The CNC industry is set to thrive over the coming years, as CNC machines play a major role in helping manufacturers embrace modern processes and increase efficiency and profits. The industry can anticipate a growth rate of five percent from 2022 to 2030 and a value of USD 126 billion by 2030 (Market Research Future).
At Xebec, modern CNC machining is our world. Our tools automate deburring and finishing on CNC machines and help manufacturers delve into the “future” of manufacturing – and we’ve been quite busy. So, we can confirm: We’re seeing this growth on the ground when we visit manufacturers of all sizes across the country.
But what’s driving it?
Data from Market Research Future and Precedence Research attributes this anticipated growth to:
- Increased demand for:
- Medical devices
- Electric vehicles (EV)
- Telecom communication equipment
- Semi-conductor manufacturing equipment
- Increased demand for automated CNC machines in:
- Healthcare
- Aerospace
- Defense industries.
- Increased adoption of and demand for Internet of Things (IoT) technology.
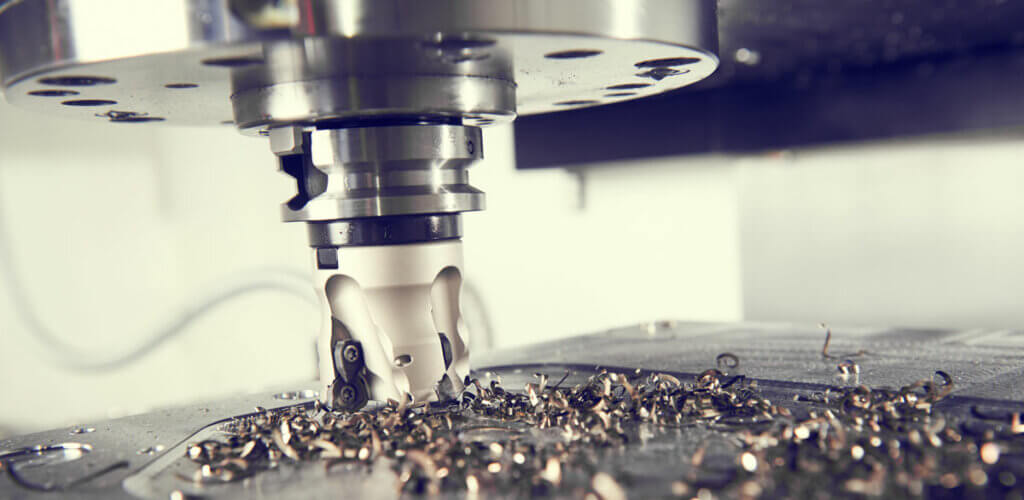
The data also shows the inherent advantages of CNC machining are driving growth, as they’re attractive amid labor shortages and demand to produce more, faster and to high quality standards. Those inherent benefits include:
- Helping businesses transition toward more automated processes with the rest of the industry.
- Allowing businesses to maintain and improve productivity despite staff shortages.
- Ability to pair with industrial robots to achieve greater efficiencies, flexibility and productivity.
- Allowing businesses to reduce costs in several areas of their operations.
- Improving safety on the shop floor, protecting staff and reducing safety-related costs and downtime.
However, with so much opportunity on the table, the industry is still plagued with challenges. The labor shortage is a top concern for every industry leader we meet. And Precedence Research cites “inadequate skills” as a key challenge. As much as companies want to capture the opportunities with CNC machining, many do not have the right balance of qualified employees to operate them.
Additionally, customer expectations are pushing manufacturers toward “high-mix, low-volume production,” challenging manufacturers to improve and diversify how they serve customers and optimize pricing, timing and quality – all while remaining profitable.
Further, manufacturers are being asked to work with new and emerging materials as industries innovate for strength, performance, sustainability and more. Their existing tools and processes may need adjustments to properly work these materials.
We recently covered the future of CNC machining technology itself, and which innovations are the real future for these machines. Here, we’ll stay up to date on the latest trends for CNC machining in general – beyond just the machines.
Our application experts are seeing much of this first-hand on their visits to your shop floors. They know what’s really happening in the industry, and what’s just hype. If you’re thinking of implementing Xebec tools in your process, be sure to reach out to our experts first. Their industry insight and familiarity with our tools will help you make the best decisions for your operations.
Where We’re Going in the Future of CNC Machining
1. We’ll innovate and upgrade our machines.
As we pointed out up top, manufacturers and job shops will purchase more CNC machines at a substantial growth rate in the coming years. Where possible, manufacturers will retrofit existing machines to better meet today’s demands and improve overall production time and part quality.
For their purchases, manufacturers will favor 5-axis CNCs, as these will allow them to work more complex parts, faster and more efficiently.
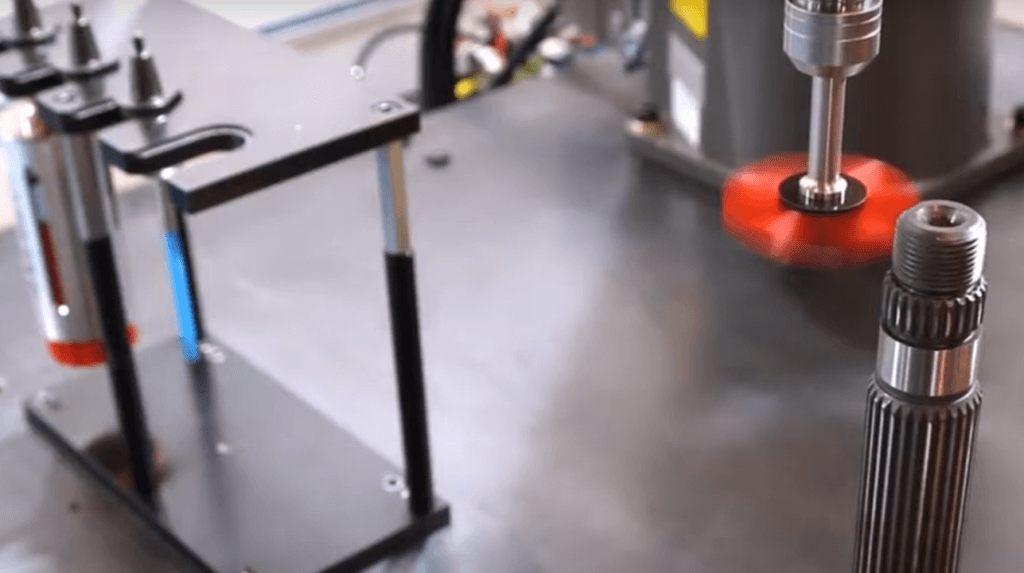
The most forward-thinking manufacturers will do this with an eye toward creating “done-in-one” production processes, where the entire production process happens on the machine and the part comes out ready to package. This is a major step toward lights-out manufacturing, a much-desired capability in the industry.
Manufacturers are also considering how they can incorporate additive manufacturing, or 3D printing, into their machining processes. Manufacturers are experimenting – and finding success – with pairing CNC machines and 3D printers in their processes.
Xebec tools fit whether you’re retrofitting or upgrading to a 5-axis machine to automate deburring and finishing. In each case, Xebec tools improve the speed, cost and efficiency of deburring and finishing operations. If you can only make one investment at a time as you retrofit a machine, an automated deburring brush made of continuous ceramic fiber will make a major difference.
What makes Xebec tools top-priority investments for CNC machining?
2. We’ll embrace more automation.
Industrial companies are set to invest substantially in automation over the next several years: 25 percent of their capital spend, according to the 2022 McKinsey Global Industrial Robotics Survey. McKinsey projects that these investments will improve safety, quality, speed of production delivery, production capacity and more (see chart below).

Further, Bain & Company reports that companies that strongly invest in automation across operations – not just on the shop floor – reduce costs by more than twice the amount of those who invest at a lagging pace. Apart from saving on costs, automating also allows these companies to free up employee time, which they can then allocate to higher-value work, and speed up overall process time.
Automated deburring is rapidly becoming a “no-brainer” in the industry as manufacturers evaluate tasks to optimize. Manual deburring and finishing are time-consuming, arduous tasks that won’t make it far into the future of manufacturing – especially as the labor shortage continues and this undesirable work deters prospective hires and frustrates existing employees.
Why won’t manual deburring make it into the future of manufacturing?

3. We’ll have more robots helping around the shop.
Manufacturers will find more opportunities to incorporate robotics into their processes, especially where they enable automation and fill gaps left unfilled by the labor shortage. In CNC machining, robotics can move parts in and out of the machine and transfer them to workstations. Robotic arms can also be programmed to deburr and finish parts after they’re off the machine if these tasks aren’t automated in the CNC. Robots are precise and efficient, which are desired benefits in all manufacturing operations.
Which is better for deburring and finishing: CNC or robot?
4. We’ll modernize employee roles and responsibilities.
Upgrading and automating manufacturing processes and operations will require manufacturers to evolve employee roles and responsibilities – which is good business practice for employee retention and recruiting in any environment. Employees need to know they have career paths at your company, and those paths should reflect the future landscape of the industry.
What does that landscape look like? According to McKinsey, the need for hands-on labor is expected to decline by 30 percent in the coming decade and technical skills will see a 50 percent increase in demand. Manufacturers are readying for this, upskilling and reskilling employees so they can grow and perform higher-value tasks. This improves employee job satisfaction and relieves concerns around the labor shortage, especially if you automate once-manual tasks such as deburring and finishing.
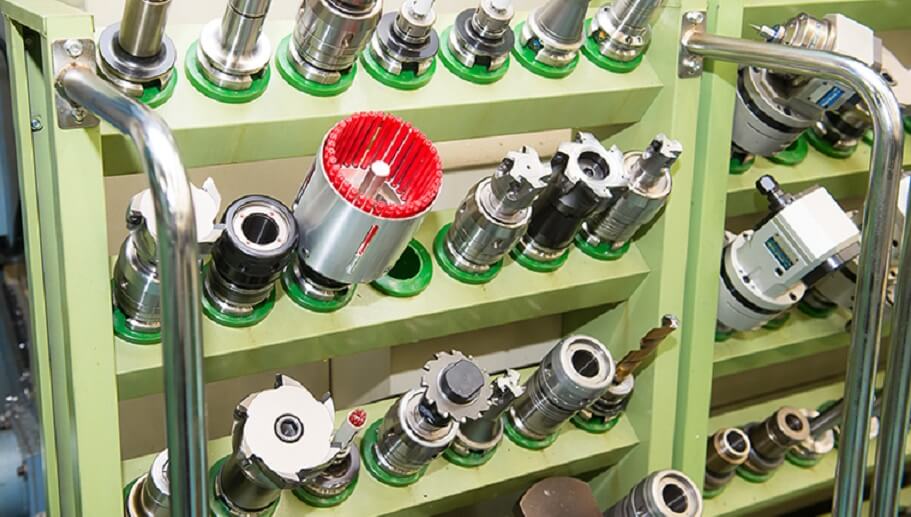
5. We’ll operate more sustainably.
Sustainable manufacturing is no longer a distant goal to work toward inch by inch. The manufacturing industry is responsible for a fifth of the energy consumption in the United States, and industry leaders are being called to incorporate more sustainable practices and meet new standards.
Fortunately, operating more sustainably also benefits businesses. It allows them to identify costly inefficiencies in their operations and make smart investments that often reduce overall costs and optimize processes.
One simple swap that can edge you toward greater sustainability is automating deburring and finishing. You might be surprised by the impact such a small change can have on your business – in fact, we identified nine.
How does automated deburring help with sustainability goals?

Due to the innovations we’ll make in our own CNC machining and operations, we’ll be able to realize better quality and consistency than ever before, optimize production time and increase throughput. This will raise the bar across the industry – which is an incentive for any manufacturers that are still lagging to start making strategic improvements and investments.
Investing in automated deburring and finishing is one way to reap results like these, quickly and efficiently. Xebec deburring tools increase machine time by a fraction yet result in major time and cost savings, shrinking net production time. And they produce consistent, quality results every time, reducing the time spent on Quality Assurance.
If you’d like to discuss your hopes for the future of your CNC machining operations, reach out to start the conversation.
Download our comprehensive eBook: Solving Modern Manufacturing Challenges