Are you concerned about injuries in your manufacturing facility?
It’s a critical issue because manufacturing has the highest injury rates of all industries. That’s why safety training, protocols and investments are so important to manufacturing leaders. Any investment in employee safety that prevents injuries is worthwhile. When that investment also improves production efficiency, eliminates certain production headaches and solves modern manufacturing challenges, like automating otherwise hazardous processes, it’s a no-brainer.
An automated deburring tool is a prime example of such an investment, especially if you choose a Xebec product. In fact, along with increased productivity, employee safety is one of the most common reasons manufacturers implement Xebec tools. Automating deburring and finishing in your CNC machine or robotic process with Xebec tools eliminates several risks related to performing this work manually, including ergonomic injuries, cuts and lacerations, musculoskeletal disorders and more.
Beyond safety, replacing a manual process with Xebec automated deburring tools also improves consistency, quality, productivity, costs, throughput and more.
Learn more about quality improvements with Xebec over manual deburring. >>
If your employees are deburring and finishing parts by hand and they haven’t been injured or overexerted themselves, knock on wood. Then, evaluate your processes to see whether they’re truly as safe as they can be.
- What types of tools and equipment are employees using?
- Are they making their own, non-standard deburring tools?
- What are the conditions of their workstations?
- Do they have to hold uncomfortable positions for extended periods?
- Are they performing strenuous repetitive motions?
- How close are they to the workpiece and equipment?
- What level of exposure to dust particles do they experience as they work?
You’ll likely find several red flags in your evaluation – and those red flags disappear when you move the deburring and finishing processes onto your CNC machine or into a robotic operation. Xebec deburring and finishing tools are ideal for these processes.
>> Watch the automated deburring and polishing with the XEBEC Crosshole Brush:
Xebec’s cutting tools are made with continuous ceramic fiber. This unique material allows for high performance grinding power, consistent performance and superior surface finish. The fibers are formed into bristles for brushes or bound into stones. Self-sharpening tips lead to superior grinding performance.
The Xebec Back Burr Cutter and Deburring Tool Path is designed with a spherical cutter to easily deburr complex edge profiles, curved holes and 3D cross holes. And it can come with a pre-programmed, customized data path and be automated in either a CNC machine or combined lathe.
As you evaluate, be sure to check your processes against OSHA standards.
Get our ebook to learn how to modernize processes to overcome manufacturing challenges. >>
What Are the Dangers of Deburring and Finishing by Hand?
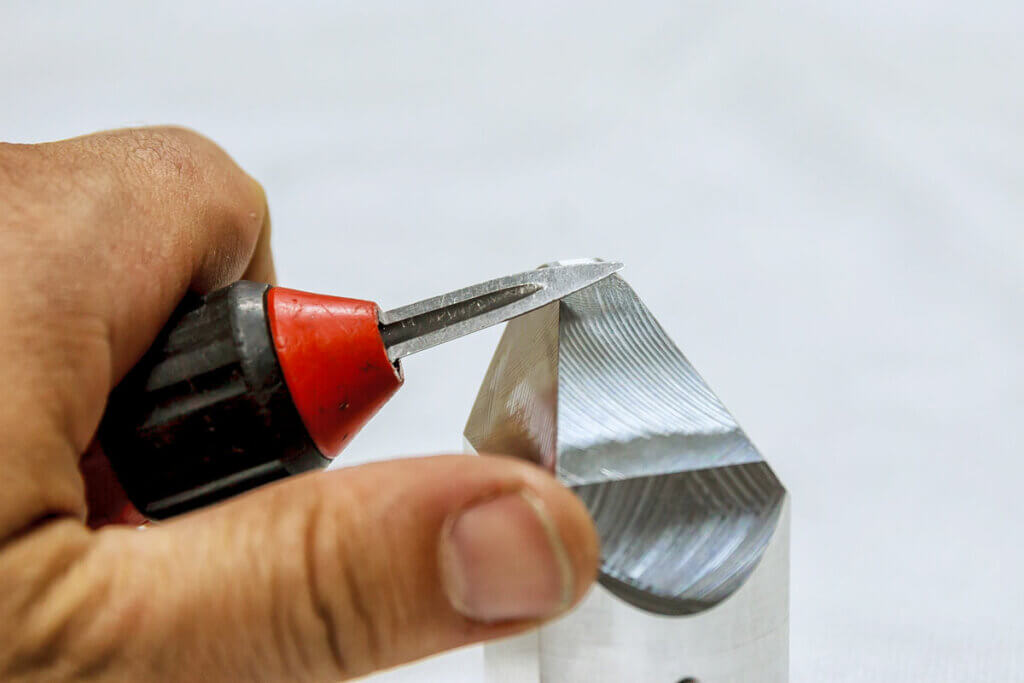
The hazards related to manual deburring and finishing are astonishing. Yet, these processes have always been essential in metalworking.
It’s only in recent decades that automated deburring and finishing tools have come on the market. So, not all manufacturers and machine shops have been able to capitalize on them just yet – but there’s no better time than now to consider the dangers of deburring metal and other materials manually. Especially when products like Xebec deburring tools eliminate these dangers altogether.
Hazardous Manual Deburring Tools and Equipment
Hand-deburring tools themselves present safety concerns unless your operators are using innovative tools like Xebec’s selection of hand-deburring tools and accessories. Common tools and equipment used in hand deburring that can be hazardous to employee health include:
- Files
- Handmade tools
- Craft knives
- Sandpaper
- Handheld deburring tool, curved blade, scraper
- Abrasive, grinding stones
- Wire brushes
- Flap wheels and abrasive disks
- Countersink tools
- Bench and angle grinders
- Pneumatic pencil grinders
- Chamfering machines
- Saws
Handling these tools, working near the equipment and parts, and performing repetitive motions all create opportunities for accidents and injuries. That’s especially the case when using handmade tools.
- Handmade tools are untested and unreliable. They present a variety of hand-deburring hazards, such as coming apart while in motion, especially when paired with a power tool.
- Some pneumatic air tool options do not have a gauge for speed, so the speed depends on the pressure applied. And their general lack of controllability is a safety concern. Consider the dangers of sandpaper at a high speed in an uncontrollable application.
- Flap wheels and grinding discs tend to break apart over time, and the debris could lead to cuts, lacerations and other injuries.
- Files, carbide blades and sharp craft knives used by hand on metal parts commonly lead to hand and arm injuries.
If you’re unable to automate these processes, consider upgrading to more reliable, safer tools like Xebec’s hand-deburring solutions. These tools are more controllable and safer in the close-up work of hand deburring. However, automating these processes can eliminate the dangers associated with using manual tools.
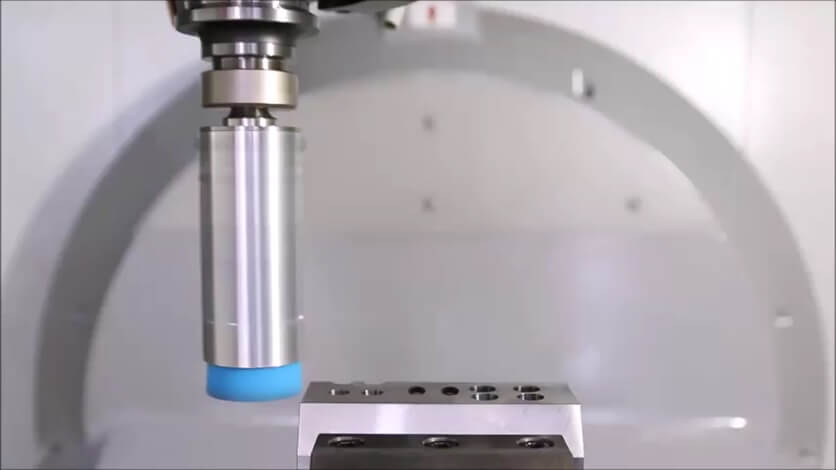
Physical Exertion while Performing the Work
Repetitive Motion: Deburring and finishing require a lot of repetitive motion, often with applied pressure. Repetitive motion and ergonomic injuries are very common with this work, including tendonitis and carpal tunnel. And that can be a significant cost; just one carpal tunnel injury can result in $65,000 in direct and indirect costs, according to OSHA.
Heavy Lifting: When an operator works with large, heavy parts, there’s a risk of strain when lifting the part out of the machine, transferring to a workstation, and turning to deburr and finish on all sides. This strain could lead to pulled muscles and injuries, as well as longer-term ergonomic injuries and musculoskeletal disorders.
Fatigue: The lifting and repetitive motion involved in these processes can cause fatigue. Fatigue tends to come before injury – for many reasons. A fatigued operator is more likely to make errors and that could mean a slip of the hand that causes a cut which hurts the company as well as the employee. Fatigued muscles are more difficult to control and they could seize up or reach a failure point mid-work and could cause longer-term issues for operators.
Holding Uncomfortable Positions: It’s quite common to see workers bending and contorting their bodies to deburr and finish large parts, such as parts for aerospace. Even small parts can be a concern if the workstation isn’t designed for ergonomic comfort, as the worker may have to sit in a curved seated position. For example, a study in the International Journal of Innovations in Engineering and Technology found that certain workstation postures while deburring can lead to strain and musculoskeletal disorders. In another example, an occupational risk assessment in deburring aircraft parts was conducted and is available as a conference paper, as it was presented at the 7th International Ergonomics Conference in 2018.
Close Visual Focus: Burrs are small, and finishing requirements are precise. Often, manually deburring and finishing parts requires close visual focus from the employee. This not only strains their eyes, but it puts their eyes close to dust and debris, a hazard we’ll cover later in this article.
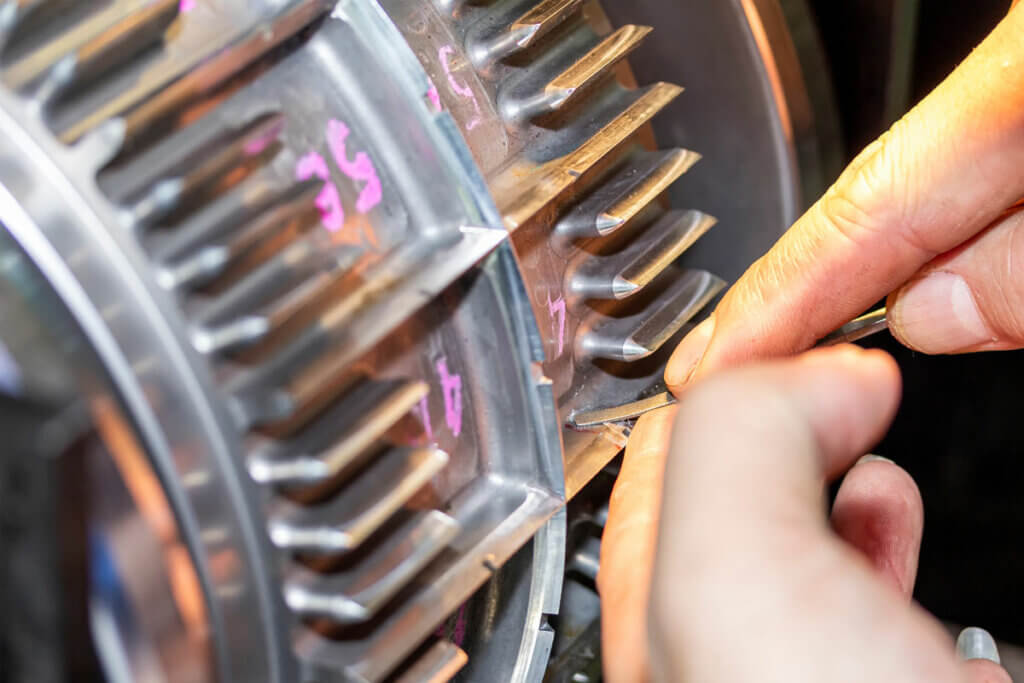
Handling Parts, Tools and Equipment
Cumbersome: Manually working a part typically results in an operator handling a part more frequently. By moving it out of the machine and deburring or finishing at the workstation, the operator is exposed to more opportunities for accidents. Some parts are cumbersome, such as turbine blades. A turbine blade that slips from an operator’s grasp can result in a cut or laceration. And having to handle awkward parts repeatedly could lead to short-term and long-term injuries and disorders.
Sharp Burrs and Edges: Manual deburring means handling parts with sharp burrs, a hazardous task that could lead to cuts and lacerations, or even metal splinters. OSHA estimates that losing a valuable employee for weeks due to a laceration can cost a company $46,000 in direct and indirect costs. If the part itself has sharp edges, handling it puts operators at risk. For example, an OSHA accident summary describes a scenario in which an employee’s thumb was amputated while working a threaded part. With Xebec tools, parts often come off the machine finished and ready to package, reducing handling and its associated risks.
Contact with Abrasives: Deburring tools like grinders and flap wheels involve abrasive materials moving at a high rate of speed, and the worker is often working very close to that abrasive material. It’s not uncommon for employees to experience contact with these abrasives that leads to injuries that can be either irksome or too gruesome to put into words.
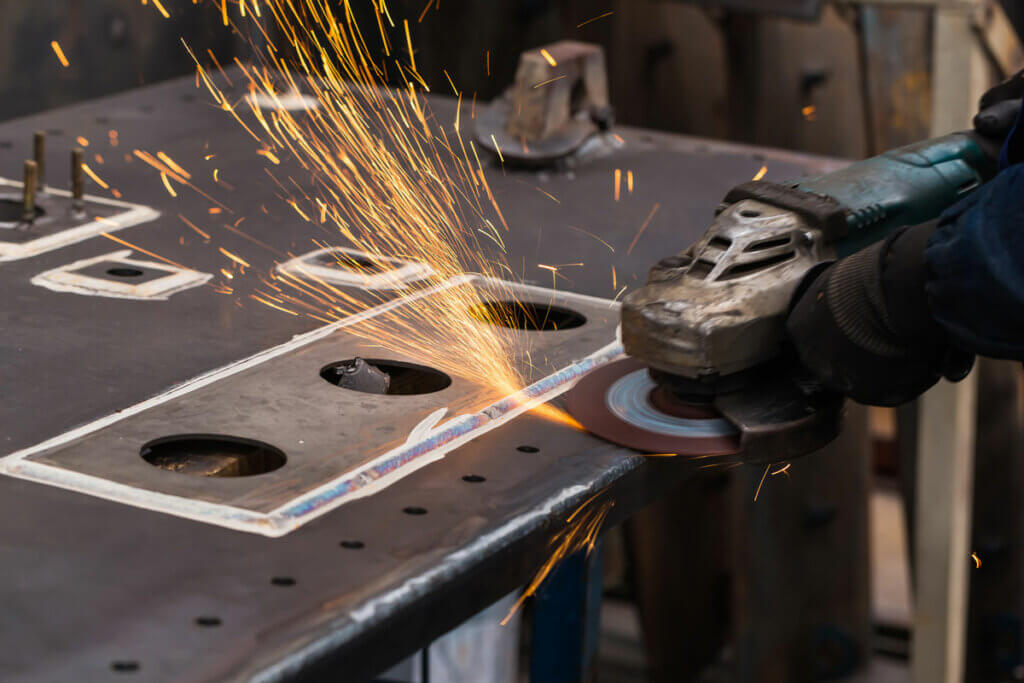
Dust and Debris from Grinding
Deburring and finishing by hand lead to several metal grinding dust hazards, or other material dust hazards depending on the part. Because the work is not contained separate from the worker or the workspace, dust and debris fly off the part and the abrasive material itself. Material debris could cause cuts and lacerations, splinters, and eye injuries. Respiratory concerns from employees breathing the dust in can lead to long-term issues such as chronic obstructive pulmonary disorder (COPD) and chronic bronchitis.
Further, dust and debris can cause hazards around your facility. The dust can pile up or leave a film on the ground, creating slip hazards. Combustible metal dust can cause explosions or fires. And the cords from debris-catching devices, such as a vacuum, can be trip hazards as well. Xebec tools can be used with wet processes, eliminating the hazards of fugitive dust.
Eliminate Manual Deburring Hazards with Xebec
Moving the deburring and finishing processes out of employees’ hands and into an automated, contained process reduces the likelihood of injuries and hazards on your shop floor.
- Operators won’t have to handle and lift parts as frequently.
- The arduous, hazardous work of manual deburring and finishing is eliminated.
- Employees won’t have to work with hazardous manual tools and equipment.
- Burrs will be removed before parts come off the machine.
- Dust and debris will be contained within the CNC machine or robotic cell.
As a result, there will be reduced likelihood of cuts and lacerations, repetitive motion injuries, ergonomic injuries, musculoskeletal disorders, respiratory concerns and more.
No matter what you’re working with, the team at Xebec has seen it all and can help you improve the safety of your workplace and ramp up productivity as well. Learn how our knowledgeable team of application experts can help you plan, design and implement Xebec deburring tools in your processes – and support your use of our tools in the future.
Unable to automate the process at this time? Xebec offers safer hand tools with a rotary tool made to hold them, the Xebec Mobile Micromotor. These light, pencil-like tools can replace heavy, clunky hand tools, and can be gripped in any way. Plus, they don’t have cords or hoses that would otherwise create trip hazards.
If you’ve identified red flags in your processes and want to switch to safer methods, reach out to one of our application experts. The greatest, safest processes come from working with our experts from the start.
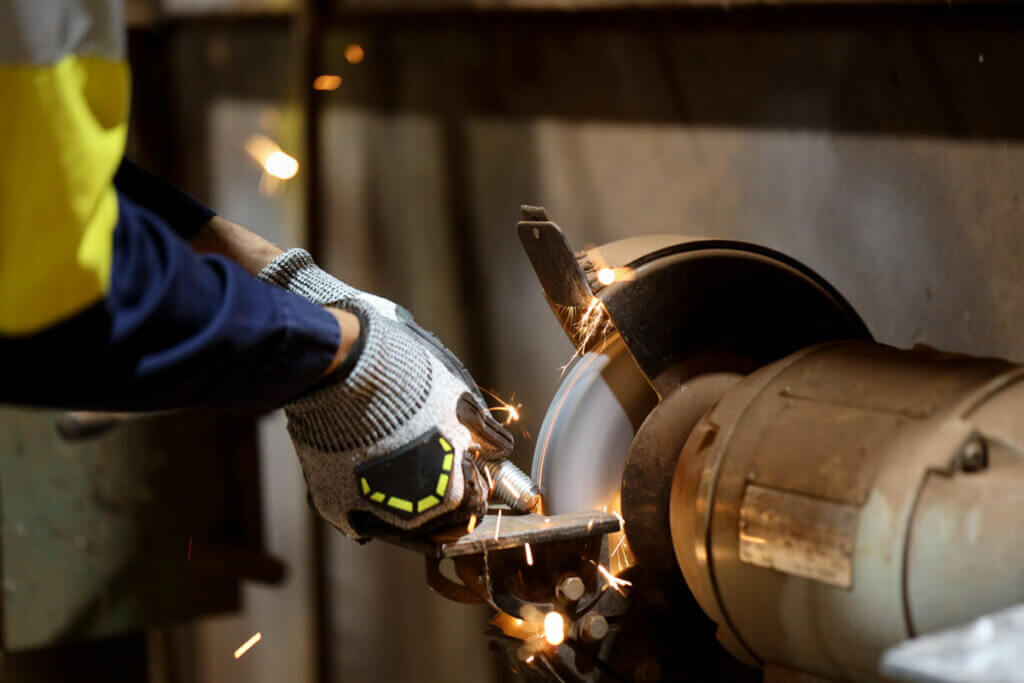