The impact of the powertrain industry extends beyond transportation and influences countless aspects of modern life and future development, such as economic growth, technological progress, environmental sustainability and global competitiveness.
According to the Global Powertrain Market – Industry Reports, the powertrain industry is expected to reach $3.2 billion by 2030. But beyond impressive growth, the industry is under increased pressure to design parts that meet today’s high standards and performance requirements. Stringent emissions standards and rising fuel costs are driving innovation in the manufacture of powertrain components.
The need for higher efficiency and improvements of powertrain components are instrumental for sustainability initiatives like reduced fuel consumption and emissions. However, three critical factors to consider during manufacturing for optimal performance are geometrical surface accuracy, surface texture and surface integrity.
Let’s explore why performance hinges on these factors:
Why are Burr Removal and Surface Finishing Critical to Powertrain Performance?
Burrs are small imperfections left on machined metal parts which can lead to negatives effects, such as:
- Injury from workers handling sharp parts
- Part failure from weak spots
- System malfunctions from part not seating properly or jamming
- Less consistent machining process
- Degraded appearance of machine parts
When machining debris is left behind during the machining process, the results can be catastrophic.
For instance, in manufacturing V6 engines, any debris left over from the machining process could be problematic due to the potential for debris to adhere to main bearings in the crankshaft. These bearings could fail and result in engine knock, rough running, a no-start or, even worse, a sudden loss of power while at speed.
When machining debris is not properly cleaned from impacted engines during their construction phase, an entire batch could be contaminated and must be recalled. This could result in a significant hit for engine manufacturers for automobiles and other applications.
Using burr-free and debris-free parts with the correct finish, and meeting strict specifications, ensures a good seal in powertrain applications and reduces the likelihood of adverse impact. Here’s how:
Improved Performance and Efficiency
Burrs can interfere with the precise fitting of components, leading to misalignments and disruption of fluids (oils, coolant) that impact overall performance of the powertrain system. Alternatively, smooth surfaces can reduce friction between moving parts, reducing wear and tear and improving efficiency.
Enhanced Durability and Longevity
Burrs and rough surfaces can increase wear and tear on components and create stress concentrations on the part. Removal of burrs aids in maintaining part integrity and reliability.
Increased Safety and Consistency
Burrs can break off and contaminate systems leading to premature failure. By removing burrs, you can ensure high-quality surface finishes on components for more consistent and safe performance.
Heat, Vibration and Noise Control
Smooth surfaces enhance thermal conductivity, helping to manage operating temperatures and prevent overheating. Rough surfaces can also contribute to increased noise and vibration. By removing burrs and imperfections, you reduce the potential for these disruptions.
Better Assembly and Maintenance
Burrs can cause component parts not to fit properly, hindering the assembly process and leading to increased scrap and cycle time. When components are free of burrs, they are easier to clean, inspect and spot potential issues for improved maintenance.
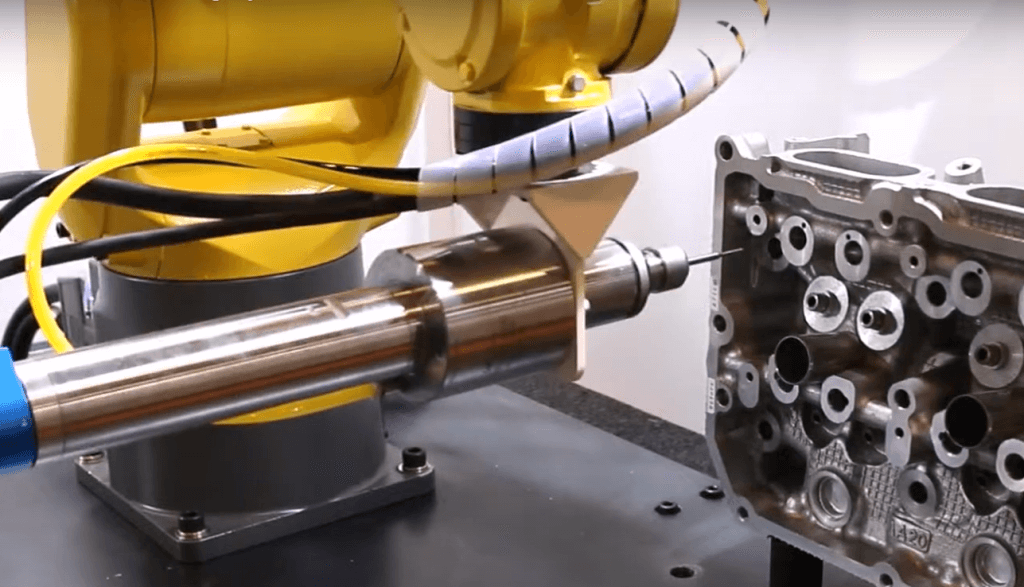
Powertrain Components Compatible with Automated Deburring
Powertrain industry manufacturers deal with components ranging in size and complexity, primarily those related to transmissions and engines. You might serve the automotive industry, or you might produce parts for farm and construction equipment, aerospace companies, energy sectors and more. All these components require meeting tight tolerances and specific finish requirements.
The list of components used for powertrain applications is long and includes:
- Engines
- Transmissions
- Exhaust systems
- Ignition systems
- Fuel injection systems
- Differentials (gear trains)
- Driveshafts
- Camshafts
- Clutches
- Flywheels
- Valves
- Manifolds
Xebec Deburring Technologies has a variety of brushes that act like cutting tools designed for these applications. These brushes can be used to automate a consistent deburring and finishing one-step process for many of these components, no matter their size or complexity.
Here are just a few examples of Xebec deburring and finishing applications with powertrain components:
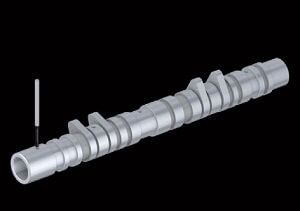
A camshaft is a cylindrical metal shaft responsible for the timely operation of the valves, helping to perform processes during the engine cycle. Back-deburring a camshaft with spring-type tools often results in over-deburring or incomplete deburring.
Automating the process with the Xebec Back Burr Cutter and Path results in a uniform edge quality in shorter operating time.
>> Video – CNC deburring of camshaft

Replacing nylon brushes’ insufficient grinding power with Xebec Surface brushes reduces the extra manual processing time needed for deburring. Xebec replaced it with automated, reliable deburring within the CNC, saving time and producing consistent, high-quality results.
>> Video – Automated Deburring of a Cam Cap
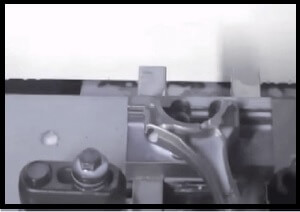
After milling the edge face, burrs were typically removed manually using a wire brush. This process was unable to remove all the burrs and deformed the part, causing quality control issues in mass production. Investing in automated deburring with Xebec ceramic fiber brushes resulted in a consistent quality outcome with increased production.
>> Video – Automated Deburring of a Connecting Rod (Edge Face)

Manual deburring leaves burrs remaining and inconsistent quality. Introducing automated deburring with the Xebec Stone Flexible Shaft tool in the machining center resulted in stable edge quality and cost reduction.
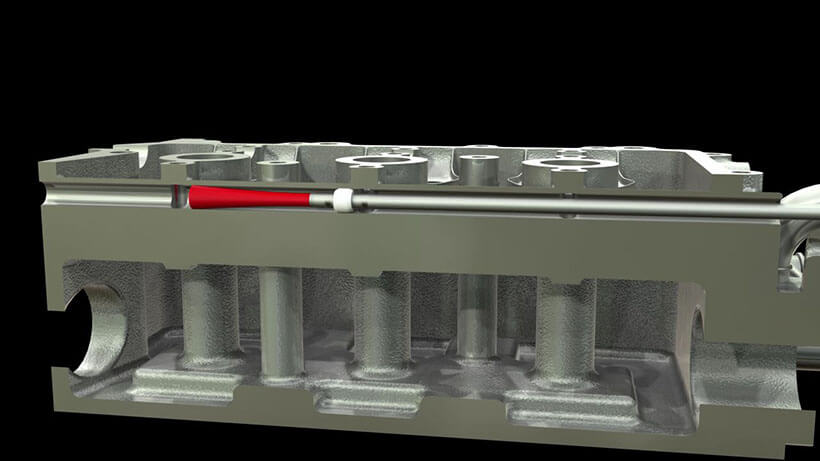
Cylinder Head Oil Gallery (Crosshole)
A Xebec Extra-long Crosshole brush was used to improve the crosshole deburring and internal polishing of the oil gallery of a cylinder head, typically done by nylon brushes. The Xebec solution ensured the removal of all burrs and cutter marks on the inner diameter.
>> Video: Automated Deburring of a Cylinder Head (Crosshole)
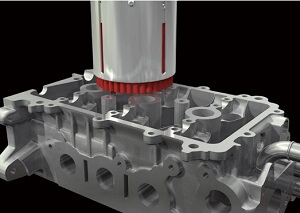
Using an abrasives-impregnated nylon brush, the deburring and finishing process used to take hours, and the brush left stains on the part, requiring extra time for removal. With Xebec’s Surface brush, a shorter cycle time was achieved via high-feed processing. Coolant contamination was reduced to one-third, eliminating time expended for cleaning.
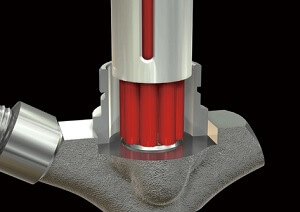
A Xebec Surface Brush was used to deburr and finish surfaces for the nozzle of an injector body. The Surface brush greatly improved the quality and consistency of the previously used abrasive-impregnated nylon brush. Xebec improved the surface roughness and reduced the cost of production by enabling random sampling instead of requiring a full inspection of each part.
>> Video: Deburring and Finishing of an Injector Body (Nozzle part)
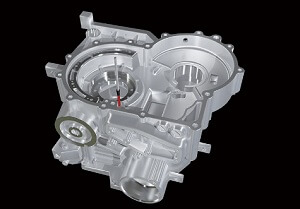
Using manual rotary brushes to deburr inside diameters takes significant time. Xebec replaced the previous rotary tool with an automated deburring solution for transmission case crossholes. This improved deburring and finish quality of the inside diameter and increased production.
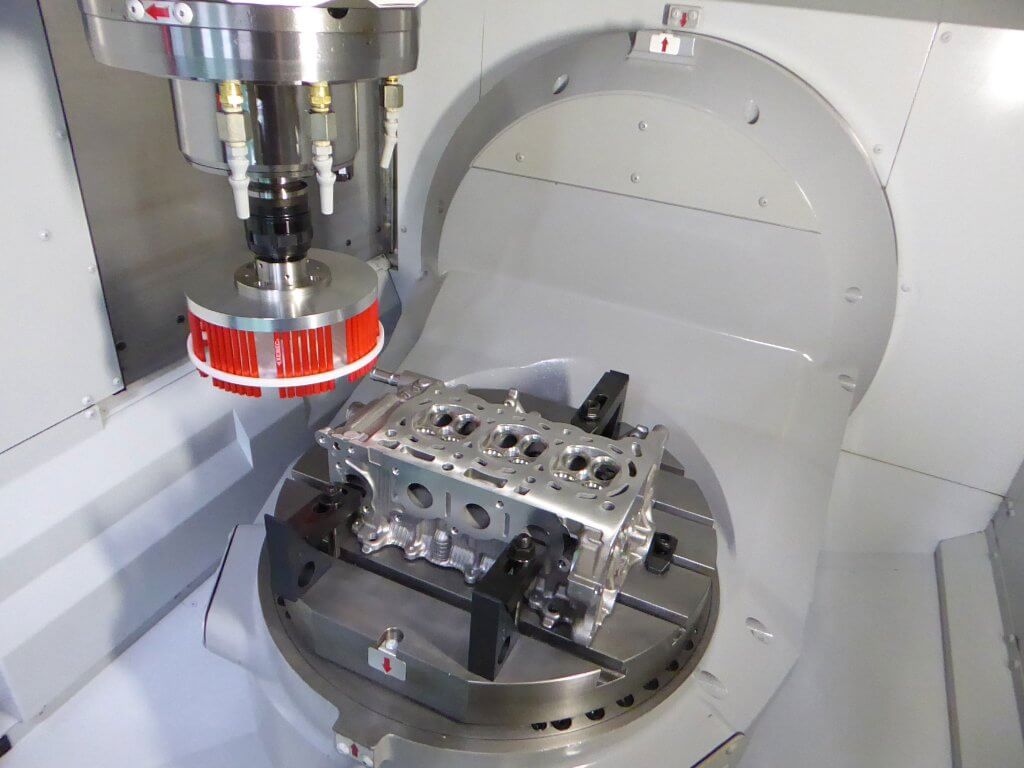
Consequences of Compromised Powertrain Components
Compromised powertrain components can have significant adverse effects on vehicle performance and reliability.
One of the primary consequences is reduced efficiency, leading to increased fuel consumption. When components such as the engine, transmission or drivetrain are not functioning optimally, the vehicle requires more energy to operate, consuming more fuel and increasing operational costs.
Compromised powertrain components can also cause irregular and unstable vehicle performance, such as erratic acceleration, poor handling and difficulty maintaining speed. This can be particularly dangerous in situations requiring precise control and maneuverability. Consider the impact of a military vehicle operating in harsh environments. A compromised powertrain can lead to mission failure and danger to personnel.
Beyond performance issues, compromised powertrain components can also lead to substantial financial and safety concerns. Frequent breakdowns and the need for more extensive repairs become inevitable as minor problems escalate into major mechanical failures if not addressed promptly. This results in higher maintenance costs and also increases the risk of accidents due to sudden failures while driving. For the manufacturers, warranty claims, legal issues, and expensive recalls can also result from decreased system reliability.
Taking it a step further, vehicles with compromised powertrain components are more likely to fail emissions tests, contributing to environmental pollution and potential legal repercussions — negating any sustainability initiatives.
Produce Consistent Quality Powertrain Components with Xebec
Xebec deburring and finishing tools give powertrain industry manufacturers the performance and reliability they need to serve the critical automotive industry or produce parts for farm and construction equipment, aerospace companies, energy sectors and more. The ceramic fiber acts more like a cutting tool; it doesn’t deform as it works and has superior grinding power. You’ll be able to deburr and finish parts more consistently – and faster and more cost-effectively – with these automated tools in place of manual methods.
Achieve more reliable consistency, meet and exceed customer expectations, improve safety and open the door for increased revenue opportunities. See how Xebec can help your precision CNC manufacturing overcome obstacles to success.
Reach out to learn more and start a conversation with our knowledgeable team about your deburring and finishing operations.