Sometimes businesses stick with familiar tools and working methods simply because they feel tried and true — whereas embracing new technology can seem like a leap into the unknown.
The paradox of playing it too safe can be the very thing that winds up putting you at risk — like the danger of overspending because you’re using outdated technology that’s no longer cost-effective, cutting into your potential profits. Or the peril of ceding ground to competitors who’ve been bolder about embracing transformative new solutions, such as robotic deburring and lights-out manufacturing solutions.
Deburring is a perfect case in point. For many understandable reasons, manufacturers have come to depend on tumbling as an alternative to manual deburring and finishing of metal parts.
However, there are also real downsides to the use of tumbling — many of which can be solved through a smarter process that’s already available such as using automated deburring and finishing ceramic fiber brushes by Xebec, which are more controllable, consistent and precise.
Tumbling vs. Manual Deburring: What Advantages Does It Offer?
Tumbling is still a technique that manufacturers and machine shops have come to lean on when converting from manual deburring. There are several advantages of tumbling over manual deburring:
- Cost. When compared to manual deburring and finishing, tumbling can be more cost-effective and is generally less labor-intensive.
- Efficiency. After manual deburring, tumbling can finish multiple parts at the same time, which can save time — especially in large-scale production.
- Surface Quality. The use of tumbling media makes it possible to blend forgings and castings, deburr machine parts, and burnish stampings to a high finish.
- Stress Relief. The tumbling process can also impart a degree of stress relief to the finished pieces, adding to their strength and durability.
- Finishes. You can use various types of tumbling media (including ceramic, steel, plastic, and organic material among others) to arrive at different finishes — ranging from heavy deburring to fine polishing — by implementing customized processes reliant on experienced technicians.
But here’s the key thing to note about these advantages: they mainly hold true when in comparison to manual deburring.
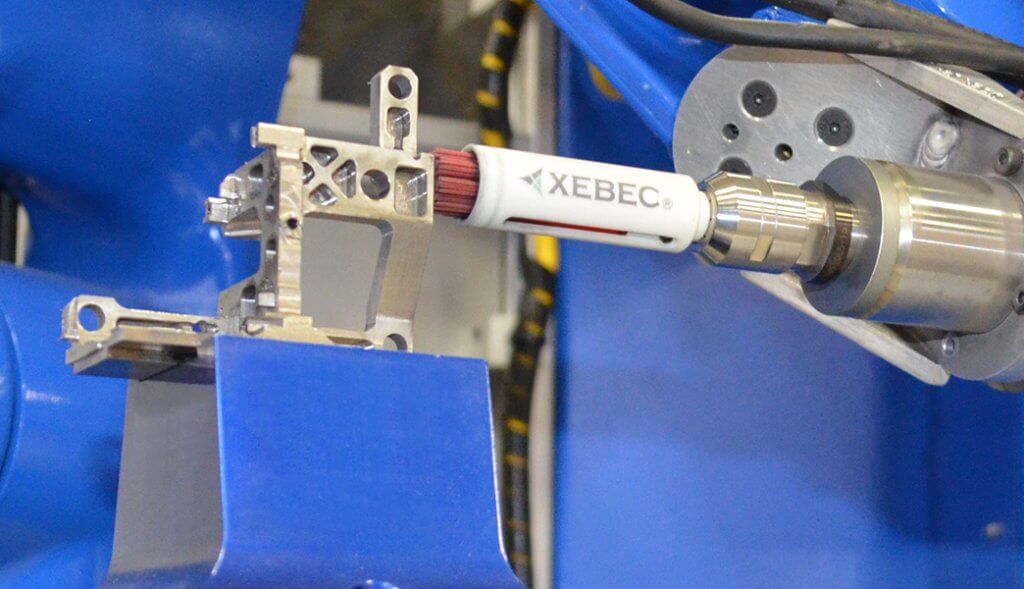
That’s because, while still common, manual deburring is really only viable for occasional small jobs — it’s not efficient or cost-effective for anything else.
But the truth is, although tumbling represents a step forward over the manual approach, it’s now an equally large step behind a newer and more efficient way of doing things – using Xebec’s innovative ceramic fiber brushes directly in your CNCs or robotic operations.
>> Xebec Guide for CNC Precision Manufacturing: Overcome Obstacles to Success
To understand why, let’s look at some of the pitfalls and limitations of tumbling.
The Devil in the Details: Types of Tumbling Media
One of the biggest challenges of tumbling is that choosing the right media comes with a lot of complexities. That’s important because the type of tumbling material you choose makes a significant difference in the final outcome.
Whether you’re using vibratory finishing equipment like centrifugal barrel machines, automatic surface finishing machines, or centrifugal disc finishing machines, tumbling can produce finished surfaces for previously machined items. But the final results you achieve will be dependent on not just the type of machine you use but the specific kind of tumbling media that’s used.
- Plastic tumbling media is a workable choice for polishing and deburring soft metals. But a key limitation of plastic media is that it doesn’t help to polish the surface or provide a high shine, it just produces a matte finish, while Xebec brushes can deburr and finish in a one-step process.
- Ceramic media can be good for cutting hard materials like steel as well as for deep abrasion of plastic materials. It’s powerful and durable, which is why Xebec brushes are made from ceramic fiber, allowing them perform like a cutting tool. However, in a tumbler, ceramic media can be too harsh for more delicate pieces and may create chips and fragments that can get lodged in nooks and crannies.
- Stainless steel media can help with achieving high shine and a lot of deburring and burnishing for metal parts after deburring, and can be a good option for plastic and ceramic parts.
- Porcelain media is best suited for metal parts that have already been deburred, as a way of giving them a final polish necessitating an extra step.
- Organic media — including plant-derived materials like peanut shells, walnut shells, coconut shells, or corncobs — can be an effective (and sustainable) choice for light deburring jobs, but can’t tackle harder materials such as titanium and others used in aerospace technologies.
Adding to all this complexity, tumbling media comes in a variety of sizes and shapes, which must be carefully chosen to align with each process.
In terms of size, larger media must be used with a certain amount of caution, since smaller, fragile parts can be damaged by large media. Another crucial consideration is making sure media doesn’t get stuck in holes or slots of the components or parts you’re finishing. For this reason, choosing the right media is critical and requires expertise.
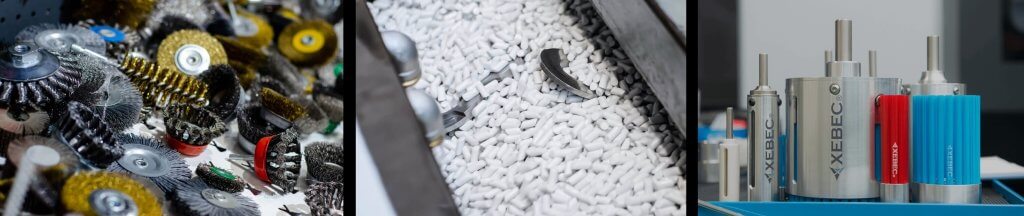
The Downsides of Tumbling: Where It Falls Short
With those considerations in mind, here are some of primary reasons why tumbling is no longer the best approach in most cases.
- Tumbling is expensive in terms of time and labor. That’s partly because the process itself is so cumbersome and inefficient. A lot of time needs to be spent loading and unloading different kinds of tumbling media for different jobs. Cleaning media out of machines in order to put a different kind in eats up valuable time and requires transport to a safe disposal site.
- Transporting parts and media adds to the expense. In some facilities, the tumblers are located on the other side of the facility from the CNCs and have to be loaded and transported to the machines by team members— adding all sorts of delays to the process. It’s even worse if the manufacturer outsources the parts to be deburred by tumbling, because they incur additional costs in terms of transport and waiting time. We visited one company that spent $2 million in costs including logistics and transit in order to move parts to be deburred and returned. And the process required waiting anywhere from 7 to 14 days for turnaround, making it painfully slow and delaying shipment and invoicing.
- Choosing the right tumbling media is complicated, with a variety of pitfalls. As discussed above, there are a lot of complexities to consider, and sometimes it’s difficult to find the baby-bear’s porridge that’s just right for the job. The people who run the machines need a very precise knowledge of which media goes with what, and why. It’s hard to gain and retain that type of knowledge.
- Tumbling machines and media hogs up space in warehouses and facilities. Tumbling machines and media storage spaces use valuable warehouse space. Additional CNCs can be utilized in spaces taken up by tumblers and the numerous large bags or boxes of media for different jobs. Managing all of that media can become a time-consuming job in itself.
- Disposing of tumbling media can be burdensome. Once the media has been used, it needs to be dealt with in a sustainable and environmentally friendly way, which can create a whole new set of challenges.
Automated Deburring with Robots
The Xebec Advantage: Game-Changing Benefits by Automated Deburring
Although it’s true that tumbling offers advantages over manual deburring with a brush, by the same token, tumbling is outclassed by Xebec’s sophisticated, high-precision, automated ceramic brushes — which actually perform more like cutting tools than brushes, and significantly outperform other technologies in CNC machines.
Xebec’s ceramic fiber brushes are highly durable, and they get the job done more efficiently than tumbling does. In fact, for almost every one of the benefits of tumbling listed earlier, Xebec delivers better results and bigger savings. Most importantly, for high production manufacturing facilities and machine shops, Xebec automated deburring and finishing products can be used within CNCs and robotic processes to achieve lights-out automation.
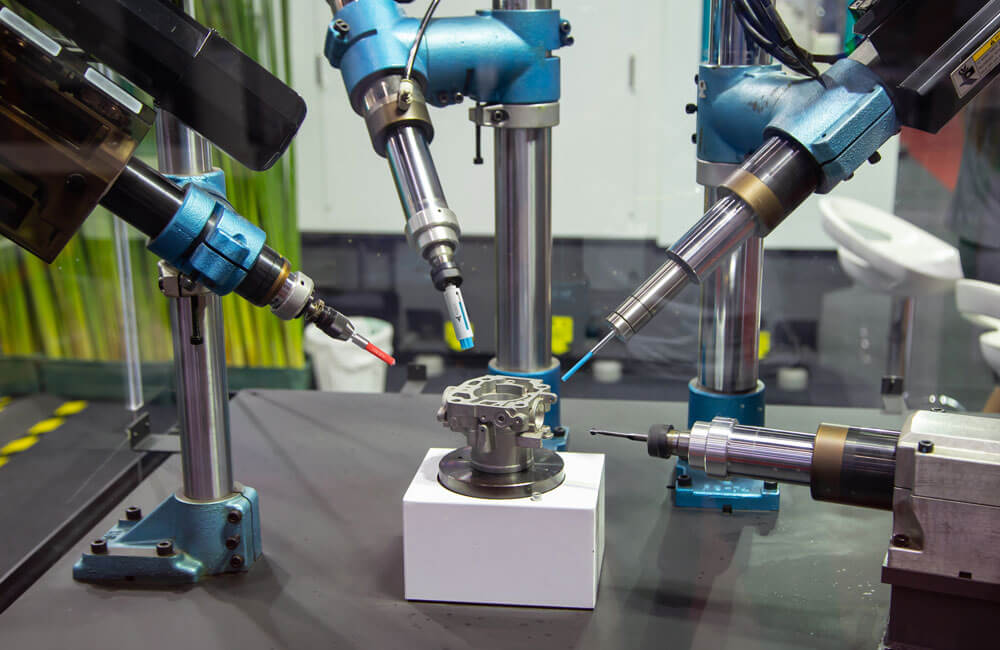
Here are three of the most important payoffs that Xebec can bring you:
Xebec is dramatically faster than tumbling or other cutting tools. Most cutting tools run fairly slow, while Xebec is typically two to four times faster than what any competitors run. And compared to tumbling, the time savings Xebec can deliver are breathtaking. For example, a given set of parts might take three hours to tumble — whereas Xebec can deburr and finish 300 of those same parts in the space of an hour. These are the kinds of game-changing results that make believers out of manufacturers who’ve seen what Xebec can do.
Xebec is automation-friendly. Reliance on tumbling can prevent automation and make lights-out manufacturing impossible. Tumbling requires careful attention and supervision to the complexities of tumbling media and the manual process of loading, unloading, cleaning, and maintaining the machines — time and labor that are saved by Xebec’s ceramic brush-based approach. And with high-pressure deburring, there’s always a risk in creating a change in the dimensions, the surface finish or the tolerance. With Xebec, you can automatically program the system to take the parts down to a precise surface roughness, without a lot of additional programming. That reduces the burden of attention and supervision in a way that’s profoundly liberating. In fact, you can use the time saved to upskill employees and overcome labor shortages.
Xebec lowers longterm costs. Although Xebec may come with higher upfront costs than other processes, the speed, efficiency, and performance delivered more than offset the initial investment. In fact, by providing longer tool life, faster processes, and lower scrap levels, Xebec winds up delivering a lower cost for each piece produced.
>> Calculate your ROI using automated deburring and finishing products from Xebec.
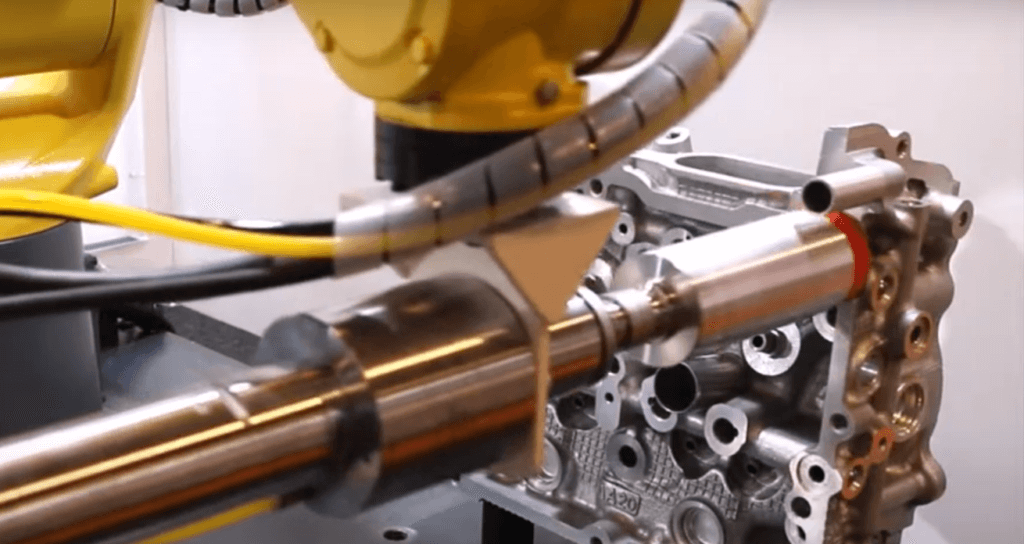
Xebec is ideal for high precision, high production facilities in the aerospace, medical, energy, firearms and powertrain industries.
Ready to explore whether Xebec is the right tool for you? Reach out to discuss your process with one of our experienced, knowledgeable team members. Be your company’s hero and make the case for modern deburring.