Do you produce parts used in aerospace, defense, communications and/or exploration industries?
These industries call for many complex parts with strict requirements, including tight tolerances, precise edge breaks and surface finishes, specific lay patterns, heat- and pressure-resistance and more. The parts themselves include everything from fasteners, antennas and valves to turbine blades, doors and wings.
Upon assembly, the end-product could be a drone, satellite or rocket, to name a few common assemblies. Additionally, you could be working with a variety of materials, including Inconel, titanium, various alloys or composites, aluminum and more. Some of these materials will be more challenging to work because of their hardness, such as Inconel.
However, when you have modern, automated tools like Xebec’s deburring brushes, you can easily work many of the hardest metals along with a variety of other materials successfully.
Whether you manufacture parts in-house for a company in one of these sectors or provide manufacturing services for companies that outsource deburring and finishing, the work you perform on each individual part is critical. Just one part failure can result in catastrophe so ensuring the end-product functions safely and appropriately is vital.
Metal Surface Finishes: The Importance in Aerospace and Defense Industries

Though no one aspect of the specifications is more important than the other, we want to focus on surface finish, how important it is to get it right and how you can ensure consistent and accurate finishes with Xebec Deburring Solutions.
>> Learn more about Surface Roughness and Surface Finishes.
Xebec deburring tools are effective for the manufacture of aerospace and defense components, as well as other communications and exploration-related industries. These tools are capable of achieving the appropriate finish for each part using an automated process, with the added benefit of deburring and finishing at the same time. You can often meet the required Ra value before the part comes off the machine, eliminating the post-machining processes of manual deburring and finishing.
In addition to making your operation more productive, automating with Xebec finishing tools increases the safety of your operators by lowering the opportunities for injuries. Some aerospace components, such as turbine blades, can have very sharp edges and hand deburring can result in a laceration and many missed days of work. That’s a headache a production supervisor doesn’t need.
>> Stop manually finishing critical parts – learn the ROI of automating with Xebec.
Meeting Required Surface Finish Specifications with Xebec
Surface finish is defined by the three characteristics of the surface: lay, surface roughness, and waviness. Surface roughness measures the closely spaced variations left by cutting tools or grinding wheels in the surface texture and is typically measured as Roughness Average (Ra).
Waviness is the measurement of the more widely spaced component of surface texture and is not as commonly used as surface roughness. It is typically used on parts such as ball bearings and flat milled sealing surfaces. Lay indicates the direction of the dominant texture pattern on the surface.
Xebec products can achieve nearly any surface finish necessary for aerospace, defense and related industries. These industries have many commonalities as far as expectations for surface finish.
Meeting Required Ra Values
For most parts in this industry, you’ll typically find that meeting a surface roughness of 8 Ra is the standard. When you use Xebec, in many cases, you’ll be able to achieve the appropriate surface finish without needing a post-machining process like polishing. This saves a significant amount of time and money without losing consistency, quality and reliability. It’s also more efficient and accurate than a manual process, with which it’s difficult to meet an exact Ra requirement.
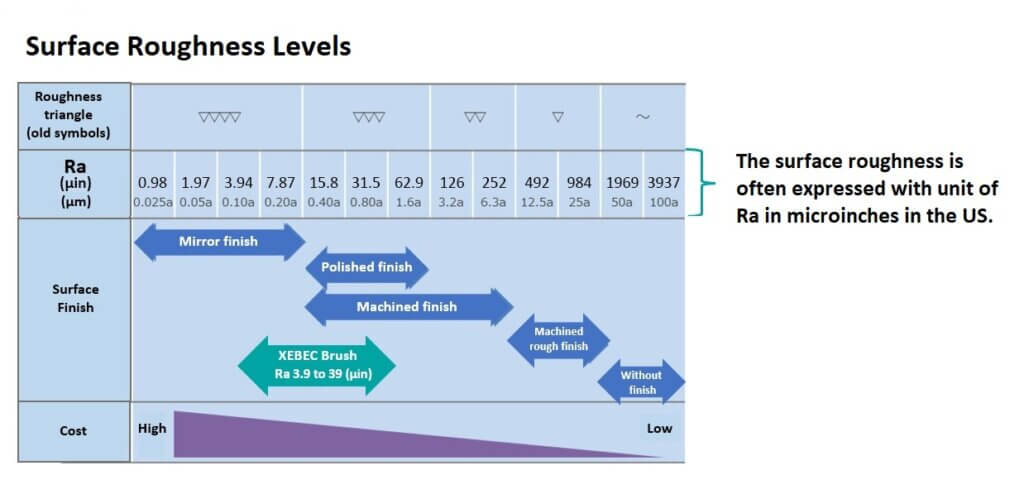
Xebec ceramic fiber brushes can help you achieve the required lay pattern specifications.
Meeting waviness specification
Waviness is defined as the periodic variations in surface finish of a part. This results from machining flaws and warping from heat and cold. The peak-to-peak spacing of the waves is known as the waviness spacing (Wsm). These surface flaws are small, brief, and regular, differentiating them from irregular surface flaws.
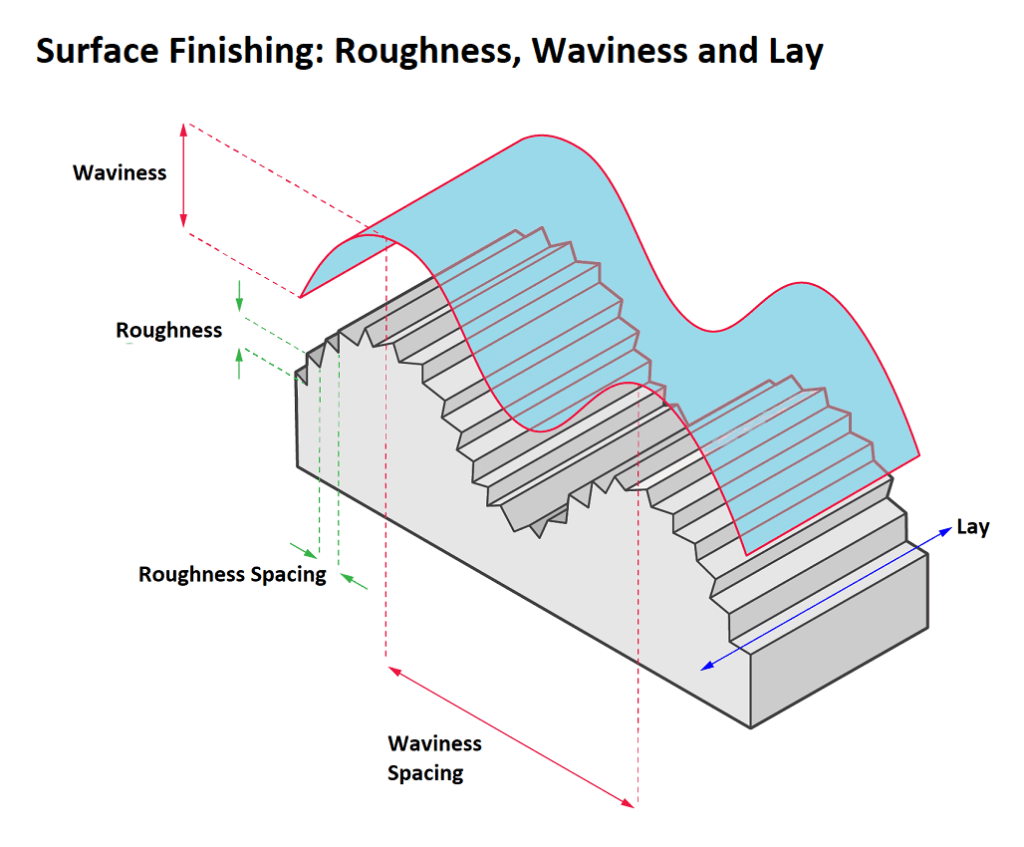
Meeting Lay Pattern Specifications
Many parts for these industries require a specific lay pattern – most often circular. Lay is the first component of surface texture and the direction of the pattern is created by the machining process. Other lay patterns include parallel, perpendicular and cross-hatched, to name a few.
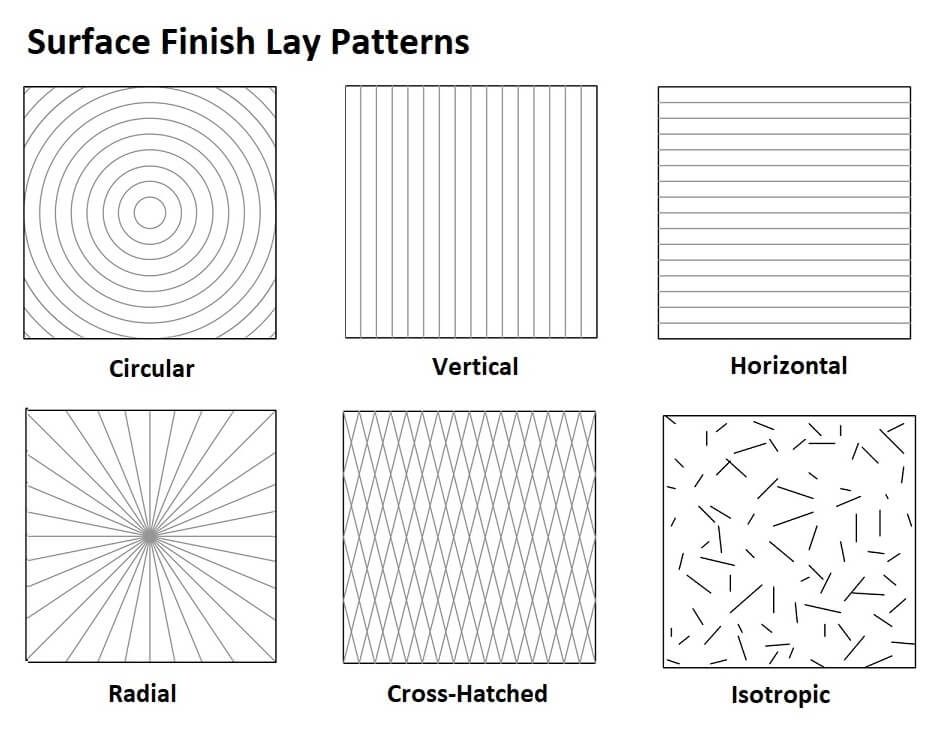
Here are a few examples of how Xebec products are effective for meeting surface finishing requirements in these specific industries:
- You can achieve the specified Ra you need for almost all applications.
- You can achieve a circular lay pattern with our brushes, which is often required for surfaces where adhesion is important or fluid must flow a certain way.
- You won’t have to worry about leaving stock on the part to avoid removing too much physical material during the finishing process.
- Since automated finishing and deburring with Xebec brushes is a consistent, reliable process, you’ll easily meet specifications for waviness.
>> Learn How Xebec Helps Aerospace Industry Manufacturers Reach New Heights
Are you curious how Xebec products can fit into – and improve – your current surface finishing processes? Watch more cool videos on our YouTube Channel and contact us to speak with our application experts. We know your processes are proprietary and work with many top-tier aerospace firms and defense contractors requiring NDA’s.