In the world of clean rooms, where even a single particle can compromise quality, how efficient is your deburring process?
Clean room cleanliness requirements are incredibly high in applications that support manufacturing medical supplies, pharmaceuticals, aerospace and semiconductors.
Many manufacturers turn to robotics to create a sterile environment free of contaminants. Robots can operate in sealed, clean environments with extensive filtration systems to eliminate particulates from degrading quality measures. But what about the tools used for deburring and polishing? How can they integrate effectively with robotics to create a sterile and uncompromised production environment?
Exploring the Use of Robotics in Manufacturing Deburring Process
The deburring process—removing unwanted rough edges, protrusions or imperfections on the material—can leave behind burrs, scales, chips or other particulates. In some instances, these left-over particles are of little concern. However, in processes that require strict adherence to precision, such as medical device manufacturing, semiconductor production or aerospace component manufacturing, less than precise deburring results could be catastrophic.
For this reason, robotic finishing and deburring in separate cells, particularly in clean room environments, are increasingly being implemented across industries that require precision, contamination control and consistent quality.
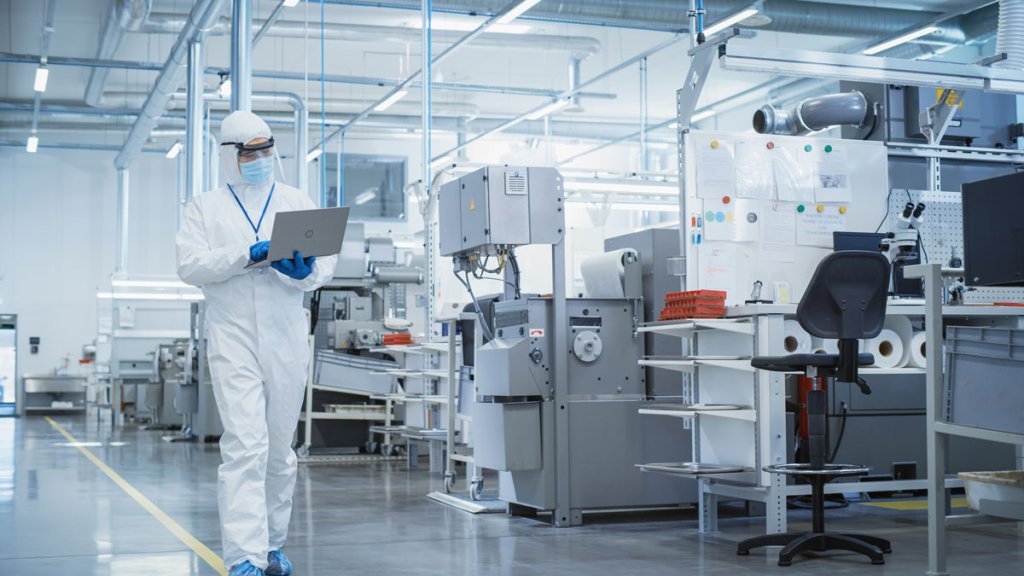
Clean Room Environment Requirements for Manufacturing
A clean room in manufacturing is specially designed to minimize the presence of airborne contaminants such as dust, particulates and microbes in addition to controlling conditions like temperature, light, humidity and air pressure.
Clean rooms are designated with stricter requirements than a controlled environment and are internationally classified by ISO 14644-1 standards. This is because even the smallest amount of contamination in industries like medical device manufacturing, pharmaceuticals, semiconductors and aerospace could compromise the quality of sensitive components.
Clean room requirements may include:
- High efficiency air filtration (HEPA filters)
- Ultra-low particulate filtration (ULPA)
- Specialized clothing for personnel
- All materials must meet rigorous cleanroom standards
- Positive pressure requirements
- Strict quality control processes
- Rigorous washdowns
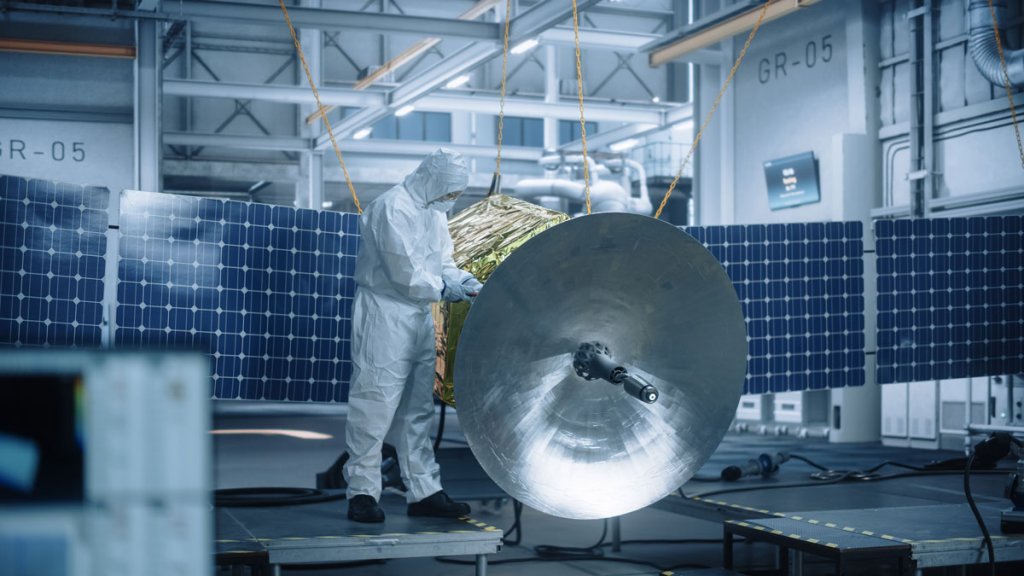
Clean Room Robotic Cells for Finishing and Deburring
Clean room environments are necessary when components require highly controlled conditions to avoid contamination. By automating separate cell robotics in clean rooms, manufacturers reduce manual handling, which minimizes contamination risk and operational errors.
Why robotics in separate cells?
Robotics implemented in separate cells are ideal for complex machining tasks because of their precision, repeatability and ability to operate in isolated, enclosed cells without human intervention—reducing contaminating factors that could affect quality.
Advantages of robotics:
- Prevents contamination
- Minimizes human interaction
- Ensures uniform deburring across multiple parts
- Reduces transfer risks with tool changes
- Can be used in various stages of production (rough deburring, fine finishing and final polishing)
- Can achieve precise tolerances and accuracy
- Can be integrated with vacuum and extraction systems to capture metal shavings or burrs
- Versatility across materials
- Increased efficiency
How Xebec Ceramic Fiber Tools Helps Deburring in Clean Rooms
When precision meets cleanliness, your tools should be as uncompromising as your standards—are your deburring processes keeping up?
Xebec Ceramic Fiber Tools: Xebec’s deburring and finishing tools are ideal for clean environments because they generate minimal debris and produce high-quality finishes without additional cleanup. Xebec ceramic fiber tools are specially designed to optimize the deburring and finishing processes while meeting the stringent cleanliness and precision requirements of advanced manufacturing environments.
Our tools offer several advantages that make them ideal for clean rooms and industries where contamination control and surface integrity are critical. Xebec ceramic fiber tools can tackle numerous clean room applications, including:
Medical Device Manufacturing
Xebec tools are ideal for the precise deburring of orthopedic implants, surgical instruments and dental components. To ensure biocompatibility, they provide clean surface finishing for components made from titanium, stainless steel and other medical-grade alloys.
>> Medical Device Industry Use Case for Xebec® Deburring Technologies
Aerospace Component Manufacturing
Xebec tools are ideal for removing burrs and finishing complex parts like jet engines, turbine blades and structural components in titanium and aluminum alloys. They also ensure smooth and defect-free surfaces to enhance aerodynamic performance and reliability.
>> How Xebec Helps Aerospace Industry Manufacturers Reach New Heights
Semiconductor and Electronics Manufacturing
Xebec tools are ideal for finishing wafer holders, heat sinks and other precision components without introducing contamination. They are capable of achieving ultra-smooth surfaces required for semiconductor applications. Xebec tools are also perfect for deburring connectors, housings and micro-components used in advanced electronics while maintaining strict cleanliness standards
High-Precision Manufacturing
Xebec tools are ideal for deburring components used in the high-tech energy sector, such as solar power and fusion energy systems, while maintaining strict cleanliness standards.
>> How Xebec Tools Spark Productivity and Profitability for Energy Industry Manufacturers
Note: We partner with manufacturers like Fanuc, ABB and Yaskawa, which have developed clean room-certified robots that meet ISO 5 and ISO 7 standards for cleanliness. For more information on the levels of particulates allowed in each standard, please review the International Organization for Standardization (ISO®).
4 Reasons Xebec Ceramic Fiber Tools are Ideal for Clean Environments
Whether you’re integrating Xebec ceramic fiber tools into robotic systems, CNC machines or other automated systems, our tools offer reliable performance, helping you achieve top-quality results in even the most demanding manufacturing environments. Here’s how:
- Minimal Debris Generation
Unlike traditional abrasive tools that can produce significant particulate matter, Xebec tools use cutting-edge ceramic fibers that generate minimal debris during use. The debris that is produced is fine and easily collected by vacuum systems integrated into clean room robotic cells, ensuring a controlled environment free from contamination risks. This feature makes Xebec tools highly suitable for medical device manufacturing, aerospace, semiconductor, and fusion energy component production, where cleanliness is paramount.
- High-Quality Finishes Without Additional Cleanup
Xebec tools are engineered for precision deburring and surface finishing in a single step, eliminating the need for leaving the clean room for secondary operations. The tools maintain consistent performance over time, ensuring a uniform surface finish that meets strict quality standards without introducing contaminants to the workpiece. This capability reduces both production time and labor costs while ensuring compliance with cleanliness requirements.
- Durable and Consistent Abrasive Performance
Made from proprietary ceramic fibers, Xebec tools offer exceptional durability and maintain their shape and cutting edges longer than traditional abrasives. This consistency translates to fewer tool changes, reduced downtime and less manual intervention, all of which make it easier in maintaining a clean environment and efficient process flow.
- Non-Transferable Abrasive Material
Unlike conventional abrasive wheels or belts, Xebec’s ceramic fiber tools do not transfer grit or particles to the workpiece during deburring or finishing. This ensures the surface remains uncontaminated, meeting the strict cleanliness and sterility requirements of industries like medical devices or electronics.
Successful Applications: Xebec Deburring in Clean Rooms
Xebec tools are an integral part of clean room manufacturing. Here’s how clients use Xebec ceramic deburring and finishing tools in a medical device manufacturing setup:
Deburring and Finishing of Hip Implants: Xebec ceramic fiber brushes were used to finish titanium hip implants. The brushes removed burrs and achieved a smooth finish in a single step. The low-debris process ensured a clean working environment suitable for sterile medical components.
Integration with Robots: A robotic arm equipped with Xebec tools deburred multiple parts in an ISO 5 clean room, with integrated vacuum systems capturing any fine particulates generated during the process.
Learn more: No Burr Left Behind: Critical Parts in the Medical Device Industry
Looking for a modern deburring and finishing solution that meets the highest standards for clean room applications?
Xebec ceramic fiber tools are the perfect fit. Designed to generate minimal debris while delivering outstanding surface quality, they’re ideal for industries that demand cleanliness, precision and efficiency.
Contact our experts to design a solution for your clean room processes.