What’s possible on CNC machines has expanded and will continue to do so as new and innovative technologies are introduced across manufacturing. For example, today, it’s more feasible to set up a done-in-one machining process to help achieve lights-out manufacturing. Fortunately, the latest technologies do more than improve production time and product quality. They also help manufacturers mitigate challenges, from resource management to operational efficiency.
Embracing the future of CNC machining could help reduce the pressures of labor shortages, supply chain volatility, quality expectations, demands on production volume, competitive job costing and more. With a little relief from innovative CNC technology, such as automated deburring and finishing with Xebec products, you can be more productive and take on more jobs.
It’s the Right Time to Innovate Your CNC Operations
To most, upgrading CNC machines and processes doesn’t sound simple. You want your machines up and running as much as possible, you’re running on a lean staff and you have production deadlines to meet.
The thing is: These conditions aren’t going to change.
There’s never going to be a perfect time to innovate in an industry that is in constant motion. However, if you don’t make upgrades that alleviate the pressures of your production challenges, that pressure may just intensify. And you’ll miss out on the benefits your competitors are already reaping.
Perhaps most importantly, customers already expect the type of experience, cost and quality they receive from companies that have innovated CNC processes.
The good news is: You don’t have to shut down your operations and do a full-scale update, and you don’t necessarily need to purchase new machines.
In fact, most manufacturers can’t and don’t. Updating processes on one CNC machine can make a significant enough dent in the pressure. Whether you’ve got a CNC center with 50-100 machines or if you’re a machine shop with a handful of CNC machines, switching in a tool to automate deburring and finishing won’t disrupt production as much as you might think, especially when you first consult with our team of experts.
At Xebec, we’re at the forefront of manufacturing process innovation. Our application specialists are on the factory floors of top tier aerospace and medical organizations and working with those embracing the future, even if it’s just one tool at a time.
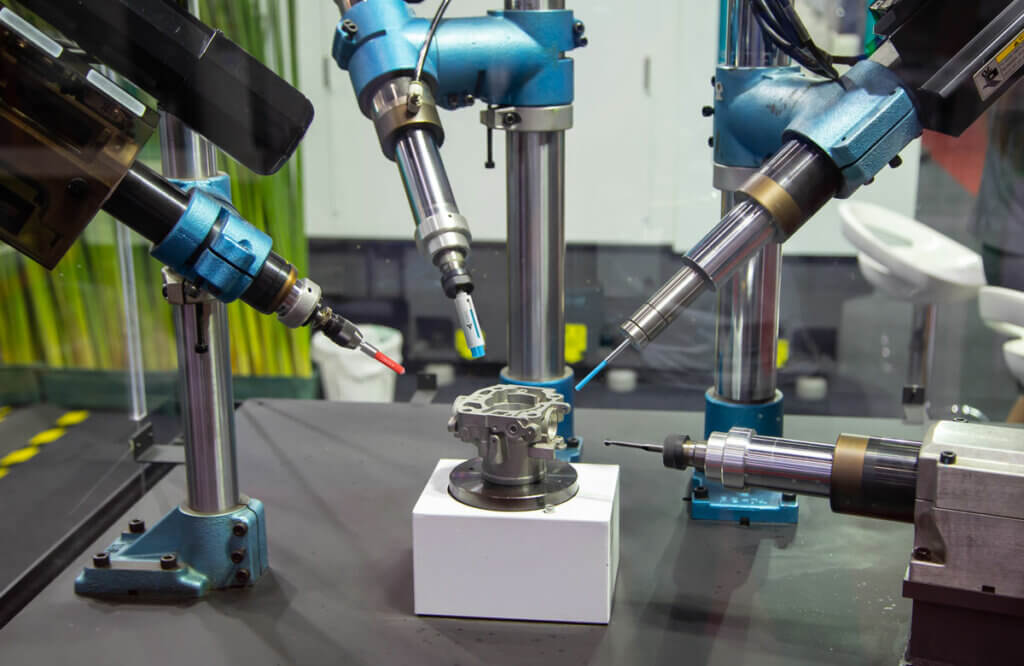
What Innovations are the Real Future for CNCs?
Some technologies fizzle as soon as they hit the market. They might not deliver enough value or underdeliver on quality, or it may be that they simply don’t work. If you’re looking to embrace technologies that will truly make a difference, it helps to know what’s trending and having an actual impact across the industry.
Automation
Automation is making a difference in many areas of manufacturing. As far as CNC machining, future factories are more likely to move more processes onto CNC machines to automate them. This reduces the number of times a part is moved and manipulated, and often reduces production time and possible damage per part. For example, many shops who currently manually deburr and finish parts will shift those processes onto the CNC, allowing for upskilling those employees. With a Xebec tool, both processes are performed at the same time, saving even more steps. There’s already an increase in investments in five-axis machines and larger tool changers, which enable manufacturers the flexibility to use more tools in the machine.
Robotics
Robots are another technology you’ll find in various areas of a manufacturing facility. However, when it comes to CNC machining, there are specific use cases that can make a major difference. Robots can do the heavy lifting when you need to move a part from one phase to another. They can also be integrated as tool and fixture changers for the CNC machine. In some cases, they can even act as alternatives to CNC machining altogether, performing the necessary work in robotic deburring cells.
Internet of Things Technology
Internet of Things (IoT) technology has revolutionized many processes for manufacturers, from inventory management to logistics to sophisticated monitoring systems for machine maintenance. IoT can be used to facilitate preventative and predictive maintenance on CNC machines, helping to monitor and track its performance to prevent unexpected malfunctions and reduce downtime. Manufacturers are increasingly interested in how to use Augmented Reality for CNC applications such as a support tool in the machining process for better production monitoring, quality control, employee training, and documentation.
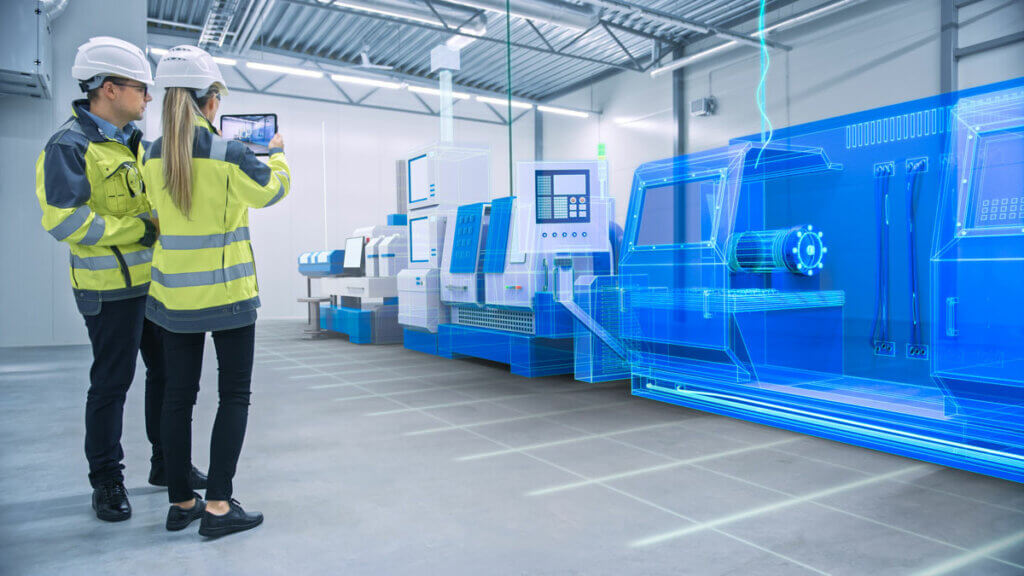
Options for Innovating CNC Operations with Xebec
In many cases, manufacturers won’t have to purchase new machines to embrace the future of CNC machining. You can often equip existing machines with the right tools and capabilities to elevate your processes and improve performance. Your next step depends on how you operate today, your budget and your goals. Here, we’ll outline how you can transform the steps of deburring and finishing based on your current processes.
1. Currently manual and unable to automate.
There is still room for major improvement if you want to stick with manual deburring and finishing. Low-cost hand-deburring tools, or even ad-hoc tools made from items on the shop floor, often mean a higher rate of scrap, constant tool replacement and inconsistency in your results. Xebec Deburring Technologies has a host of hand tools that will help you achieve better quality, faster and with a longer tool life.
Learn how to improve hand-deburring with Xebec. >>
2. Currently manual and ready to automate.
Moving deburring and finishing onto the CNC machine to automate the processes has major benefits for manufacturers today. Manual deburring often costs more with less consistent results than automated – by a drastic amount. It may seem that it’s adding time on your CNC machine, but the time saved overall outweighs that difference on the machine. With automated deburring and finishing using Xebec products, you’ll realize greater quality, more reliability and less scrap and rework than with manual work.
Learn more about increasing machine cycle time to save net production time with Xebec. >>
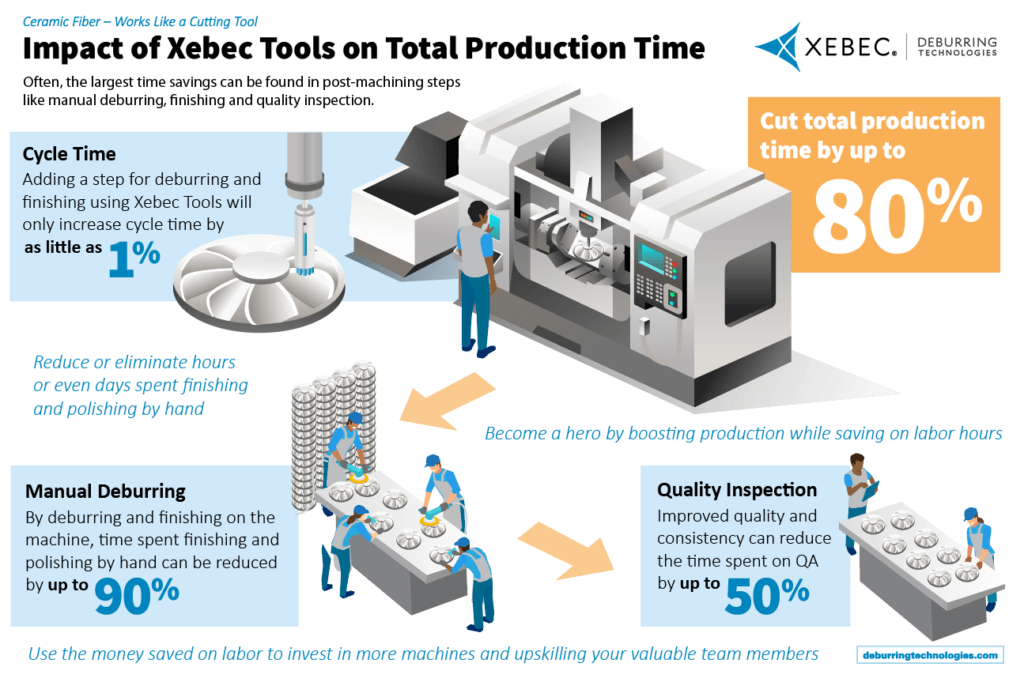
3. Currently automated and ready for better tooling.
There are many automated deburring brushes available on the market. However, most of them fall short of the performance and longevity of Xebec deburring tools. Due to the continuous ceramic fiber, Xebec deburring brushes and tools perform more like cutting tools than regular brushes. They also won’t deform, providing consistent results you can count on.
Learn more about optimizing performance and maximizing tool life for Xebec. >>
4. Currently manual or automated and ready for a new CNC.
You may be in the position to upgrade from no CNC or a 3-axis CNC to a 5-axis CNC to support more tools in the machine and accomplish more in one run. Such an investment could get you closer to lights-out manufacturing, improve production time, allow you to do more with existing employees and resources, and much more.
If you’d like to learn more about taking the next step in CNC machining, reach out to us. We have a wide depth of experience and work with manufacturers across industries, including aerospace, medical, energy, powertrain and firearms. Contact the Xebec team to learn more.