It’s imperative for manufacturers and CNC machining centers to have a close eye on actual spend for jobs, accounting for a variety of direct and indirect factors related to cost. With this, you’ll be working off the most accurate CNC machining cost calculation. You’ll be able to price jobs in a way that retains existing business and allows you to take on new work while remaining profitable.
Take the cost of labor for example. Labor is a major factor in the cost to run a CNC machine and accomplish other tasks related to a job. You must account for all the types of labor needed to produce a part in your job costing calculations.
This includes being mindful of how wage increases at your shop and in your industry affect profitability on your jobs, so you can make strategic adjustments without rattling your customers. This is especially important today, with wages rising in substantial increments each month. According to Reuters, in December 2023, average hourly wages saw a rise of 0.4%, which increased the year-on-year average from 4.0% to 4.1%.
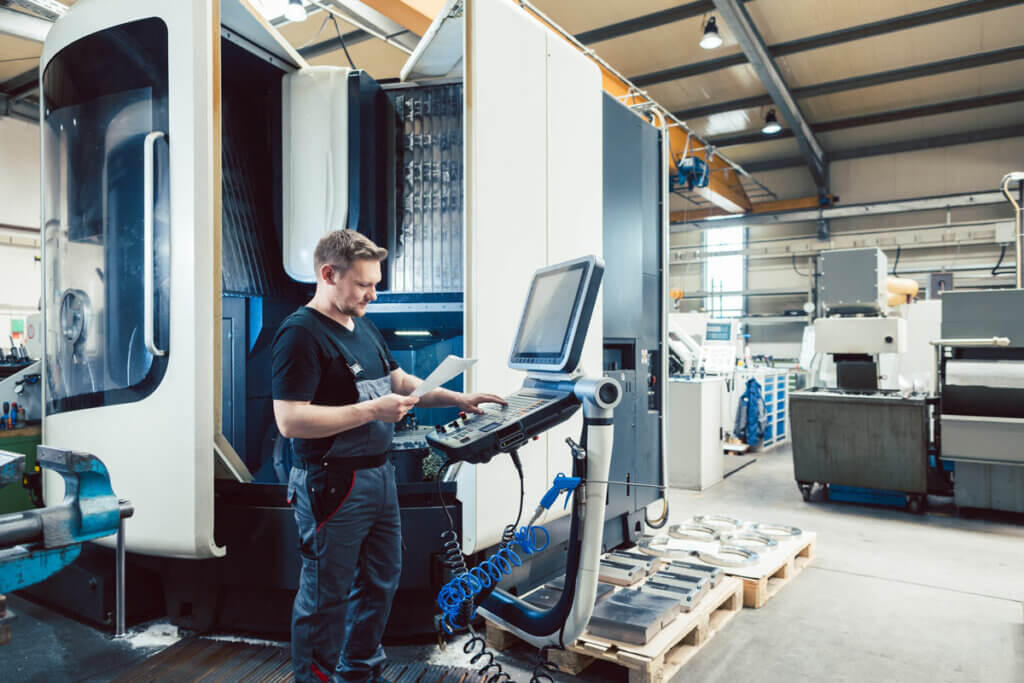
Here, we’ll outline the many direct and indirect components that go into job costing and discuss how you can improve accuracy. We’ll also present scenarios for reducing your current CNC machine running cost and other related costs by increasing efficiency and sophistication in your processes.
For instance, sticking with the labor example, as labor costs increase and the labor shortage persists, it’s critical to optimize how you allocate labor in your shop. If you can automate and combine tedious manual tasks, you can reduce outlay on CNC machining jobs and be more productive with existing employees. Innovative technologies like Xebec ceramic fiber brushes automatically deburr and finish parts in one step, relieving employees of this otherwise manual work and freeing them up to perform other tasks, reskill or upskill to perform higher-value work.
Learn about machine shop use cases for Xebec deburring tools. >>
Monitoring Your CNC Machining Costs Pays Off
With close visibility, you can calculate machining prices more precisely. This allows you to quote jobs profitably and consistently, directly affecting profitability which can often mean the difference between landing jobs and losing them.
In fact, statistics show that top machine shops with more advanced and accurate job costing processes win most of the jobs they quote, where average shops win one job for every two quotes.
Analyzing your production process allows you to create more comprehensive quotes and look at how to streamline production, making it more efficient and cost-effective.
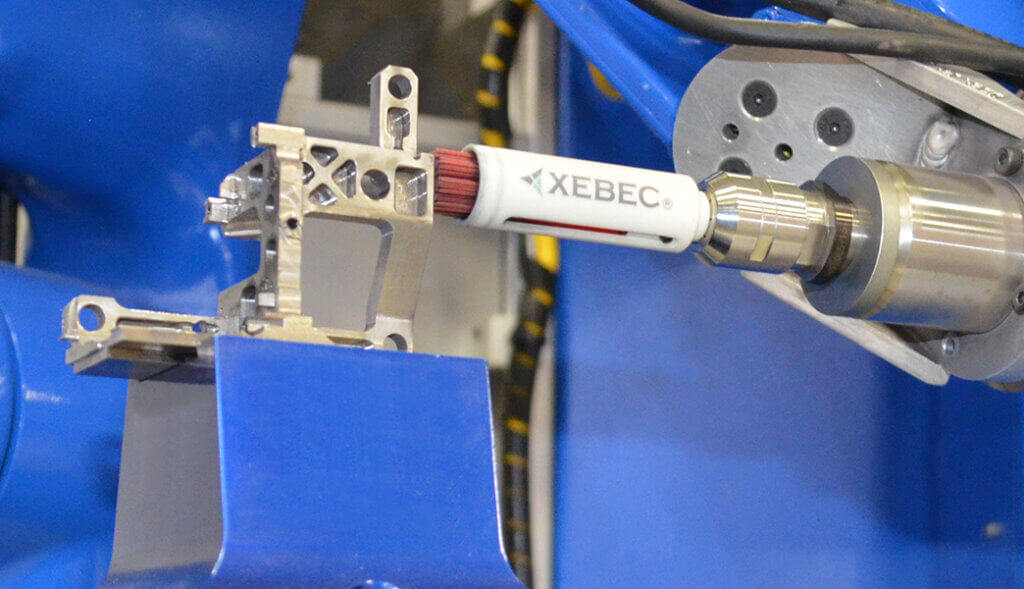
More precise calculations could mean: Better, more informed decisions about mark-ups.
- Improved visibility over wasted spend and time.
- Fewer mysterious, unaccounted-for costs.
- Greater likelihood of margins that provide meaningful profit.
- Improved competitive standing.
- Increased repeat customers.
- Less risk of accepting unprofitable jobs or losing money on jobs.
- Greater business resilience amidst economic uncertainty.

CNC Machining Cost Factors for More Accurate Job Quotes
Many factors influence the cost of a job and how much you should charge. The average machining cost per hour could total as low as $50, as high as $500 – and even more depending on the job.
Complexity of Part
Complexity, such as part dimensions and required tolerances, plays a major role in the cost of a job. More complex parts typically require a higher level of skill, take up more time and resources, and demand specialized setups with specific tooling that monopolize a machine. Depending on your available equipment and processes, working complex parts could also mean using more expensive equipment, tools and supplies. Simpler parts are often easier to work and require less specialized programming and setup.
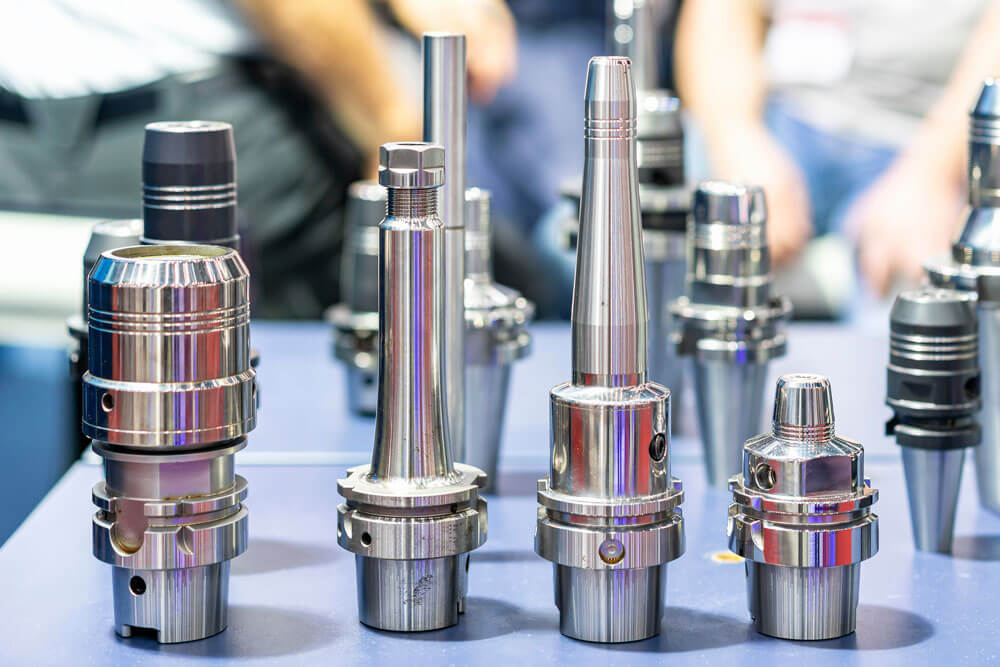
Number of Parts
The number of parts you make in a run directly influences the cost of a job. When you’re able to produce more parts per setup, the value of the time involved in setup increases, and vice versa. You want to determine the optimal lot size for profitability on your machines. Then, for each job you quote, you want to factor for the time vs. value of setting up the run to produce the requested number of parts. Typically, a smaller batch will have a higher cost per part than a large volume run of a similar part.
Material Used
The type of material you’re machining has a major impact on the true cost of a job. Different materials have their own price tags, and those prices fluctuate depending on availability and economic and political conditions. Where aluminum alloys are typically lower-cost metals, titanium matrix composites (TMCs) can cost up to 10 times as much as aluminum alloys. Additionally, a certain amount of material will become waste after cutting. You must consider this lost – but purchased – material in your job costing calculations.
Different materials also have their own machining and tooling requirements. Tungsten, for instance, is an incredibly hard metal. It has an even higher strength-to-weight ratio than steel. Working this material requires a durable, capable tool, such as a ceramic fiber brush from Xebec.
Learn about deburring different materials: Metal, Plastic and Beyond. >>
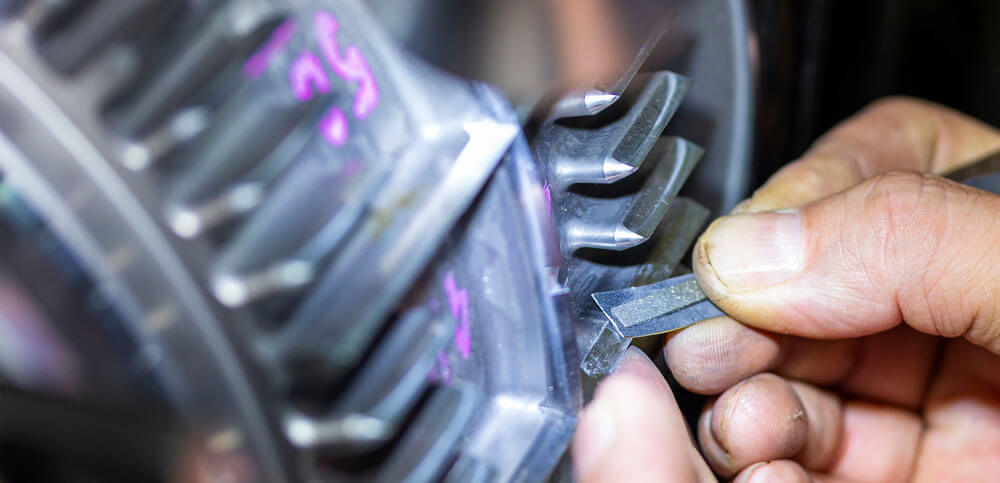
Labor and Labor Overhead
Labor is one of the biggest pieces of the job costing pie. Calculating the true cost of labor per job goes beyond hourly wages and salaries, and it’s not just about the time a part is on the machine. Rather, labor includes costs related to:
- Designing and programming to run the part
- Setting the machine up to run the part
- Running the part and performing changeovers or adjustments
- Handling the part once it’s off the machine
- Performing post-production work such as deburring, finishing, and inspections
The labor category also includes labor overhead, which involves costs related to retaining and supporting your workforce. Examples range from the obvious need to have comfortable conditions in the workplace (i.e., lights on, suitable temperature, ergonomic workstations) to dealing with workplace injuries to providing employee benefits.
Tools and Equipment
The cost of tools and equipment used to produce a part must be included in the overall job cost. It’s easy to neglect this, whether you use an automated brush or a case of disposable discs. It may seem inconsequential in small increments, but the cost adds up at the end of a job.
For instance, if you deburr manually, consider the ultimate cost of a job if you use hundreds or even thousands of $2 to $4 flap discs in the process. If you deburr on the machine using a Xebec deburring brush, one brush can often work tens of thousands of parts, depending on material type and requirements.
Learn about the ROI of automated deburring over manual processes. >>
Machine Time
Machine time is as critical as employee time. CNC machines are hefty investments that can churn out substantial profit, and every hour on them counts. On average, running a CNC machine costs $125 to $250 per hour, but this depends on the machine’s original cost of the CNC machine, the machine type (number of axes) and expected annual production time. Additionally, a run could take minutes or days. That timing depends on the part and requirements.
If tapping is part of your CNC milling process, removing that step from the CNC can significantly reduce cycle time. Adding a rugged, durable tapping arm to the CNC center can improve CNC production time and increase the speed and accuracy of the tapping process. Every minute you can shave off CNC time results in sizable savings.
Note: Machine time may also include changeovers and adjustments noted under labor costs. Be sure to account for this in one or the other category.
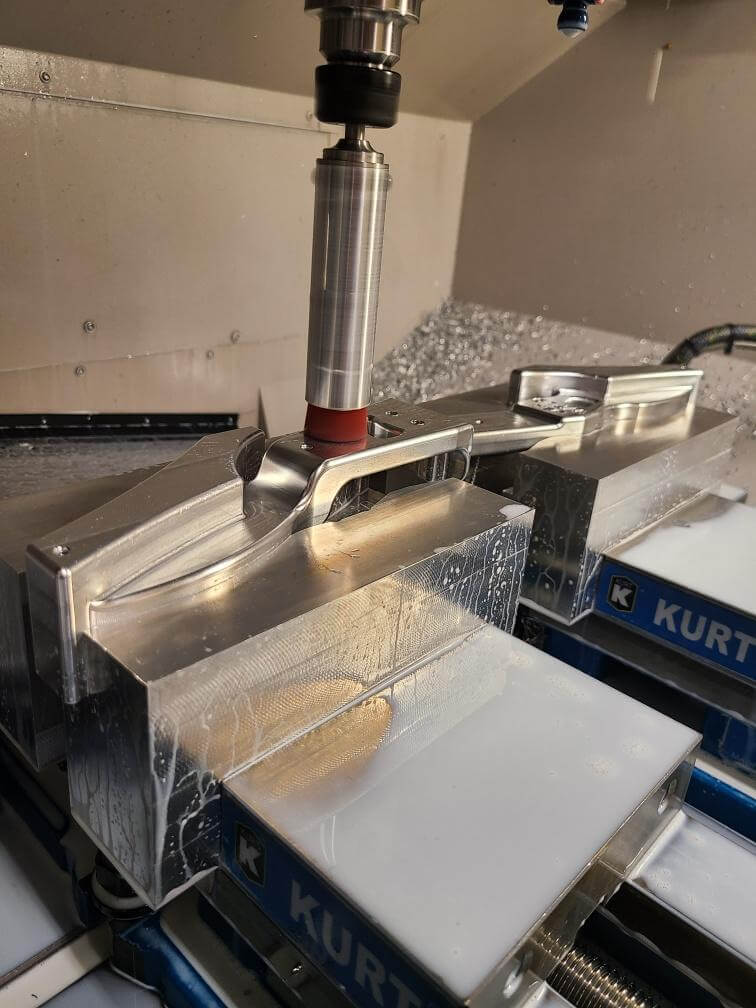
Deburring
Costs related to the actual deburring process depend on the method you use. When deburring manually, the task is separate from the CNC machining process and involves additional labor and tools. When using automated deburring tools on the CNC machine, particularly Xebec deburring tools, the process time is reduced from hours and potentially days to minutes and even seconds.
Further, the tool accomplishes finishing at the same time as it deburrs. You not only reduce or eliminate the time spent performing these tasks, the time is spent handling the part is also decreased. So, while this adds a small amount of time to the machining process, it reduces the time to deburr and finish a part drastically – and thereby reduces net production time per job and increases quality and consistency.
Surface Finishing
Surface finishing costs will also depend on the method used. Finishing work is separate from the CNC machining process when it’s performed manually and takes time and resources. It also requires precision that is difficult to achieve through manual processes. When automating surface finishing on the CNC machine with a tool like Xebec, it cuts time and costs and results in higher quality finishes. Automating also contributes to lower net production time.

QA Inspections
Factor in the cost to perform QA inspections, especially if you deburr and finish manually. Manual processes are less reliable than automated ones, so your QA team has to be extra diligent. With Xebec deburring tools, parts often come off the machine ready to package or assemble, so your QA team will likely need less time to inspect and they’ll send fewer parts back for rework.
Learn about other – avoidable – costs related to manual deburring and finishing. >>
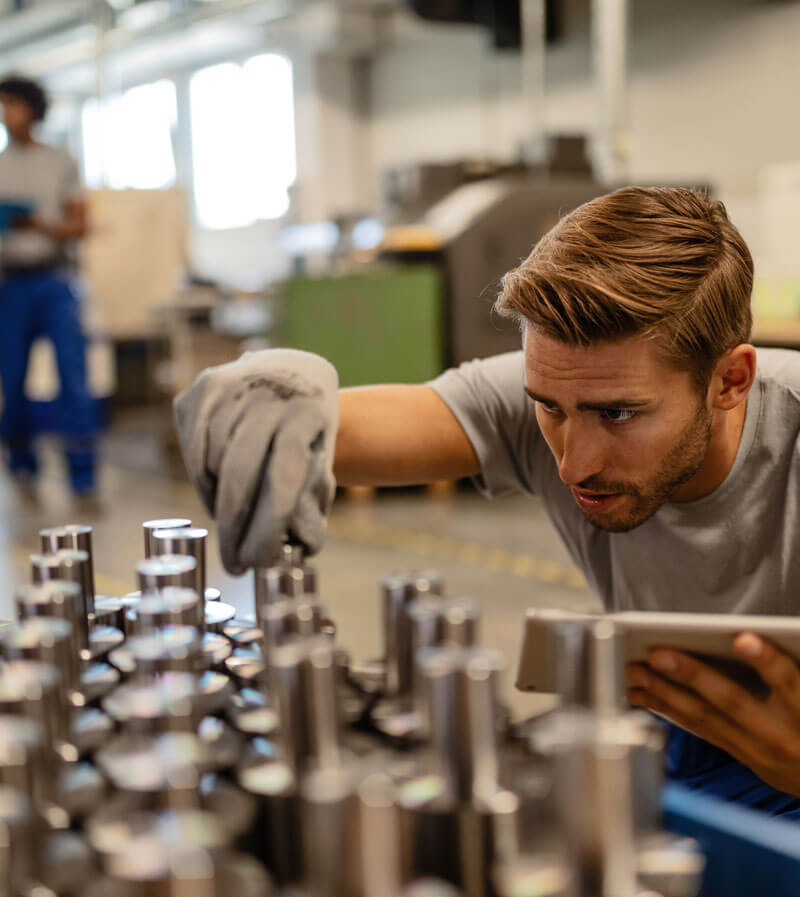
Outsourcing
Most manufacturers and machine shops outsource one or more responsibilities. It may be that you hire a subcontractor to work on site, outsource certain logistics, or outsource entire processes such as deburring and finishing to another shop. Be sure to add expenses related to outsourcing into your job costing process, such as extra handling, transportation and possible parts damage.
Special Handling
If special handling is required, be sure to add related costs. For instance, a customer requests expedited delivery on a job. Your estimator will have to identify opportunities in the current schedule as well as any bottlenecks created, such as obtaining inventory and tooling, and they must be factored in any subcontracted operations. Any overtime to get the job done should be considered as well. Often these jobs consist of one-offs or small quantities, and the estimator should charge enough for expedited delivery.
Transportation
Logistics and transportation have their own costs, such as storage, shipping, fuel and labor. These costs can fluctuate and they’re often outside of your direct control, so it’s important to stay up to date on them as you build out quotes for jobs.
General Overhead
Take into account the costs of necessities at the facility, such as:
- Shop and machine supplies, such as oil, coolant and even printer paper.
- Facility costs, such as rent and electricity.
- Maintenance costs, such as machine maintenance and repairs.
- Necessary insurances and other policies.
Profit
Finally, once you’ve calculated the actual costs that go into a job, you must determine a profitable margin to add onto the job cost. Understanding your true costs helps you make mindful decisions about this margin, so you don’t lose customers to an over-priced job and you don’t lose money on an under-quoted job.

How to Reduce CNC Job Costs through Operational Improvements
Reducing costs in production can help you continue to quote competitive prices, even amid industry challenges such as rising inflation, increasing labor costs and other economic concerns. It can ensure you get the best margin for the work you perform or may create opportunities to pass on savings and strengthen customer relationships. Importantly, many of the measures to reduce job costs will also make your processes more efficient and improve your resource management overall.
Automate Inefficient Processes and Operations
Automating processes in your CNC machining center, such as deburring and finishing, will reduce overhead and labor costs, as well as QA time and scrap. Automating deburring and finishing with Xebec ceramic fiber brushes improves operations and timing as these brushes:
- Perform like cutting tools
- Achieve consistent performance
- Deburr and finish in one step
- Achieve a finely finished surface
- Do not deform after repeated use
- Have incredible grinding power
Learn how Xebec ceramic fiber brushes perform like a cutting tool. >>
Change Part Material (If Possible and Reliable)
If you have influence over part material, changing the type can reduce costs. Certain materials are more expensive and difficult to machine versus others, taking more time, money and effort. Most materials generate burrs during production, whether from milling, drilling, cutting or otherwise. Understanding how different materials behave in the deburring process and which tools will best achieve the precision and quality you need can help you make profitable choices around material type, keeping in mind that parts must be able to reliably perform their end function.
Improve CNC Machine Capabilities
When you assess the entire process, you may find that you need more capability out of your CNC machine. Many machines can be retrofitted so they’re able to work more complex parts, faster. For example, our application experts have experience integrating Xebec ceramic fiber brushes into a variety of CNC machine types.
In some cases, you may want to add a five-axis machine to your facility. The upfront investment of a five-axis machine is hefty, but the functionality you get with it will quickly return the investment.
Optimize Processing Conditions
The tools used and the shape they’re in affects the number and severity of burrs you’ll have to remove. You can save time and money by controlling burr formation in processing. The more finished a piece can be when it’s removed from the CNC, the faster the part can be inspected, packed up and shipped to the customer. When milling, the angle and rotational direction used as well as the depth of cut and feed rate will affect the quality as well. Sometimes, a simple change in the order of operation can significantly improve the quality of the machined piece. Using Xebec’s team and solutions to help you move faster from CNC to shipping.
Optimize Production Processes
Getting visibility into your processes can help you identify the most efficient – and least efficient – activities. For instance, you can identify which lot sizes are optimal for productivity. Consider whether certain levels of custom fixturing are not worth accepting a job. You can use this understanding to inform conversations with potential customers, as you can suggest increasing the job size if it makes the cost more worthwhile.
If you’re tapping parts in the CNC, it’s a good time to consider an investment in a rugged tapping arm, like one from Roscamat’s line of electric and pneumatic arms. By placing a Roscamat tapping arm outside your CNC, your operation can reduce cycle time and gain a significant improvement in speed, accuracy and productivity. While the CNC is milling the next part, the operator can tap the holes in the last part.
Learn how to cut CNC milling time with Roscamat tapping arms. >>
Look at the Big Picture
Consider all the steps involved in a machining job, from CNC programming and loading/changing tools to deburring, finishing, QA and shipping. Calculate how much each step requires and costs in labor and overhead and determine the ROI for the whole job.
Cutting out a significant chunk of manual labor in the deburring and finishing process can save your organization thousands of dollars a year and help deal with the lack of skilled labor. Automating your deburring and finishing process in your CNC provides a positive ROI and impacts your company in many ways by reducing these costs:
- Extra cost of CNC operators having to stop work to deburr parts. Operator labor has a higher cost, especially when engineers are recruited into the deburring efforts.
- Lost production time when not operating the CNC machine, wasting machine value and missing revenue opportunities.
- Cost of returned parts because of unreliable quality due to exhausted, injured or low-skilled employees deburring.
- Cost of purchasing and constantly replacing consumables.
- Cost of injuries and accidents due to fatigue.
- Additional expenses such as transportation costs for outsourced work.
Understanding all the factors involved in the entire machining job will help you develop a good CNC machining cost calculator and improve processes overall. Streamlining the deburring and finishing process with Xebec solutions will not only reduce costs but help you provide consistently high-quality parts and give you the excellent reputation you deserve.
Be Your Company’s Hero: Make the Case for Modern Deburring. >>
Contact us to see how we can help you cut costs and improve the quality and consistency of your CNC machining center.
1 thought on “Job Costing for CNC Machining Centers: Challenges and Opportunities”
Great article! Thank you.