How Xebec Helps Medical Manufacturers Innovate at Pace with the Industry
Manufacturing medical parts, tools, equipment and devices comes with a unique set of challenges that require reliable and dependable partners to meet.
- Medical manufacturing is one of the most innovative product areas, which often means meeting new demands for complexity and function.
- When manufacturers are involved in the research, development and prototyping phases, there are iterations of the product involving unique setups and processes for one-off runs.
- All aspects of the process are heavily regulated and standardized, with high expectations for quality management.
- When producing the final product, manufacturers must achieve highly precise specs to ensure proper functionality and quality for end use.
That’s on top of common challenges all manufacturers and machine shops are facing today, many of which have affected the medical industry in unique ways.
For example, most manufacturers experienced supply shortages. For medical device manufacturing, semiconductor chip shortages were a major barrier to production and innovation. Another example is the labor shortage, which was felt – and is being felt – in most manufacturing sectors. Selecting partners that can help address these issues is key to a medical manufacturer’s success.
Manufacturers across industries face common challenges, as we discuss in our eBook. >>
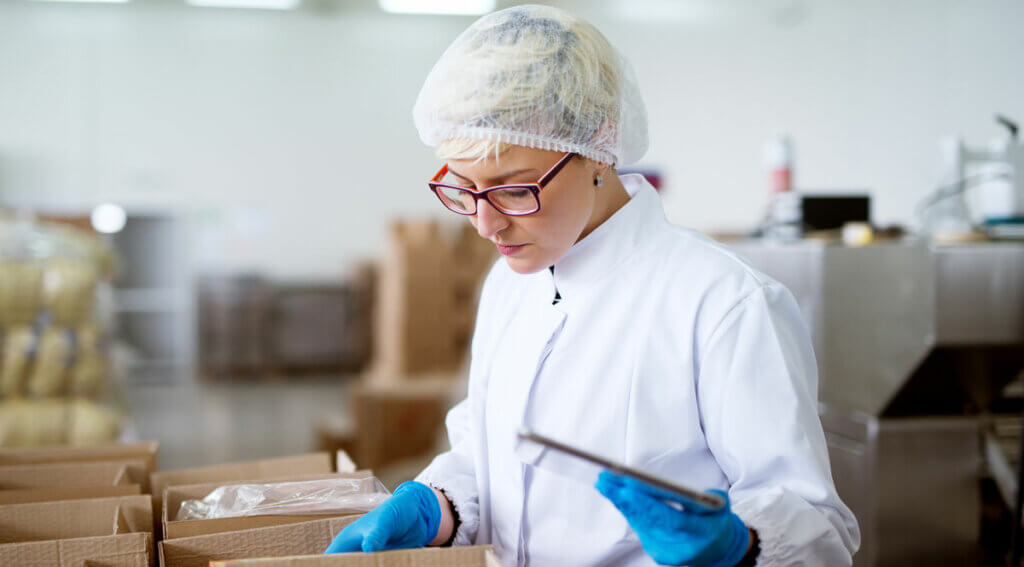
Medical manufacturing is an innovative and exciting sector, resulting in products that save and improve the quality and length of people’s lives.
Deburring and finishing are important steps in the production process. If you’re using insufficient tools or performing these tasks manually, you’re likely dealing with quality-related (and expensive) scrap and significant spend on manual labor. At the end of the day, this can cut into your profit margin and keep you from realizing timely and reliable production at the very least.
Xebec deburring and finishing solutions are as innovative as your medical parts and can help reduce issues that occur during these processes by automating them, performing them both at the same time and producing high-quality, repeatable parts. Production will be faster, more efficient and more reliable. By eliminating manual deburring and finishing, you can reassign and upskill employees from that department to fill skill gaps in your workforce. And you’ll be able to participate heartily in an industry that’s on the forefront of manufacturing innovation and advancing human health.
Learn more about the many applications for Xebec products in medical manufacturing. >>
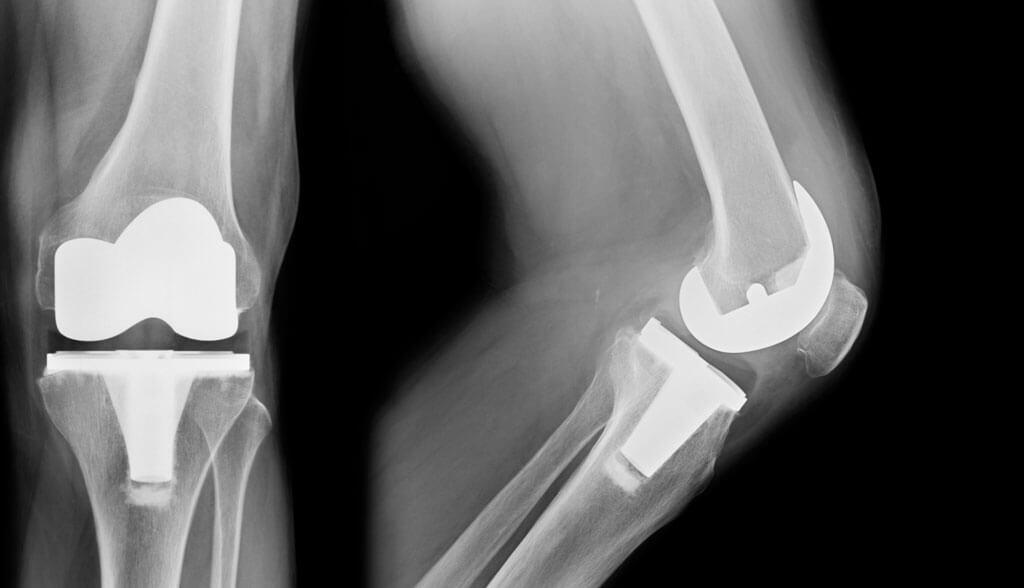
Performance that Meets and Exceeds Expectation
Medical devices, equipment and tools must meet exacting specifications. Otherwise, there could be a catastrophic risk to human life and well-being. Fortunately, the manufacture of such components is tightly regulated and standardized, so a part that isn’t to spec is unlikely to get past quality inspection. Having reliable tools to deburr and finish a part, dependably and reliably, in the final stretch decreases the opportunity for error and waste. And it helps medical manufacturers overcome challenges such as:
- Meeting increased demand
- Producing consistent quality parts
- Meeting tight dimensional tolerances
- Achieving smooth finishes
- Preventing downstream catastrophes or product failures
Learn more: Medical device industry use case for Xebec Deburring Technologies. >>
Critically, Xebec’s modern deburring and finishing tools help manufacturers achieve the desired finish on a part faster and with consistent results. This is essential to performance of the end product. For example, implants are designed to function in specific and dynamic ways, and an abrasive surface could mean poor performance and reduced longevity. And it could greatly affect patient health.
While most parts will require manual polishing to get the exact Ra, such as a mirror finish polished to 1-12 Ra microinches (µin), Xebec ceramic fiber brushes will get you closer to that finish – faster and more reliably – before polishing manually. Xebec brushes can typically achieve 4-40 Ra microinches depending on material and process.

Learn more: Modern surface finishing and polishing operations in manufacturing. >>
Take, for example, the parts involved in a knee replacement. The replacement itself involves a concave cup and convex ball end, parts which fit into each other and must perform dynamic movements in place of a knee. It also often involves a plastic sizing kit. These parts are complex and require precision across production. The finish must be exact to ensure patient safety and quality of life. Otherwise, there is a risk of infection, patient discomfort, reduced part lift, contamination, implant rejection and more.
Learn more: Deburring and finishing critical parts in the medical industry. >>
View a sampling of medical parts that can be deburred with Xebec solutions:
Automation to Innovate with the Industry
The medical industry is on the cutting edge of innovation. When introducing new technologies and processes that help you be innovative and adaptive, you set yourself up to capitalize on opportunities, be invaluable to your customers, and attract and retain skilled employees.

Embracing new and different materials: Research and development is leading to the use of new materials in the medical industry, as well as expanded use of such materials as PEEK plastic. Xebec has a broad selection of ceramic fiber brushes and ceramic stone tools to accommodate materials that need to be worked differently to be efficient and meet specifications.
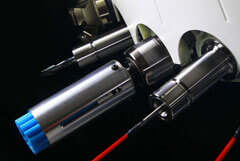
Consolidating processes for modern efficiency: Deburring and finishing are often treated as different steps in the production process, which requires redundant part handling and takes time. Xebec ceramic fiber brushes deburr and finish at the same time, which decreases scrap due to excessive handling and reduces production time and manual labor costs.

Modernizing roles in your workforce: It’s not just the labor shortage putting pressure on manufacturers, it’s also about retention. Giving your employees opportunities to upskill and grow in your company is often even more critical than simple recruitment. With automated deburring and finishing, you can move people off manual deburring to perform higher-value tasks and gain new skills, increasing production.

Implementing robotics where optimal: Robotics are becoming more popular and efficient for medical manufacturing. Xebec tools are compatible with robotics, but how do you determine whether a robot or CNC is best for your deburring and finishing jobs? Your deburring tools should be able to handle changes in your production processes.

Incorporating additive manufacturing: Additive manufacturing is already being put to great use for medical manufacturing, prototyping and innovation. When parts are created with this process, they often benefit from automated deburring and finishing.
ROI Beyond the Monetary to Time Savings and Employee Safety
Automated deburring and finishing are more cost-effective and less time-intensive than manual deburring and finishing when you implement Xebec solutions. You’ll save on the cost of disposable tools, manual labor and waste from quality issues and errors. Considering the expensive nature of materials and parts in medical industry manufacturing, you can imagine how the savings add up.
While Xebec ceramic fiber brushes cost more on an individual level, they last longer and are more efficient than manual and automated alternatives.

Learn more: How to calculate the ROI on automated deburring with Xebec. >>
Further, Xebec tools keep the part on the machine for much of production, reducing or eliminating the need for some time-consuming tool changes and post-machining steps. In most cases, even quality inspection will go faster. So, while keeping the part on the machine for a little longer does add machine cycle time, you have an opportunity to cut total production time by up to 80 percent.

Perhaps most importantly of all, you’ll be doing more to protect your employees and improve their quality of life at work. Manual labor related to deburring and finishing can lead to a variety of injuries, including:
- Cuts and lacerations
- Carpal tunnel
- Splinters
- Eye injuries
Automating these processes in the CNC machine or with a robot not only removes the physical strain, but also the risk of sudden injury from particles in the air or a hand slipping while working a part. Protecting your employees leads to better job satisfaction and increased employee retention, along with a reputation for being a company that cares about its employees. And in today’s market, your reputation goes a long way in attracting high-quality recruits.
Learn more: How automated deburring and finishing improves employee safety. >>
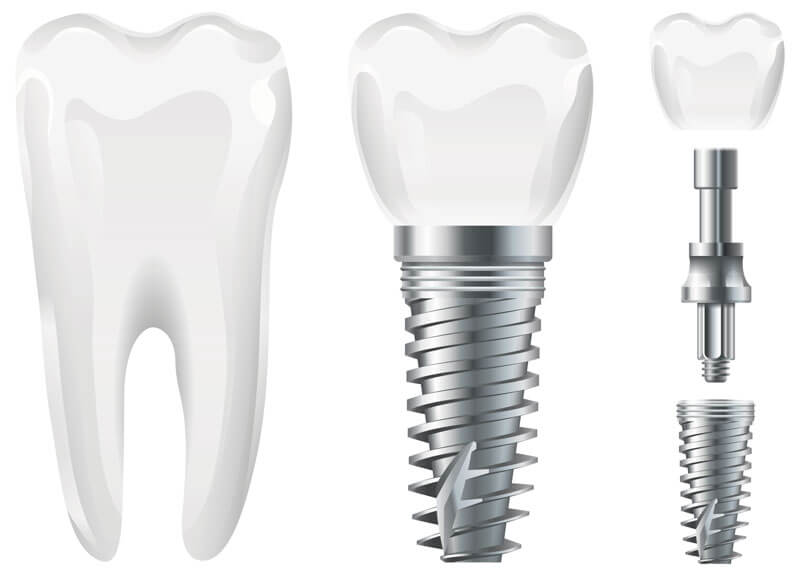
Are you a medical industry manufacturer? Download our comprehensive eBook, Advanced Manufacturing Solutions for Medical Parts.