Imagine the time you’d save if you could deburr and finish your machined parts in one process.
Burrs need to be removed from metal parts and other materials during production. The parts must also be polished to a high-quality, specified finish. This allows the correct fit, assembly and operation of the final product, and it is usually done in separate steps.
To accomplish both steps separately, operators often move parts from one station to another. In some instances, these parts are rather large and difficult to maneuver. In many cases, the part must be flipped several times to work each side and complete both steps. Some shops and manufacturers primarily work small, complex parts, and meticulous attention to detail must be paid in each stage.
Having these processes done separately takes up extra time and much can go wrong during handling. A part or tool could get dropped, or an operator could get injured. If the part is damaged beyond repair, it goes into the scrap pile.
Yet, these processes are critical to ensuring quality production of components used in industries such as aerospace, medical, automotive, fluid power, firearms, electronics, and more. Many manufacturers still perform them separately because there are few systems devised for accomplishing both in one step.
Of the existing applications, only Xebec’s automated deburring tools provide the most flexible, adaptable and economic solution. They’re also the most future-forward option, helping set you up to overcome common manufacturing challenges today, embrace the future of CNC machining and seize transformational opportunities like done-in-one machining.
As you consider the best deburring option for your operations, consider looping our application experts in early. Their experience in the field and across industries has made them invaluable resources for our customers, ensuring each has the most efficient, effective application design for the job.
Deburring Methods Manufacturers Commonly Use
There are many methods of deburring and polishing metals and other materials, each with benefits and drawbacks.
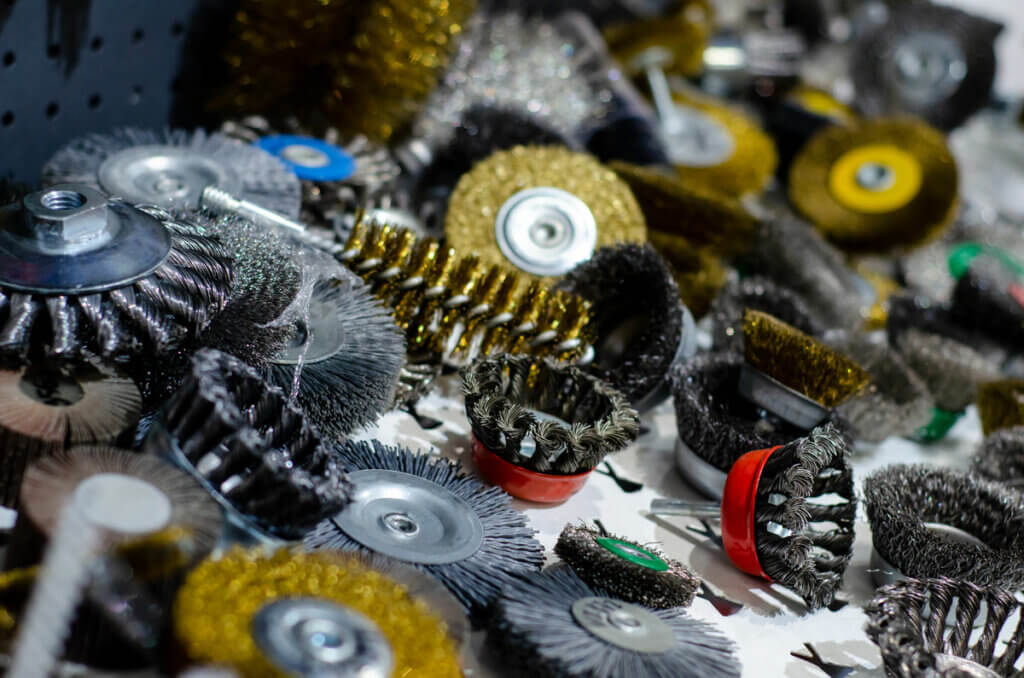
Manual Deburring with Hand-Held Deburring Tools
Hand-held and mechanized tools such as grinders, brushes and files appear to be a low-cost option at first glance. However, when you add up the number of disposable materials and tools you need for hand-deburring each month and compare that to the cost and efficiency of an automated tool from Xebec, you’ll likely find you’re spending thousands more on throw-away tools.
Learn how to calculate the ROI of automated deburring with Xebec. >>>
Beyond upfront costs, there are many quality issues with manual deburring that lead to rework and scrap. For instance, a manual deburring process is not ideal for parts with complex geometries and parts that require tight dimensional tolerances or precise edge breaks. Further, when you use hand-deburring tools, finishing requires a second step.

Mechanical Deburring Machines
Mechanical deburring employs machines to perform general deburring on parts using an abrasive application. This includes wet and dry barrel tumbling and vibratory deburring.
Barrel tumblers work by filling a chamber with abrasive media and other compounds (wet or dry) that deburr and polish the parts during the tumbling process.
Vibratory machines operate in much the same way through a vibration process and come in various configurations such as tubs, circular bowls or trough machines.
Some barrel tumblers and vibratory machines can be economical options due to lower operator costs, and these machines can deburr and polish in one step. However, they have their disadvantages.
Many of these machines have limits as far as the size and type of part you can deburr due to the size of the barrels or containers that hold the abrasives. Also, any compounds and abrasives used in the process could flake off and become embedded in the parts themselves.
With barrel tumbling, there is an increased risk of surface gouges because parts strike one another instead of gently rubbing together.
Wet deburring machines are typically 30 percent more expensive to run than dry machines. They require the use of expensive chemicals to prevent corrosion. These chemicals and the coolants used to run the machine are hazardous waste, so disposal of them is an expensive concern.
Dry media tumbling is a much slower process. Dry abrasives are lighter, so they generally take two times longer to get the same deburring results as wet abrasives. This makes them poorly suited for high-volume production.
Unlike using Xebec brushes in your CNC or robotic processes, tumbling requires a transfer of parts to a separate machine. This adds time and labor to the deburring and finishing process and can result in damage to parts. Plus, it requires cost and labor associated with storage and disposal of tumbling media.
Electrochemical Deburring Process
Electrochemical deburring, or electro-polishing, is a wet process that utilizes the principles of electrolysis. It is commonly described as the reverse of electro-plating. It is primarily used on stainless steel, most commonly for small metal parts with burrs that are otherwise inaccessible by most deburring methods. The method doesn’t involve tool wear, and it can be used to deburr delicate parts with complex geometries.
However, this method cannot remove rough surface defects. It also requires the use of environmentally harmful chemical compounds, and disposing of the wastewater is labor-intensive and costly and subject to strict regulations. Thus, these machines are only cost-effective for small parts and when they make the most sense in terms of part complexity.

Automated Deburring with Xebec Ceramic Fiber Brushes
Xebec’s deburring solutions meet the demand to deburr and finish in one step to save time and resources without sacrificing quality or efficacy. They’re available in a variety of tooling and process options, and they’re capable of working small, complex parts and maintaining tight dimensional tolerances. In fact, the Xebec team works with high-tech industries, such as aerospace, energy and medical, in meeting their precise edge break requirements. Xebec tools and processes can help meet stringent quality demands of industries that cannot risk surface variations that could allow foreign matter to embed on a part’s surface or compromise part assembly or function.
Xebec’s ceramic fiber brushes work like cutting tools and can deburr and polish different types of metals and materials in one process, quickly and efficiently. They can provide different surface finishes by varying cutting speeds and, because of their inherent hardness, are extremely durable when deburring hard metals. Unlike most other deburring methods, they finish at the same time as they deburr. Other brushes can’t achieve the quality and productivity levels of Xebec’s sophisticated cutting tools, and will result in increased labor, scrap and rework over time.
You can use Xebec tools in a variety of methods and applications depending upon your deburring requirements, and they offer flexibility and adaptability to your manufacturing or machine shop environment.
- Hand-held: Xebec provides a number of handheld deburring brushes, pens and stones for detail work.
- CNC Machine: Add a Xebec brush to the end of your CNC machining process and you can create the part, deburr and polish in one step and have your part ready for QA and shipment – all with less overall net production time.
- Robotics: Integrate a Xebec brush with robots for an automated process that speeds up production time while maintaining a superior quality deburring and polishing process.
See this One-Step Deburring and Finishing Process in Action
If you’re an organization that manufactures parts with tight dimensional tolerances or high precision edge breaks and are looking to automate the deburring and finishing processes, check out our video on the automated burr removal and surface finishing of an aluminum alloy air rifle guard using a Yaskawa GP8 industrial robotic arm paired with Xebec ceramic fiber brushes.
This method resulted in incredible cost savings with consistent and improved quality. The video was produced by Xebec Deburring Technologies in collaboration with our partners: Ellison Technologies, Yaskawa and Invictus Manufacturing.
Ready to embrace the future of manufacturing with automated deburring and finishing? To evaluate whether a Xebec ceramic fiber brush is the right tool for you, reach out to discuss your process with one of our experienced, knowledgeable team members.