Every CNC operator can tell you that fixturing is an important and complex part of CNC machining.
Manufacturers already use the most optimal CNC workholding methods and fixture designs for their operations given the machines they have, tools they use, part they’re working, number of operations involved and more.
So, when the time comes to introduce a new tool into the process, it’s not always as simple as replacing an existing tool or adding that tool somewhere in the job.
For example, Xebec deburring solutions can replace other automated deburring brushes, but they don’t have the same operating parameters. They perform more like cutting tools. And if you’re moving a manual deburring operation onto the machine to automate it with Xebec tools, that will mean adding a new step to the run.
Trading up to Xebec tools is usually worth the extra effort. They can greatly improve your processes and provide reliable outcomes and many other benefits, including a calculable ROI, time savings and cost reduction.
So, our first tip for optimizing CNC operations is to ensure your machining fixture design will allow Xebec tools to perform at their best.
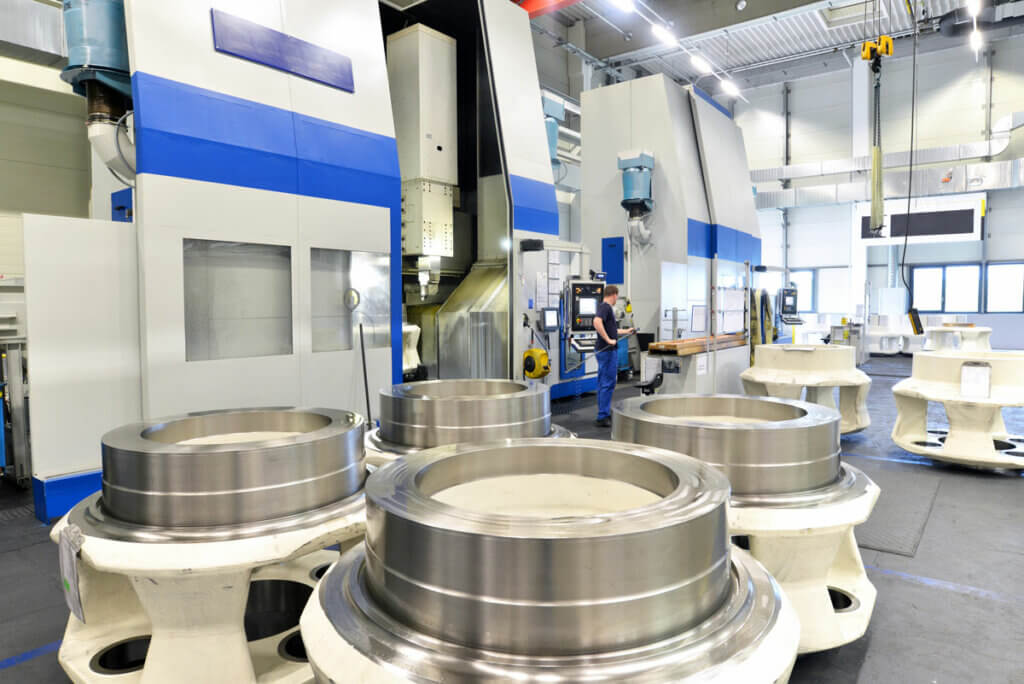
Why Do Workholding Fixture Designs Matter?
Manufacturers often call our seasoned application experts after they’ve already set up fixturing for a part, though it is ideal if we’re able to work with you from step one. In many cases, our team members can identify an optimal way to integrate Xebec tools for the best outcome. Using information such as machine type, fixturing capabilities, number of axes, part complexity and more, they can determine the best way to approach the part and at which step in the process.
Most products require machining on all sides, which could take multiple steps and machine changes. Our experts might determine the tool is best used in the final step and machine to avoid surface damage during the changeovers.
However, there are times our application experts have to problem-solve and get creative to make sure manufacturers get the best results. They commonly encounter issues with:
Part orientation: The part may be positioned in such a way that the tool cannot remove burrs because they’re facing the same direction or the tool cannot come down at a 90-degree angle to the surface.
Burr access: At times, the tool simply can’t get to the burr because of the way the part is positioned and fixtured. For example, the fixtures themselves may be in the way, limiting the faces the tool can touch or which holes can be accessed during the process.
Our experts can help solve these issues by shifting the Xebec tool to later in the process or having different deburring steps happen on different machines. For example, one situation had a pin that prevented operators from getting a tool where it needed to be. The Xebec team determined that access to that area could be found on another phase of the machining and could use a Xebec tool to do the deburring operation in that phase.
We want to work with clients on their specific applications to minimize fixture and machine changes and create a reliable and repeatable finishing process. Some parts may go through twenty operations and three fixturing changes or moved to different machines during the process. That’s why our team members come onsite – to see where our expertise can help work out the right fixturing and operational steps for the best outcome. – Brett Reeder, Xebec Sales Director Eastern Americas
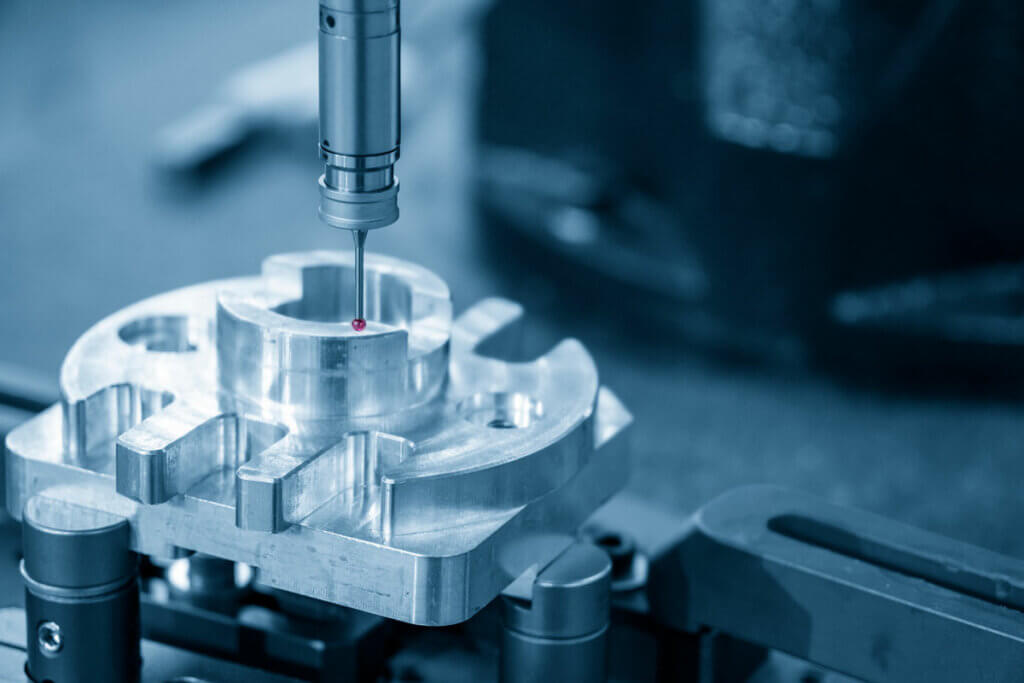
How to Fix Fixturing for Xebec Products
It’s important that your fixturing design supports repeatability and is reliable for Xebec products to get the expected results. The best strategy to get your fixturing set up for implementing automated deburring with Xebec products is to reach out to one of our experts and discuss the design from the start. If that’s not possible, we’re always available to help you strategize to integrate our tools optimally and efficiently.
You might also want to consider upgrading your machinery. Fixturing issues aren’t as much of a concern with 5-axis machines or robotics. These allow the tool to be held and moved in any angle or direction necessary. That way, you can fix the part straight up and down and the robot or 5-axis can turn in ways that allow you to touch every side of the part without having to take the part off and place it into another fixture or machine. In a 5-axis, for example, the table can move and the spindle can move to it. You can present the part in different ways.
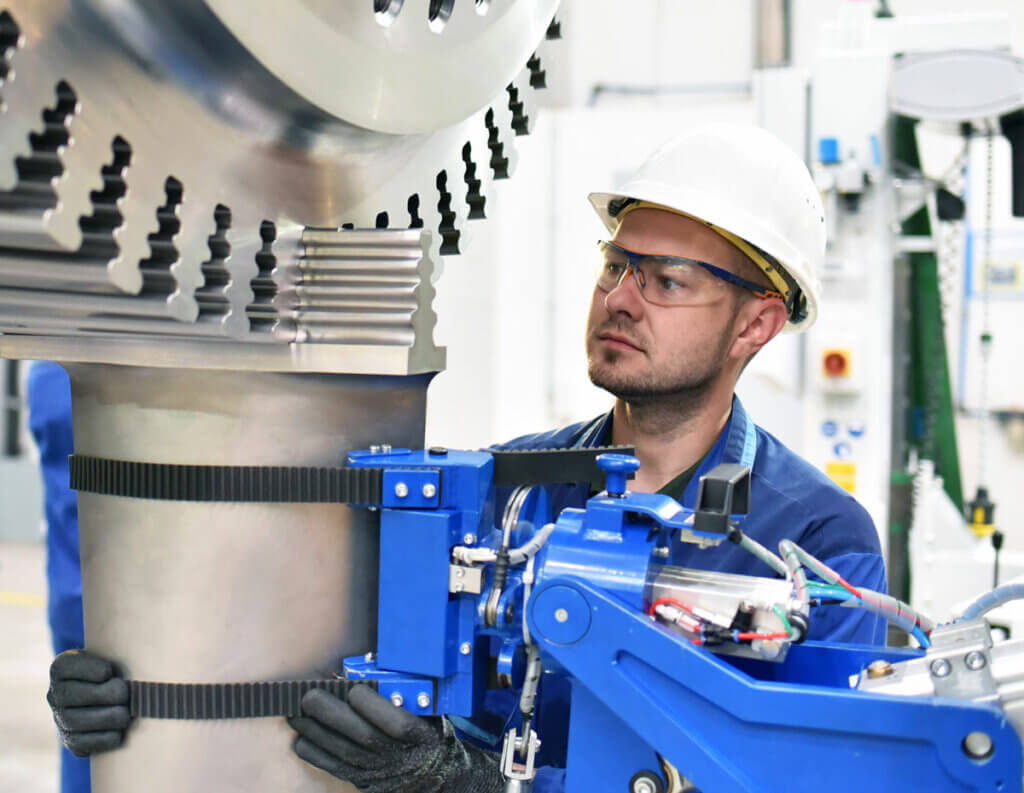
And if you’re using manual methods to deburr and finish, reach out to discuss automating these processes with our tools. Automating deburring and finishing in the machine means less movement from one fixture setting to another. This is critically important for parts that are required to meet surface roughness specifications in industries such as medical, aerospace, energy and more. The fewer times you touch the part, the less likely it will be scratched and damaged moving from machine to machine or for burrs to be left behind. And a superior finish that reliably meets strict specifications is critical to your customer’s satisfaction and you company’s reputation.
Meet our experts at Xebec and contact us to help you design the optimal fixturing and process to get the results your customers require.