Manual deburring and finishing are two of the most persistent holdovers from the time before advanced manufacturing; before modern robotics, connectivity, automation and more; before automated deburring and finishing with tools like Xebec deburring brushes was even possible.
Why?
It can be a major pain to change a process that works as-is. And who’s to say it’ll be worth it? Or that it will be a success?
In some cases, you could simply take a lap around the shop floor to see how that manual work is already holding up operations – and costing you time and money.
At Xebec Deburring Technologies, we regularly witness the relief – both mental and financial – when manufacturers implement our automated deburring tools and shed their costly, tedious manual processes.
It’s the time to be bold and not let the fear of change impede progress. We show you how to Be the Hero for your organization by making the case for modern deburring.
Automating with Xebec ceramic fiber brushes is not only more cost- and time-effective than deburring and finishing by hand, but also produces high-quality parts to spec – consistently. This brush performs more like a cutting tool, and it simultaneously deburrs and finishes the part. You can expect a clear and quick return on your investment, including reduced scrap and rework. And you’ll find surprising ways this one simple swap can help you solve other common manufacturing challenges.
That’s especially true if you work with one of our application experts from the beginning stages of your decision-making. Their invaluable knowledge is the real secret to success with Xebec products. They can help set you up to embrace the future of CNC machining and capture the most ROI from automating deburring at your facility.
Manual Deburring Process Issues and Quality Concerns
If you currently deburr and finish parts by hand at your shop, you’ve likely noticed the most common issues, such as:
- Inconsistent results
- Inefficient, time-consuming processes
- Productivity that lags and wains
- Unreliable quality
- High rate of rework
- High rate of scrap
If you recognize any of these, it’s worth exploring how they’re costing you.
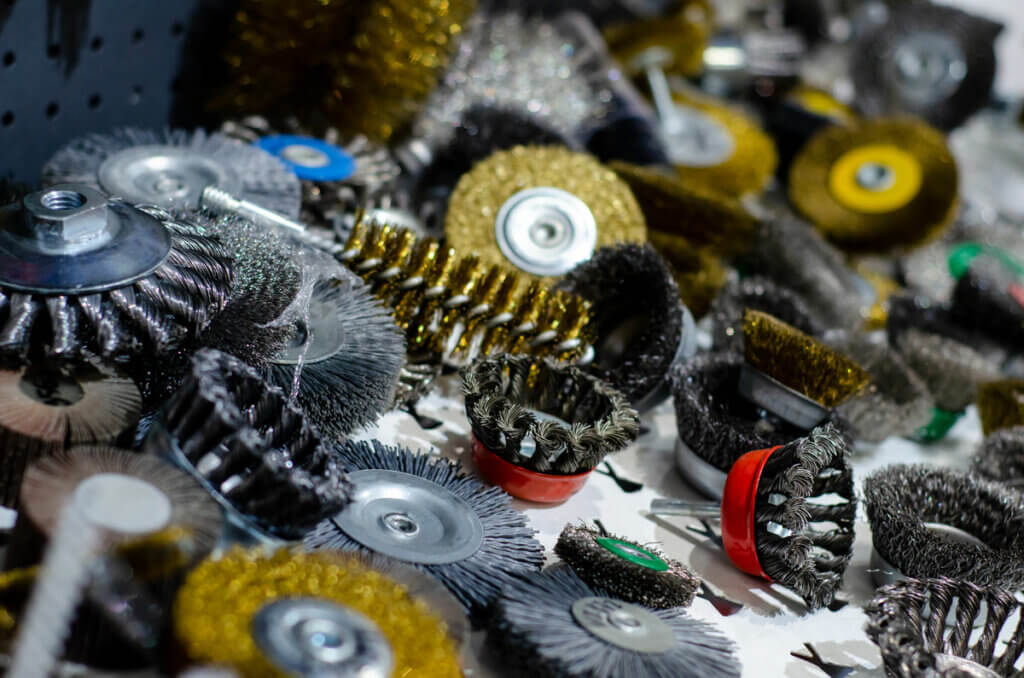
Deburring and finishing by hand is inherently inconsistent.
Cost: Rework, Scrap, Labor, Reputational Damage, End Use Failure
If the way you deburr and finish isn’t consistent, then you’re going to struggle to get consistent results.
Best-case-scenario, all employees use the same high-quality manual deburring tools and machines to perform the work following strict guidelines. But even in this scenario, each employee is going to perform differently, and even individual employees’ performance will change day to day and hour to hour. Inconsistent deburring depths and speeds will mean you can’t rely on parts to pass QA with ease.
In a less ideal scenario, employees are using their own methods and even handmade deburring tools to perform the work, making consistency an even greater challenge.
We don’t need to tell you what’s so bad about inconsistency. You see it yourself when it affects your operations. You can’t rely on parts to keep moving forward as projected. They’re either sent back from QA for rework, where they’ll hold up production, or they’re scrapped. Or, if they make it through QA to the customer, you risk your reputation and the function of the end product.
And don’t even get us started on how inconsistency affects potential additional processes down the line, such as anodizing. At that point, if there’s a problem with the finish, it’ll be too late for rework and you’ll have to scrap the part.
With an automated process using Xebec ceramic fiber brushes, you can expect consistent, quality results. The ceramic fiber doesn’t deform, and it is incredibly durable and long-lasting. Even if you need to use hand polishing for the final step, a Xebec brush will get you to your required surface roughness (Ra) much faster. You can expect Xebec to outperform the alternatives – and vastly outperform manual methods.

Humans are challenged in meeting super tight specifications.
Cost: Scrap, Labor, Inability to Accept Certain Jobs
In some cases, it can seem (and even be) impossible for your employees to achieve the spec required on a part by hand. For example, critical, high-performance parts for industries like aerospace and energy may require precise edge breaks to perform in their final assembly. This is challenging to achieve with hand-deburring tools and human capabilities, particularly with thin parts. If the break isn’t precise, you’ll likely have to scrap an expensive part – which could realistically cost upwards of hundreds of thousands of dollars.
Xebec tools can achieve tight tolerances and edge breaks reliably, so you won’t find yourself scrapping costly parts or passing up high-value jobs.
Human error and handling lead to more scrap and rework.
Cost: Rework, Scrap, Labor, Employee Injury, Net Time Waste, Resource Waste
Aside from inconsistent output and failure to meet tight specifications, there are many other ways manual deburring results in scrap and rework.
Take handling for example. In a manual process, parts are touched and handled far more than when the process is automated in a CNC machine or robot. This risks damage from mishandling and dropping. Also, a slip of the hand or a sneeze could render a part completely unusable – and may even cause injury to the employee. Further, depending on the hand deburring method you’re using, the process may leave abrasive particles behind in the part that aren’t acceptable for the end use.
Scrap and rework are more than a pain. They’re expensive. In one case, you have to jam up productivity to get a part right. In the other, you’re out the cost of the part, as well as the time spent on it thus far. Think setup time, cost of getting materials, quality control work and more.
Finishing a jet turbine blade is a great example of this and other issues that can be solved with an automated process. These parts are tricky to work both on and off the machine, with tight specifications that demand tedious work and handling. They’re cumbersome and easy to drop, which is hazardous to employees and could damage the part. However, Xebec Deburring Technologies has a proven method manufacturers can use to automate turbine blade finishing, eliminating many issues related to handling and easily achieving specifications.
Learn more about automating turbine blade finishing with Xebec. >>
Expected inconsistency means more extensive quality control.
Cost: Labor, Net Time Waste
If you can’t rely on parts to be consistent, your quality control department will have to spend more time inspecting parts to make sure they’re ready to go. This increases the overall net production time for a part. Compared this to Xebec ceramic fiber brushes, which are so reliable that parts are often ready to ship right off the machine. So, while QA is still necessary, it won’t require as much time and attention, contributing to a lower overall production time.
Learn more about how Xebec products save net production time. >>

Proven Results: Area Tool’s Experience Automating Deburring
A typical example of a customer finding relief from the high costs of manual deburring is Area Tool & Manufacturing, Inc. This precision manufacturing shop was hand-sanding barebow recurve risers and watching the costs of disposable discs add up, as well as the half-hour of labor to hand-polish each riser.
With Xebec brushes, they took the half-hour process down to five minutes. And instead of going through disc after disc, they’ve been able to finish around 350 risers over the course of two years using just one Xebec brush.
So, though five minutes per part was added onto the CNC machine, Area Tool still saves 20 minutes in overall production time – and up to 60 hours of labor per year. And employees who would otherwise hand-sand bows can instead get the next job going. As a result, Area Tool reports labor savings, increased productivity, a significant reduction in rejected bows and more.
Weigh the Benefits of Automated Deburring vs. Manual Work
If you’re concerned that quality issues related to manual deburring and finishing are affecting your bottom line, wasting valuable resources and even affecting your reputation, it’s worth having a conversation with one of our application experts to discuss how an automated process could help. For instance, with automated deburring, you could:
- Produce higher-quality parts
- Realize greater consistency
- Deburr and finish faster
- Reduce net production time
- Reduce scrap and rework (and associated costs)
- Increase health and safety for employees
- Accept more complex jobs
- Improve productivity
- Create more efficiency
To learn more, reach out to start the conversation or read our article featured in CTE: Automate Deburring and Finishing Operations.
Ready to make the case for automated deburring at your company? Let us help! We created a brochure with all the details you need to demonstrate the impact Xebec products could have on your operations.
Don’t be afraid to investigate new technologies by Xebec. Our consultants can show you how our tools can make a dramatic difference at your worksite. Be bold! Contact us to get started.