Are you creating more problems by using the wrong tools for deburring?
Machinists know that deburring and surface finishing are critical in high-precision machining, but not all tools deliver the same results. You may be relying on traditional nylon brushes for deburring, assuming all tools work the same.
However, nylon impregnated brushes (also known as abrasive nylon brushes) fall short when precision, consistency, and material adaptability are required.
A comparison of nylon impregnated brushes against Xebec ceramic fiber brushes demonstrates why Xebec cutting tools are the superior choice. This is especially true for machine shops and high-production, tight-tolerance industries that deal with challenging materials like advanced alloys and materials with extreme hardness levels used in aerospace, medical, energy, firearms and other high tech applications.
>> Xebec Ceramic Fiber Brush: The Deburring Brush that Performs Like a Cutting Tool
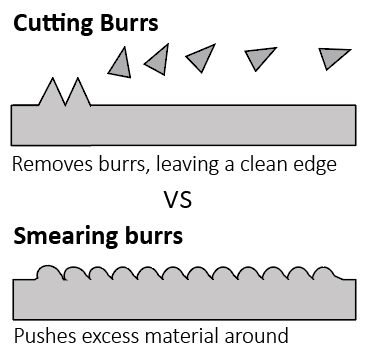
Key Differences Between Xebec and Nylon Brushes in Deburring
Avoiding burrs before they become a problem avoids issues further down the production line. But to avoid cutting and pushing burrs, you need the right cutting tools that maintain a sharp cutting surface, using the correct speed and feed rates. Let’s talk about the difference between cutting and pushing burrs:
Cutting burrs: created when the material is sheared away during the cutting process, leaving behind small, raised edges. This commonly occurs during milling, drilling and turning.
Pushing burrs: created when the material is not cleanly cut but instead displaced or pushed to the side. This commonly occurs during stamping, punching or forming and can be a result of blunt tools, excessive force or soft material.
Your tool selection plays a big role in material removal.
Why Nylon Brushes Fall Short in High-Precision Machining
Nylon Abrasive brushes offer limited performance and potential for inconsistencies.
- Nylon impregnated brushes are composed of nylon filament typically coated with silicon carbide grit particles, which can wear down quickly and unpredictably.
- To deburr extremely hard materials, diamond grit is used on the filaments, which is typically more expensive.
- These brushes push burrs instead of cutting them, which can lead to smearing and inconsistent finishes.
- Applied pressure must increase over time as the abrasive layer wears off, creating variability in deburring results and inconsistent finishes.
- When used on cross-drilled holes, nylon brushes can push burrs back into the hole, requiring additional manual processing.
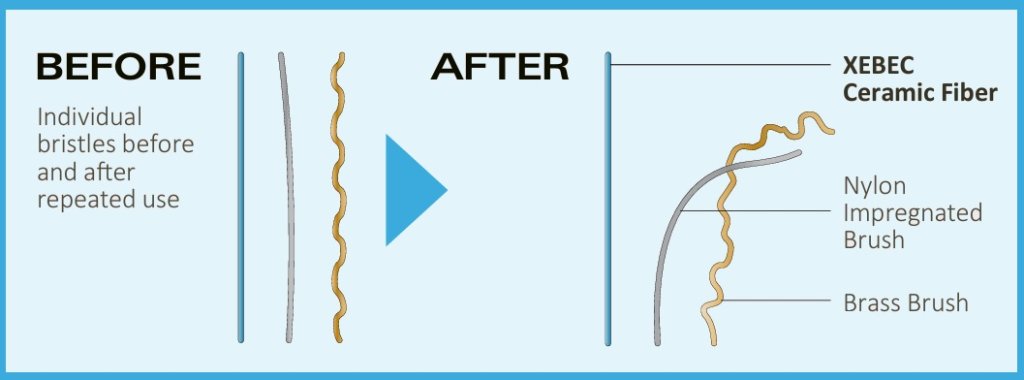
How Xebec Ceramic Brushes Reduce Costs and Boost Efficiency
Xebec Ceramic Fiber Brushes offer precision cutting for consistent results due to the following:
- They are made of continuous ceramic fibers that maintain sharp edges as they wear.
- They cut burrs cleanly at the root, preventing material smearing and ensuring a uniform surface finish.
- Speeds, Feeds and Depth of Cut matter to XEBEC.
- Cutting depth is prescribed rather than pressure-dependent, allowing repeatable results and automation in high-production environments.
- Xebec brushes make cross-hole deburring much easier with consistent and reliable results.
- The ability to maintain sharpness throughout its lifespan means fewer tool changes, increased uptime, and improved efficiency.
- Xebec often runs at 2-4 times the Feed Rate of a nylon brush.
The True Cost of Nylon Brushes: Hidden Expenses & Performance Issues
Nylon brushes are usually selected because they are cost-effective up front and can often handle harder metals than wire brushes. They can also be used to achieve certain edge radii and finished surfaces. However, their performance is inconsistent, takes longer than that of ceramic fiber, and may leave a surface residue. Other downsides include:
- Has a lower melting point
- Can generate static charge
- Limited rigidity for extremely hard alloys
- Not biodegradable or environmentally sustainable
- Poor resistance to chemicals like acids or solvents
- Bristles deform and fray with continuous use
- Dust particles require dust collection systems and PPE for staff
Additionally, using nylon brushes can yield unexpected expenses:
- Inconsistent Performance: Abrasive distribution varies, making it difficult to achieve uniform deburring results.
- Shorter Tool Life: Once the abrasive layer wears down, performance declines rapidly, leading to frequent replacements.
- Increased Manual Labor: Nylon brushes often require additional post-processing steps, increasing labor costs and cycle time.
- Process Inefficiencies: Deformity of nylon brushes is often a cause for rejected parts.
- Limited Use: Nylon impregnated brushes are inefficient for use in clean room environments.
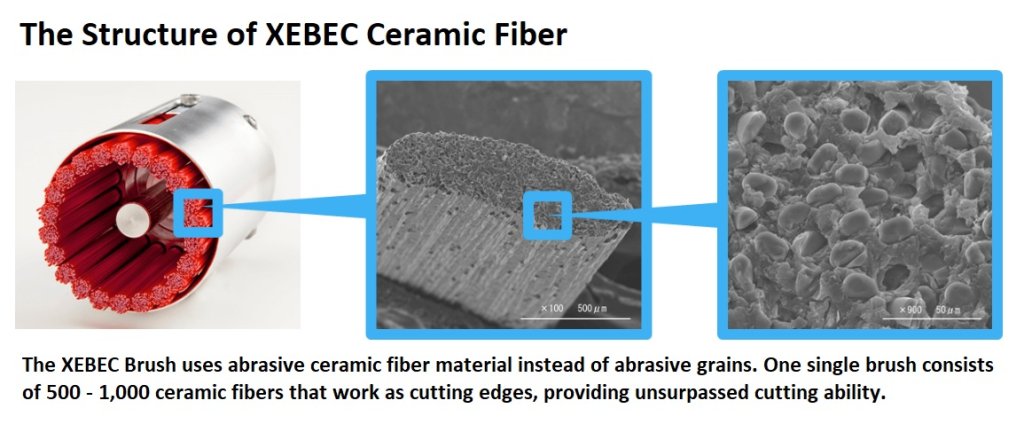
Xebec Cutting Tools Reduce Costs and Increase Efficiency
Xebec ceramic brushes are made with continuous ceramic fibers that have 60 times the grinding power of nylon brushes. The uniquely developed ceramic fibers themselves are the abrasives and the fiber content ratio is over 80%. One single bristle in a Xebec brush consists of 500 -1,000 ceramic fibers that work as cutting edges, providing excellent performance.
Though they may come at a higher upfront cost, they don’t deform over time like nylon fibers and wire brushes do. Longer service life, improved consistency and greater efficiency means manufacturers save net production time.
- Longer tool life means fewer replacements and lower costs.
- Cutting efficiency results in better results, reduced manual intervention and higher automation potential.
- Greater consistency ensures quality control is maintained without the need for extra rework or inspections.
- Handles harder metals better than nylon fibers.
- Unparalleled automated cross hole deburring performance
- No mystery abrasives.
- Xebec generates minimal particles or debris which make it CNC, Lathe, and Robot safe.
>> XEBEC Solutions for Greater Efficiency and Reliability: Automated Cross Hole Deburring
Precision Applications: Controlling Lay Patterns and Surface Finish
How do Xebec’s proprietary ceramic fibers perform in special applications?
High-precision CNC machining requires repeatable surface finishes and often lay patterns, particularly in aerospace, medical, and automotive applications. Something that nylon brushes can’t promise.
Xebec ceramic fiber brushes allow manufacturers to create consistent lay patterns that enhance surface finish and sealing surfaces. The ability to apply specific and repeatable lay patterns is critical as they are used to enhance the seal of metal parts.
Xebec brushes use abrasive ceramic fiber bristles that effectively remove cutting and pushing burrs without damaging the workpiece. Unlike nylon brushes, ceramic brushes cut rather than smear material—leaving cleaner, more consistent edges from the start.
When working with tight tolerances, Xebec’s precision cutting minimizes the risk of over-processing or unintended material removal, which is crucial for high-performance components that are required to meet strict Surface Roughness (Ra) and finish specifications.
Unlike nylon brushes that degrade over time and lead to varying results, Xebec brushes ensure each part meets the same exacting standards, reducing variability and quality control issues.
>> Learn how Xebec meets surface finish specs for aerospace industries and more
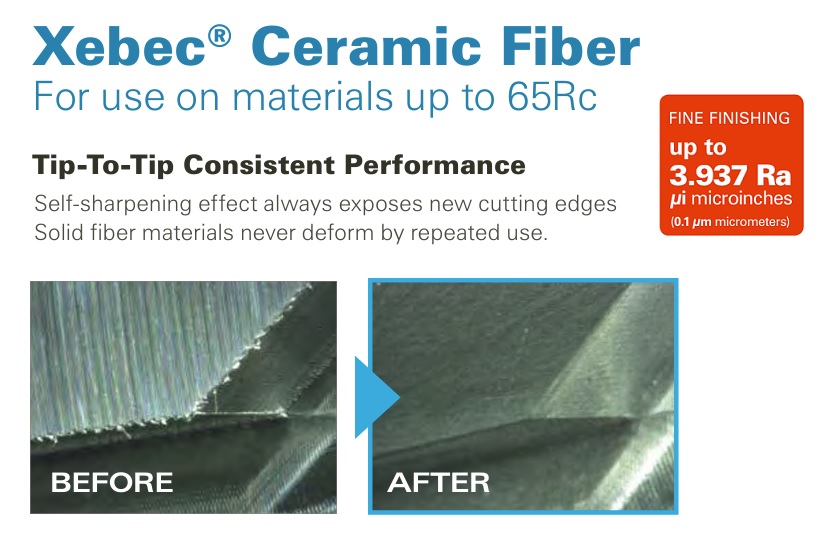
Tackling Tough Materials: Xebec’s Advantage in Hard Alloy Deburring
Exotic metals and varying levels of material hardness have become common challenges for metal cutting applications. As manufacturers and machine shops run into materials made with a high nickel content, such as Inconel and stainless steel, they find using more advanced cutting tools is a non-negotiable.
Deburring Nickel-Based and Proprietary Alloys: The Challenges
Many industries, particularly aerospace and defense, use proprietary alloy mixtures with high nickel content for strength and durability. These materials often have inconsistent machining characteristics due to small variations in composition (1-2% difference in nickel can significantly impact cutting behavior).
Traditional nylon brushes struggle with these alloys, leading to burred edges, excessive wear and ineffective deburring, but Xebec brushes are up to the task.
Xebec Tools’ Advantage in Hard and Unique Materials
Xebec tools effectively handle materials up to 65 Rockwell hardness, a range where nylon brushes quickly lose efficiency.
Capable of working with exotic materials such as Inconel, Hastelloy, titanium, carbon fiber composites, and even quartz, Xebec offers solutions for industries requiring precision deburring in hard-to-machine materials.
As the use of new alloy mixtures grows in aerospace, medical, and defense industries, Xebec’s tools, with the expert consulting of the Xebec team, provide the adaptability to ensure reliable performance across different material compositions.
We are committed to creating custom-tailored solutions that improve quality, reduce cycle times, and eliminate inefficiencies caused by traditional nylon brushes. Unlike nylon impregnated brushes, Xebec brushes generate minimal debris, making them ideal for use in clean room environments.
>>Learn more about improving clean room environments with Xebec.
Why Machinists are Switching from Nylon to Xebec Ceramic Fiber Brushes
One of the most significant advantages of Xebec tools is not just the technology, but the freedom we have to collaborate with customers to develop solutions right for their needs.
We work directly with manufacturers and machine shops to understand their unique challenges and offer recommendations and tailored solutions to improve their deburring and surface finishing processes.
How Xebec collaborates with customers:
We listen to your needs and ideas and then develop solutions based on your feedback. Beyond delivering advanced deburring solutions, our customers say they experienced these benefits working with us:
- Improved efficiency, moving from manual to automated deburring.
- Increased productivity when employees are freed up to work on other tasks.
- Upskilling existing employees to learn new skills and advance their career.
- Better equipped to meet customer needs and industry expectations.
- Programmed paths for back deburring of 3D cross holes, curved surfaces and complex edge profiles.
>> Learn about our Xebec Back Burr Cutter & Path for Automation
Customer Focused Solutions
We collaborate with many large precision machine shops within the aerospace and space industry and provide them with the tools and expertise to exceed quality and performance standards while meeting stringent testing requirements for surface finish.
Our vast experience working with unpredictable materials and proprietary alloys means we can identify the right tools for the job, eliminating costly trial and error.
>> The Secret to Deburring Success: Application Expertise from Xebec
Act Now: Upgrade Your Deburring Process Today
Manufacturers, machine shops and high-production CNC facilities can significantly benefit from switching from nylon brushes to Xebec cutting tools. Here’s how to take the next step:
- Schedule a Consultation: Our team is ready to evaluate your current deburring challenges and recommend the best solutions. Experience the difference firsthand with a demo of Xebec ceramic fiber brushes on your application.
- Guide for CNC Precision Manufacturing: Actionable advice for overcoming common obstacles and gaining a competitive edge. Read.
Conclusion
Xebec ceramic fiber brushes are not just an alternative to nylon brushes—they are an essential upgrade for machine shops that demand precision, efficiency, and reliability. Whether dealing with Exotic Alloys, high Rockwell hardness, strict Ra specifications or creating consistent lay patterns, Xebec cutting tools provide a superior solution.
Our expert team is here to help you find the right tool for your specific application, ensuring your machining process is as efficient and precise as possible.
Are you ready to eliminate inefficiencies and achieve the highest precision in deburring? Contact us today to learn more about how Xebec cutting tools can transform your operations.