Back deburring complex edge profiles, curved holes and 3D cross holes can be challenging. However, with the Xebec Back Burr Cutter and Deburring Tool Path combined, engineers and operators can confidently automate such processes in their CNC machines.
The Xebec Back Burr Cutter is designed for these specific processes. Its spherical cutter can deburr both sides of the front and back of cross holes. And it can be automated in either a CNC machine or combined lathe. Further, the data path can be programmed and customized such that one cutter can deburr various hole shapes. Use this tool on hundreds to thousands and millions of holes. With Xebec you can expect great results for any of the following hole types:
- Angled
- Broken
- Flat
- Off-center
- Orthogonal
- Slotted
- Threaded
- Irregular/Complicated (custom)
The Xebec Deburring Tool Path is customized to your job by Xebec application experts and, once it’s created, you’re off to the races. Forget trial and error; forget sub-par timing and outcomes. Whether or not the edge profile you’re working with is complex, our experts can design a data path that will help you achieve high-quality results, faster and more efficiently, and with a longer tool life than you’d see without the Deburring Tool Path.
Dig deeper into use cases for the Xebec Back Burr Cutter and Deburring Tool Path. >>
The Trouble with Programming Trial and Error
Programming this one-of-a-kind tool on your own to achieve the quality you expect isn’t as simple as other cutting tools. It involves accounting for the unique spherical blade design and ensuring the cutting edge continually shifts. It requires time to calculate the geometry and is difficult to accomplish with accuracy and reliability. There are a number of ways the process can go wrong without our guidance, and we can’t guarantee the performance of the tool when you program it on your own. This is the reason we offer the Deburring Tool Path in the first place – so we know the Back Burr Cutter will work the way it was designed.
Our application experts know the unique geometries of the cutter. Personally ensuring the Path is made correctly is the only way we can offer out-of-the-box, burr-free performance – guaranteed.
With the combination of the Back Burr Cutter and the Deburring Tool Path, you’ll see benefits beyond what’s happening in the CNC or lathe as far as accuracy and reliability. Programming and testing absorbs time, which means labor costs as well as lost opportunities to use that time more productively – an especially important factor considering the labor shortage and the cost of a programmer’s time. Then, once the programming is in play, your operators would likely have to go back and forth troubleshooting to get the right results – more time and labor, as well as scrap and rework. All of that to end up with a path that ultimately falls short of expectations.
You may find that once you calculate the cost of this time, labor, scrap and rework, it comes up far short of the cost of a Xebec Deburring Tool Path.

Benefits of the Xebec Deburring Tool Path vs. DIY Data Path
The Xebec Deburring Tool Path is the real key to success. It’s rare that manufacturers are able to design a sufficient path for the Back Burr Cutter – but our Path is 100% reliable, accurate and ready to run from the start. Our team has years of experience integrated into programming the path data file specific to your application.
The path data can be used as soon as it’s installed on a CNC program, saving you time. Not to mention the down time you’d have spent trying to troubleshoot or fine tune your own program. The Xebec created Deburring Tool Path comes with a guarantee from Xebec – we will work with you to ensure it works exactly as it should for your application. Once you’ve run the CNC with the Deburring Tool Path, you’ll sit back and wonder why you ever went without it.
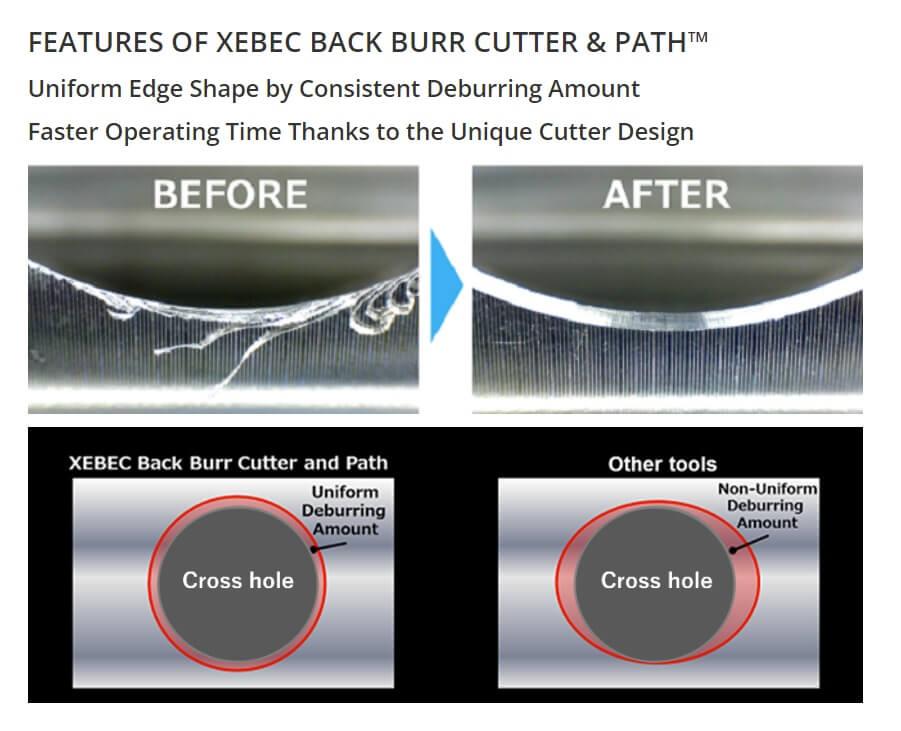
Get More Life Out of the Back Burr Cutter
The Deburring Tool Path ensures the Back Burr Cutter uses the entire cutting edge to help you get every ounce of use and productivity out of the tool. It does so by continuously shifting where the cutter contacts the workpiece. Customers report incredible results going from their own path design to the Xebec Deburring Tool Path.
→ In one instance, a customer used the Deburring Tool Path with the Back Burr Cutter on a Motorcycle Hydraulic Component made of Alloy Steel. They found tool life quadrupled compared to their former data path:
Before: They could deburr 1600 holes prior to the formation of secondary burrs with the Back Burr Cutter.
After: With the Path, they could deburr 6,400 holes.
In the beginning, I only purchased the Back Burr Cutter and created the tool path with CAM. However, upon hearing that their Deburring Tool Path helps improve the tool life, I decided to purchase it and try it. The result was amazing! The tool life quadrupled!
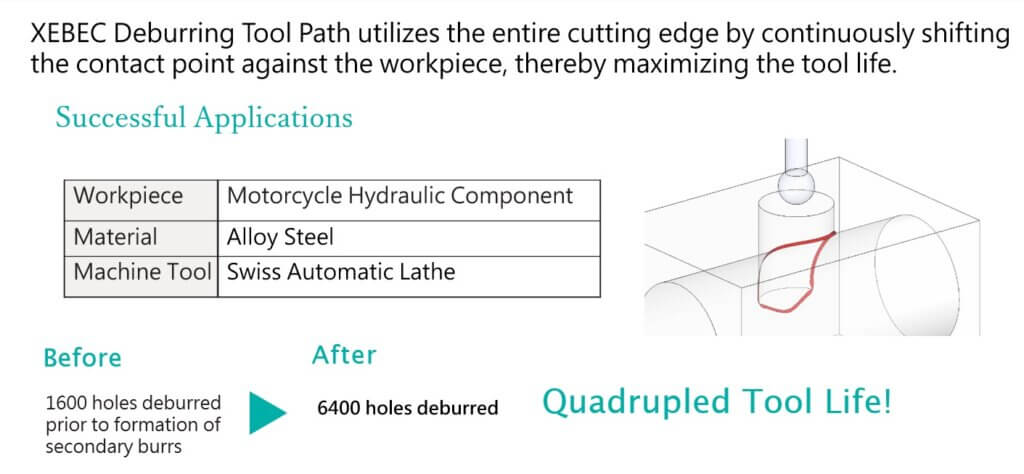
→ Another customer experienced 4.2 times longer tool life using the Path with the Back Burr Cutter on an Alloy Steel Automotive Part.
Before: They could deburr 100 holds prior to the formation of secondary burrs.
After: They could deburr 420 holes.

Save Time and Effort on Implementation
As we mentioned up top, using the Deburring Tool Path means your operators won’t have to program and troubleshoot the path to get optimal results.
For instance, one customer used the Path on an Alloy Steel automotive part in a machining center and saw major improvements.
Before: It took hours to program the tool path and the customer had to make corrections to the tool path using trial and error.
After: With the Path, the customer didn’t have to program OR correct the path. As the customer stated:
We spent several hours to program tool paths for simple cross holes. For cross holes with offsets and for angled cross holes, it was necessary to spend a day. However, only a few of our engineers are capable of this, and they are always busy with other tasks. XEBEC Deburring Tool Path solved these difficulties, because they deliver the optimal tool path that can be used right away that requires no corrections!

Achieve Optimal Cutting Angle that Improves Edge Quality
Importantly, the Deburring Tool Path ensures the process does not produce secondary burrs. This is because it’s designed to approach at an optimal cutting angle, contouring the target edge. This means superb edge quality with every run.
For example, one customer was having issues using their own path on an Alloy Steel automotive part in a machining center, which created secondary burrs. “We needed to remove them manually, thinking that it was unavoidable with a 3D-curved edge like this,” the customer said. With the Deburring Tool Path, however, secondary burrs no longer formed.
Starting to believe the Xebec Back Burr Cutter and Deburring Tool Path will work for your specific cross hole projects?
See how to choose the best cross hole deburring tool for your application. >>
Ready for Your Own Path?
Have any questions on the Deburring Tool Path? Check out our FAQs page on the XEBEC Back Burr Cutter & Path™.
Now that you’re inspired to improve your deburring processes, see if the Xebec Back Burr Cutter and Deburring Tool Path will work for your process using our free online assessment, or reach out to discuss your operations with one of our experts.