’s sitting in a drawer somewhere. We also run into situations where manufacturers outsource programming due to labor constraints, making the design process a step removed from the manufacturing floor.
We can help – from step one. Our team can consult with you on planning, design, implementation and proper tool usage. We’ll help test and problem-solve, and we’ll be available to support you after implementation. And we recommend you take us up on it.
Why?
Because we want you to be successful.

If it’s a simple question you need answered, you’ll find instruction manuals and other handy information on our Specs Page. However, every new application requires a different approach and our team can help you identify the best tools, speed and feed for your needs. Xebec deburring tools are different in all the best ways and they can be your secret weapon if you work with our experts to optimize their application.
We know how to apply Xebec solutions so they’re effective, repeatable and long-lasting. Our team is always eager to roll up their sleeves, help you strategize and teach you to use these advanced tools we’re all so proud of – saving you time, resources and headaches.
These Aren’t Your Average Deburring Brushes
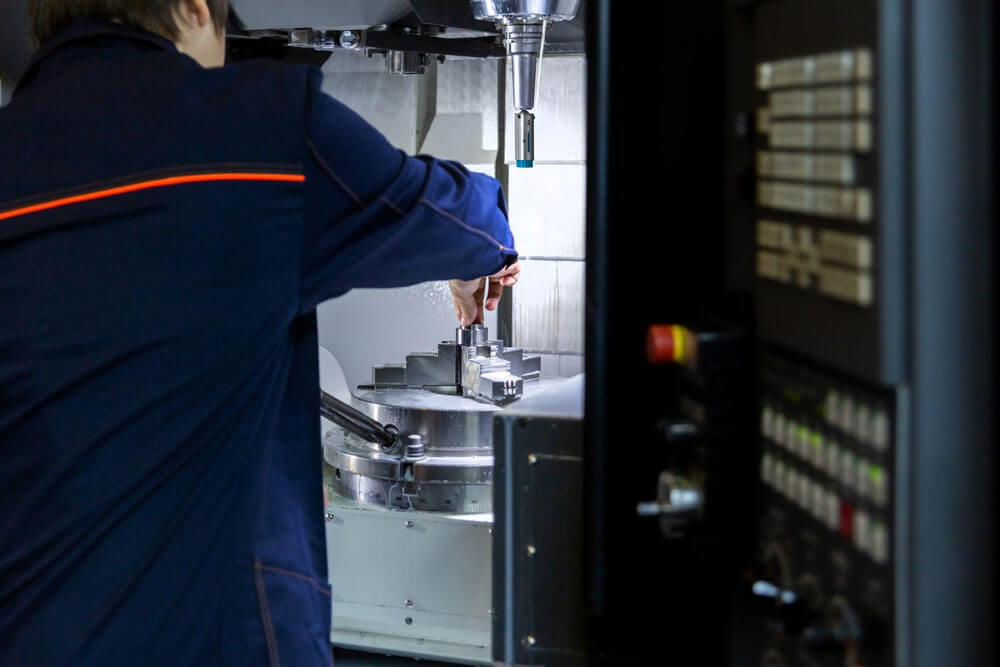
Xebec deburring solutions don’t just outperform alternatives – they’re in a category of their own. It’s not a one-to-one swap if you’re replacing another brush type, and you must adjust your program designs to fit.
That’s because Xebec ceramic fiber brushes perform more like cutting tools. Their proprietary continuous ceramic fiber bristles have sixty times higher grinding power compared with nylon brushes and the patented Xebec sleeve supports and reinforces their strength.
It’s critical that these tools aren’t run like nylon brushes. They have their own optimal feeds and speeds relative to the application, machine and material. It’s best to request guidance from one of our team members.
For example, let’s say you’re using a 10-inch nylon impregnated brush and you want to switch to a Xebec ceramic fiber brush. One of our experts might advise using a 25-millimeter Xebec brush, with which you can accomplish the same work in half the time. If you’ve never worked with our tools before, it would be more challenging to determine the proper alternative on your own. And even then, you’re working with a much smaller brush with different run requirements.
What Could Go Wrong?
According to an article in Modern Machine Shop, process mistakes are among the top three reasons CNC programs fail. Process mistakes could include processing with the wrong depths of cut, speeds and feed rates. The article illustrates, “If cutting conditions are too aggressive, cutting tools will wear out quickly or break. If they are too conservative, efficiency will suffer.”
Other issues that might cause your program to fail include:
- Using the incorrect tool for the application
- Issues with part positioning in the machine
- Miscalculation and programming errors due to lack of skilled team members
- Vibration or “chatter” during production
These issues could lead to part and equipment damage, reduced quality, reduced tool life, rework and scrap.
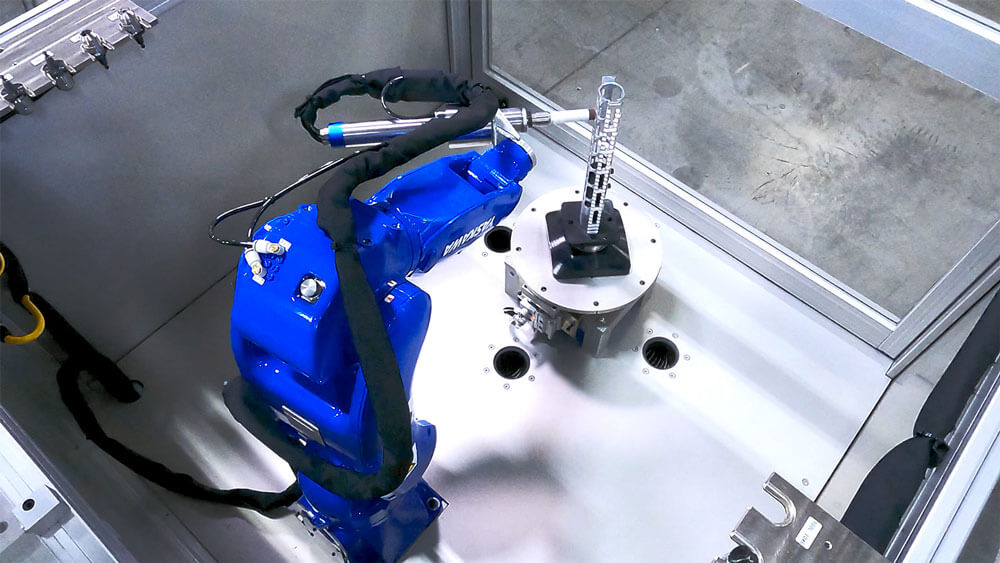
What Guidance Do We Offer?
Our team can help with everything from tool selection to proper tool usage, implementation, testing, troubleshooting and support. We can advise as to:
Controlling burrs before deburring: If you can optimize the direction, size and amount of burrs produced during the machining process, deburring itself will be faster and more efficient, and you’ll extend the life of your deburring tools.
Properly applying the deburring and finishing tool: Xebec tools have tremendous potential, but sometimes they’re programmed sub-optimally for the application, limiting their capacity for repeatability, reliability and quality. Proper deburring tool usage is key, and our experts are eager to help engineers accomplish this.
Working specific materials: Different materials respond differently in the machining process, and Xebec tools don’t operate the way similar looking brushes do. Xebec products are more like cutting tools. Our reps know how to guide programming for different materials, so you can accomplish exact specifications confidently.
Choosing, retrofitting or upgrading machines: In most cases, manufacturers can program Xebec tools on existing machines. However, there might be a high-ROI opportunity to upgrade or retrofit your machines to achieve optimal outcomes with automated deburring and finishing. Or you may even consider incorporating robotics or additive manufacturing processes. Not to mention the opportunities that arise to increase efficiency when it comes to resource allocation and upskilling once you have this machine and an automated process.

Conclusion
We want to have a conversation and work with you from the start to help with the application as a whole, not just deburring and finishing. We want to know:
- What are you trying to accomplish?
- What kind of machine are you using, or are you working manually?
- What type of material are you working with?
Such a collaboration will help us identify the right tools and applications for the job. We know our tools, and we’ll be able to determine how to approach the job more readily, so you can get on with production, results and cost savings.
>> Don’t leave us out of the process:
Tap the Experts at Xebec to Design a More Efficient Machining Process
Contact us: Tell us a little bit about your application and any issues you may have and one of our experts will get back to you. We’ll be happy to discuss how we can help you maximize productivity and quality, demonstrate what we can do, and guide through the selection and implementation process until a successful test run is accomplished.