When equipment breaks down at your manufacturing facility or machine shop, the solution is pretty cut-and-dry: repair or replace. You can even gauge how long it’ll take to be back up and running. So, though there are consequences such as costly downtime and the upfront expense, there’s a clear solution and timeline.
If only all manufacturing challenges had such clear solutions.
Today, manufacturers face a long list of challenges that are like perennial thorns in their sides, appearing unsolvable and insurmountable. For instance, there’s pressure to embrace the future of manufacturing, but first they must determine which investments will actually pay off for their business.
There’s also continued volatility and uncertainty in the cost and availability of raw materials, making it difficult to price jobs accurately and ensure profitability. There are many challenges in job costing for CNC machining centers and these issues involve variables outside of a manufacturer’s control.
These more stubborn and taxing challenges in manufacturing can lead to production headaches. Since you don’t have as much control over them, it can seem like they’ll never go away.
However, you might be surprised to learn that your entire shop can get noticeable relief by changing one process: How you deburr parts. If you manually deburr parts at your facility, we’re sorry to say that you might be standing in your own way. Automating this process can make a significant difference, helping you both embrace the future of manufacturing and reduce job costs. Importantly, it can provide relief from three of manufacturing’s most pressing, headache-inducing concerns:
- Finding adequate skilled labor amidst labor shortages and manufacturing skills gap.
- Embracing automation at pace with the industry – and where it counts.
- Using automation for deburring and finishing to keep quality staff during business lulls
- Retaining a supportive environment for employee health, safety, morale and stability.
1. Skilled Labor Shortage in Manufacturing
Finding skilled labor is a major issue across the industry. It causes headaches because many companies are in the same boat and there isn’t a simple solution.
If the talent pool is limited, how do you find the right people and make them an attractive offer? If the talent isn’t there to recruit, how can you develop it yourself? If the next generation isn’t pursuing manufacturing careers, how can the industry build more excitement around needed roles? And what about those roles soon to be emptied as highly skilled staff enter retirement?
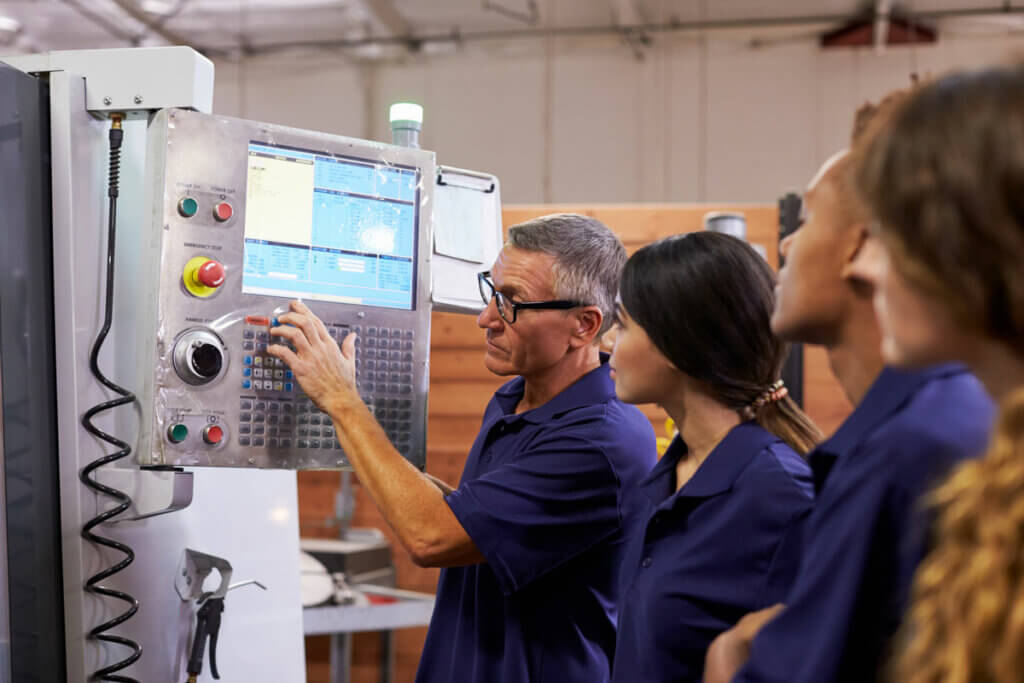
According to the Deloitte and The Manufacturing Institute 2022 Manufacturing Perception Study, while 83 percent of Americans consider manufacturing very important to economic prosperity, only 66 percent consider manufacturing careers interesting and engaging. And only 64 percent feel that future manufacturing jobs will provide more opportunities for career progression.
To add to frustrations, there is an element of mystery around why the labor shortage has persisted. Studies are being conducted to get to the “why,” but it’s hard to make a strategy when there are so many unknowns and the ask is so steep. If your production is slowing down, you may find your employee turnover increasing as skilled workers leave for other opportunities where they don’t have to do manual deburring and finishing tasks.
Yeah, we get it. Our heads hurt too.
Solution: Attract and Upskill the Skilled Labor You Need
Manual deburring and finishing are tedious, time-consuming tasks that absorb labor and time from your resources. When you automate the process with Xebec deburring solutions, your employees gain time back from performing it manually.
Manufacturers also see time savings for labor dedicated to the setup process. This is because, with Xebec’s deburring tools, both deburring and finishing occur at once while the part is still in the CNC machine. With this, you can realize one or both of the following:
- Fill in where labor is short. If you’re struggling to staff the deburring and finishing department, automating the process eliminates the issue.
- Reallocate to where skill is needed. If you’re struggling to staff other roles in production, you can take staff off manual deburring and finishing and upskill with training and hands-on experience to fill those needed roles.
- Make the job easier by removing the difficult work of hand-deburring or dealing with transporting and disposing of large quantities of substrate in less efficient tumbling processes.
2. Application of Automation in Manufacturing
There’s an expectation for digital transformation and automation in almost every business function at manufacturing companies, from finance to operations and supply chain management. All are essential to compete as agility becomes more imperative and expectations for speed, throughput and quality tighten.
It takes a lot of mental gymnastics, math and forecasting to sort which investments should take priority. And many business leaders find even these activities are limited by manual methods and spreadsheets.
>> Learn More: Automated Surface Finish Processes for Manufacturing
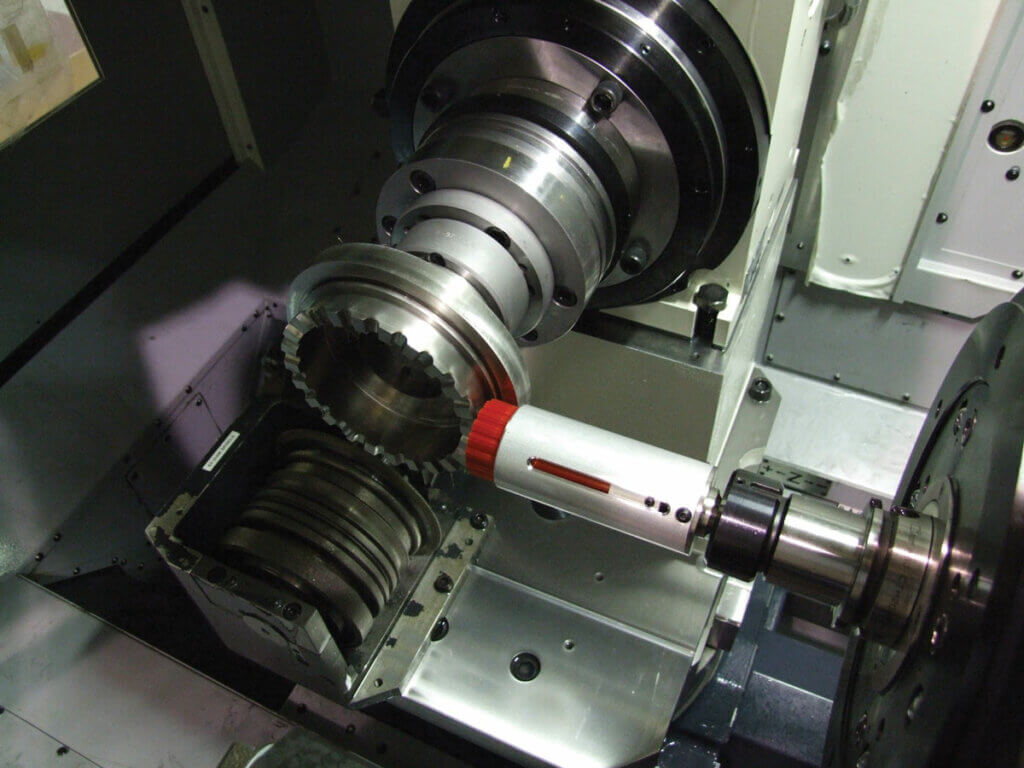
Solution: Automate Where the Return is High
When the call to automate in manufacturing is so broad, it’s difficult to choose the best first step. The results we’ve seen manufacturers realize automating their manual deburring and finishing processes prove that this step belongs on your priority list. Manufacturers in a number of industries already use our products, such as aerospace, firearms, energy, medical, powertrain and more.
With our tools in your processes, you can improve operations, reduce costs and overcome several lean manufacturing challenges:
- Increase production capacity and throughput. Xebec products deburr and finish parts faster and more efficiently than manual processes and nylon brushes. You’ll be able to increase throughput on your machines, allow operators to run multiple machines at once and reallocate staff to other tasks.
- Meet high standards for consistency and quality. Xebec ceramic fiber performs like a cutting tool and delivers consistent, high-quality finishes. It has a longer tool life than other options in the market and won’t deform, an issue manufacturers experience using nylon brushes.
- Save on high cost of manual processes. Some of the most common concerns manual deburring and finishing are those that have associated costs, such as inconsistency and poor quality leading to costly scrap and rework.
- Use Robots and Cobots. Robotic arms automate deburring and finishing across industries, enhancing precision in automotive, aerospace, medical and general metal or non-metal fabrication. Collaborative robots (cobots) offer flexibility, easy programming and enhanced safety, making them ideal for small-batch production and close human collaboration.
- Meet strict specifications for clean rooms. Xebec deburring tools generate minimal debris and produce high-quality finishes without additional cleanup, helping manufacturers maintain strict clean room requirements and quality standards for industries like medical, aerospace, and semiconductors.
3. Manufacturing Worker Safety
Worker safety and morale have always been priorities in manufacturing. Safety is a daily challenge considering the types of work and materials involved. Additionally, the COVID-19 pandemic recreated new expectations to protect the health and safety of employees via practicing social distancing, providing sufficient PPE and truly abiding by the rule that employees should stay home if they feel sick – without penalty.
Morale and employee stability are challenges in any industry. Employees typically want to feel they are progressing in their roles, and manufacturers must work to design mindful career paths with training, support, and a safer workplace.
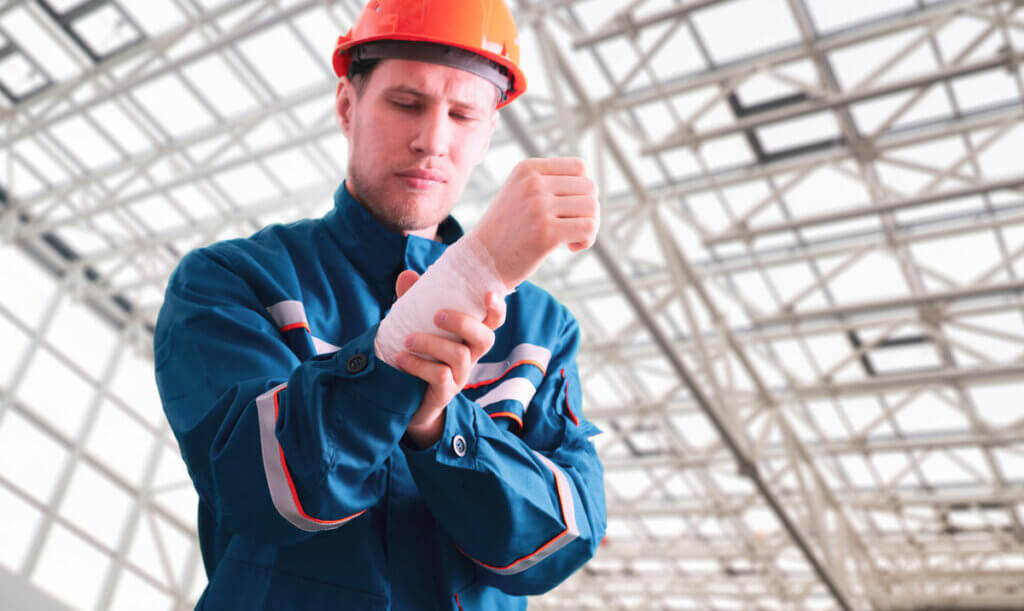
Solution: Reduce Risks and Strenuous Activity
Manual deburring and finishing metal can be dangerous and strenuous. The risks of making an error and or being slightly distracted ending up with an injury aren’t insubstantial. Then, there are injuries incurred over time from continuous motion. And working on large pieces calls for twisting and contorting, while working on small and complex parts requires close-up focus. Additionally, there’s potential for injury from metal shards.
- Improve employee health and safety. Automating this process takes it out of human hands to eliminate these risks. Employees won’t have to do perform the continuous motion or contortion these tasks often require, and there won’t be risk of injury due to metal shards.
- Maintain a desirable work environment. When you improve safety on your shop floor, you are investing in your employees, and they will recognize that. Their jobs won’t be as taxing and physically strenuous, and they’ll know you’re looking out for them.
Automating deburring and finishing with Xebec tools promotes these goals as it alleviates the risk of injury handling heavy parts with sharp edges and manual deburring with risky, and often jerry-rigged, tools. Xebec can help improve morale and retain skilled employees by automating tasks that are seen as punishment instead of craft in today’s machine shops.
If you’re ready for modern deburring at your company, be sure to grab our guide to doing so.
Have questions for us? You’re likely wondering what makes Xebec products different and how to determine the right deburring method for your application. Contact our experts who are the secret to deburring success. They are available to take your call or email and answer your questions.