Aerospace components demand high precision and perfect quality to guarantee performance. Manufacturers that rely on manual work to deburr and finish aerospace components are finding it difficult to meet these requirements. Not only is it challenging to achieve consistent quality with manual processes, but it’s also difficult to meet demand with the enduring labor shortage and supply chain issues.
With the growing aerospace market, it’s more critical than ever for manufacturers to make smart investments that keep them moving forward despite today’s challenges and tomorrow’s projections.
Learn more about challenges facing manufacturers today in our eBook. >>
Tools that automate deburring and finishing are among those smart investments. In such an exacting industry, automating with the most effective, efficient tools available pays big dividends. Xebec ceramic fiber brushes outperform alternatives like wire and impregnated nylon brushes in both quality and speed, and they run laps around manual processes.
- A Confident Step Toward Automated Processes
- Tools that Contribute to Health and Safety Goals
- Performance that Simplifies Working Complex Components
- Processes that Enable Optimized Resource Management
- A Clear ROI versus Manual Deburring and Finishing
- A Future-Forward Investment that Supports Innovative Manufacturing
- Discuss an Application
- Contact Us
A Confident Step Toward Automated Processes

Manufacturers have automation goals across operations. Implementing automated deburring brushes in machining by CNC or robotics should be one of the simplest decisions toward those goals. The difference is dramatic, and it impacts cost and timing as well as quality. One change in your process can rocket your productivity and efficiency upward and reduce the number of parts you scrap due to quality issues, damage during handling, overly aggressive manual finishing and more.
When you automate deburring and finishing with Xebec products, you’ll realize:
- Improved, consistent outcomes
- Reduced setup and cycle time per part
- Improved productivity to increase throughput
- Capacity to meet high-precision requirements
- Better use of your resources, both human and machine
Learn more: The benefits of automated deburring and finishing in aerospace. >>
Improved, consistent outcomes help you retain your reputation for reliability and quality in the market. If a part isn’t finished according to specification, the negative consequences in aerospace – an industry that involves aircraft, rockets, spacecraft and more – could be grave.
Xebec tools can be used for numerous aerospace applications including aircraft or rocket bodies, turbine blades and disks, landing gear parts and engine brackets – to name just a few.
Learn about the many applications Xebec products can be used to improve production >>
Fortunately, parts that don’t meet spec typically don’t make it to the assembly phase. Many eyes are looking out along the way, ensuring no burr, cutter mark, or over-spec peak or valley in the surface is missed. With Xebec tools, you can achieve the Ra specifications required efficiently and consistently, reducing the amount of QA work needed.
Learn more: Deburring and finishing critical parts in the aerospace industry. >>
More specifically, Xebec ceramic fiber brushes are quite accomplished in automating surface finishing in aerospace, so manufacturers can achieve – and even exceed – the Ra requirements for ideal performance.
With Xebec, polishing may be necessary for an Ra below 4 microinches (µin). Still, the automated finishing that Xebec can conduct before the manual process creates an impressive surface that significantly reduces time needed in the post-machining phase.
Compared to manual finishing, automation is more cost- and time-efficient, particularly since Xebec tools perform both deburring and finishing at once.
Learn more: Modern surface finishing and polishing operations in manufacturing. >>
Deburring and finishing in one step gives aerospace manufacturers an incredible advantage, both in terms of time and labor. Aerospace parts often need a lot of handling, and many are of significant size. To have to turn large or complex parts multiple times to deburr, then multiple times to finish, is inefficient when you compare that process to the efficiency of Xebec deburring brushes.
With Xebec, the part stays on the CNC machine and is deburred and finished at once. And this is significant. Few systems can accomplish these two steps in one.
Learn more: Deburring and polishing in one step with Xebec. >>
Tools that Contribute to Health and Safety Goals
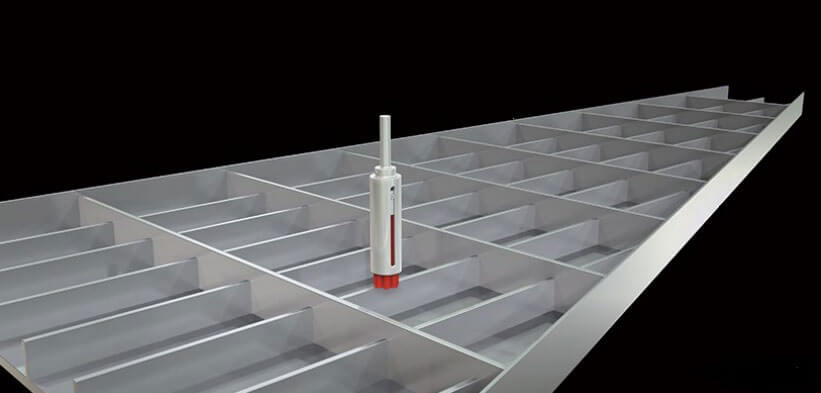
Manufacturers are always looking to improve health and safety in facilities. Manual deburring and finishing are processes that create risks for employees, both in the short and long term. In aerospace, working with large parts is physically demanding, and working with small, complex parts also causes physical strain. Dust and particles created in the process can cause damage as well, and a slip of the hand could lead to a large laceration.
Examples of injuries and strains operators experience with manual deburring and finishing include:
- Cuts and lacerations
- Carpal tunnel from repetitive motion
- Splinters from metal and debris
- Eye injuries from debris
When an automated option is not only available, but more cost-effective and better for productivity, it makes the decision to switch easy to defend. Automating these processes with Xebec deburring technologies greatly reduces the risk to the operator, keeping these tasks on the machine and limiting emissions of dust and particles beyond the machine.
Learn more: Improving health and safety for machine shop employees. >>
Performance that Simplifies Working Complex Components
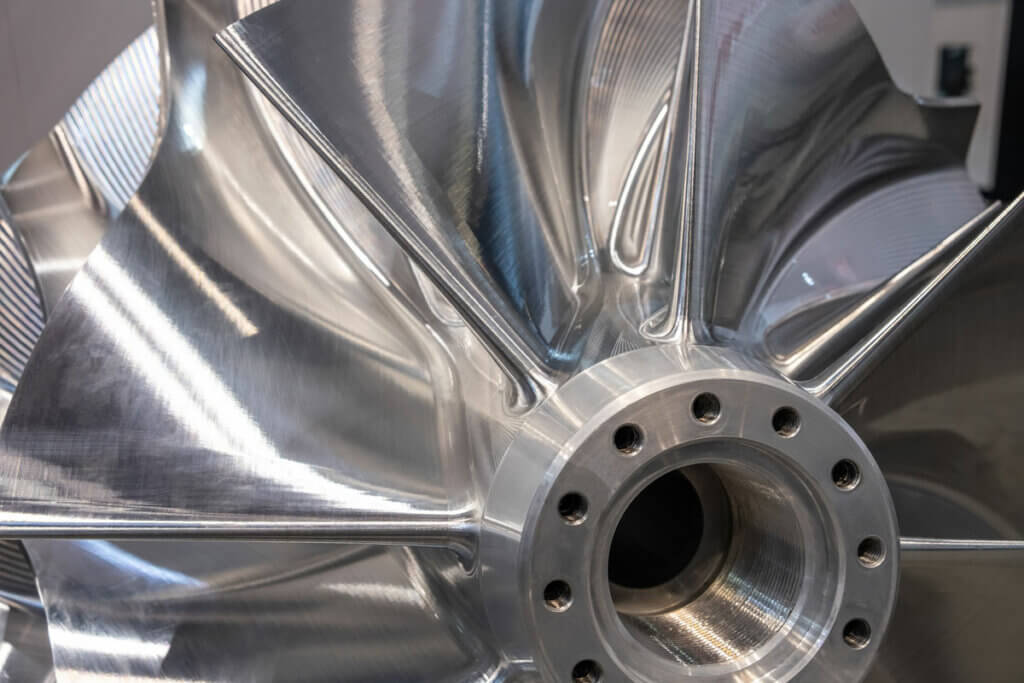
Xebec tools can help make aerospace manufacturers’ toughest jobs simpler by reliably automating the deburring and finishing processes. For instance, turbine blades are a common aerospace component – but they’re no walk in the park to produce and finish. The curved surface of a turbine blade makes it more challenging to achieve precision and quality reliably and efficiently. Further, many manufacturers still depend on manual deburring and finishing, which is often inconsistent and risks more scrap and rework.
The Xebec Brush Surface is an ideal tool to automate turbine blade deburring and finishing.
- It has superior grinding power and consistent cutting performance.
- You won’t have to spend as much time moving and fixturing parts.
- You can deburr and polish quickly and in one step, saving process time.
- It will get to your target Roughness Average (Ra) much faster than the alternatives
Additionally, Xebec has developed a method for deburring turbine blades with the Xebec Surface Brush that helps manufacturers achieve optimal results.
Learn how Xebec makes turbine blade manufacturing a cinch. >>
Processes that Enable Optimized Resource Management
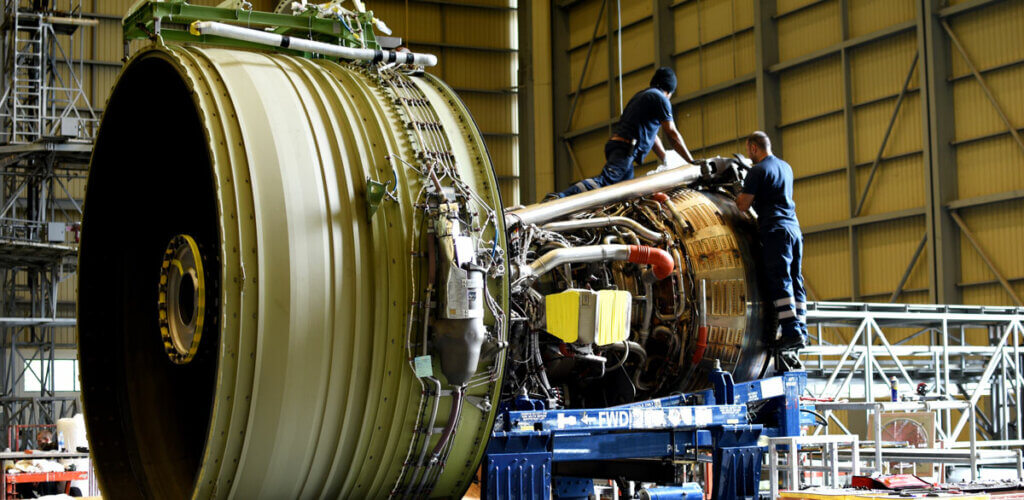
We’ve seen first-hand how the labor shortage is affecting manufacturers across the country. Aerospace manufacturers that implement automated deburring and finishing to replace manual processes can improve how they allocate their workforce, taking them off of these time-intensive manual tasks and putting them on more productive ones. Or, in the instances where engineers and CNC machinists are having to stop what they’re doing to deburr and finish, those individuals can go back to their actual jobs and keep production going.
Automated deburring and finishing will be faster, more consistent and more reliable than manual work. And it will allow you to upskill and reskill employees who would otherwise be doing that work.
Upskilling is growing in popularity across manufacturing. Investing in automated tools, whether on your CNC machine or in your administrative office, allows you to pursue upskilling and reskilling in your facilities. A person who would otherwise be bogged down in deburring or with manual data entry in the office could learn new skills, gain certifications or even acquire degrees that elevate their responsibilities – and career – at your company.
Learn more: Upskilling to overcome the labor shortage in manufacturing. >>
A Clear ROI versus Manual Deburring and Finishing
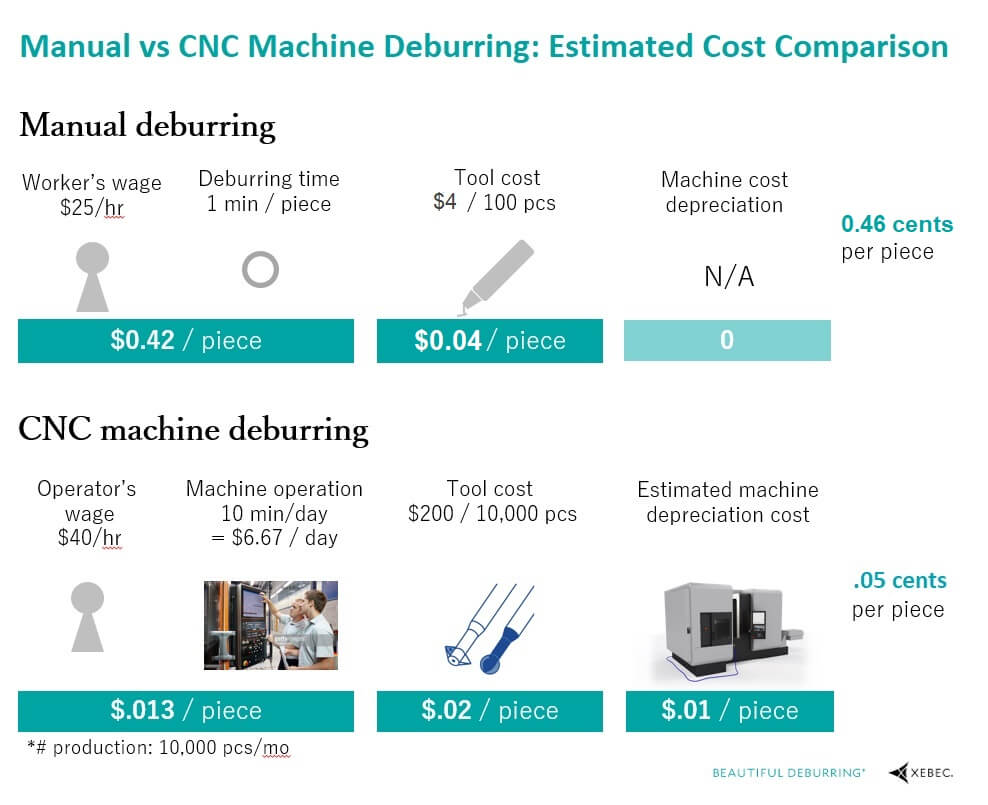
Manual deburring and finishing aren’t just inefficient and time-consuming, they’re more expensive than automated processes with Xebec products. They often require purchasing hundreds of disposable tools, absorb high labor costs and result in more wasted parts and rework. Then, there is the wear on your employees to account for and the potential cost of injuries.
And for aerospace manufacturers, scrapping the expensive materials used adds up quickly.
Xebec ceramic fiber brushes may have a higher upfront cost than a flap-wheel disk, but they have a long tool life, work faster without deforming and don’t leave a residue resulting in a consistent quality result with every part.
You save money with these tools – and you can capture new revenue opportunities with your improved processes, productivity and resource allocation.
Learn more: Calculate the ROI on automated deburring with Xebec. >>
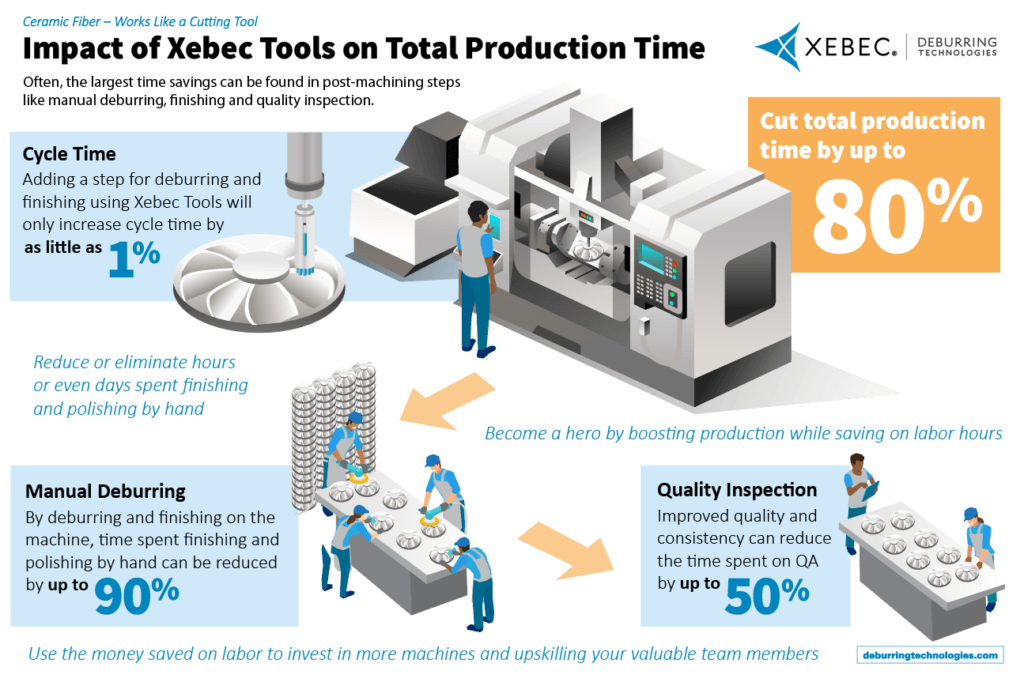
It’s time to reframe machine cycle time as a measure of efficiency. Innovative tools available today are creating new opportunities to optimize net production time, and some of those opportunities actually add seconds or minutes on the machine.
If you’re keeping a close eye on CNC machine time, your first instinct may be to nix anything that adds to it. But when it comes to automated deburring and finishing, those seconds or minutes given on the machine could save you hours and even days in post-machining processes.
In fact, some of the largest time savings can be found in post-machining steps like manual deburring, finishing and quality inspection (QA). Adding a minimal amount of time to the cycle time for automated deburring and finishing with Xebec can lower overall production time significantly.
A Future-Forward Investment that Supports Innovative Manufacturing
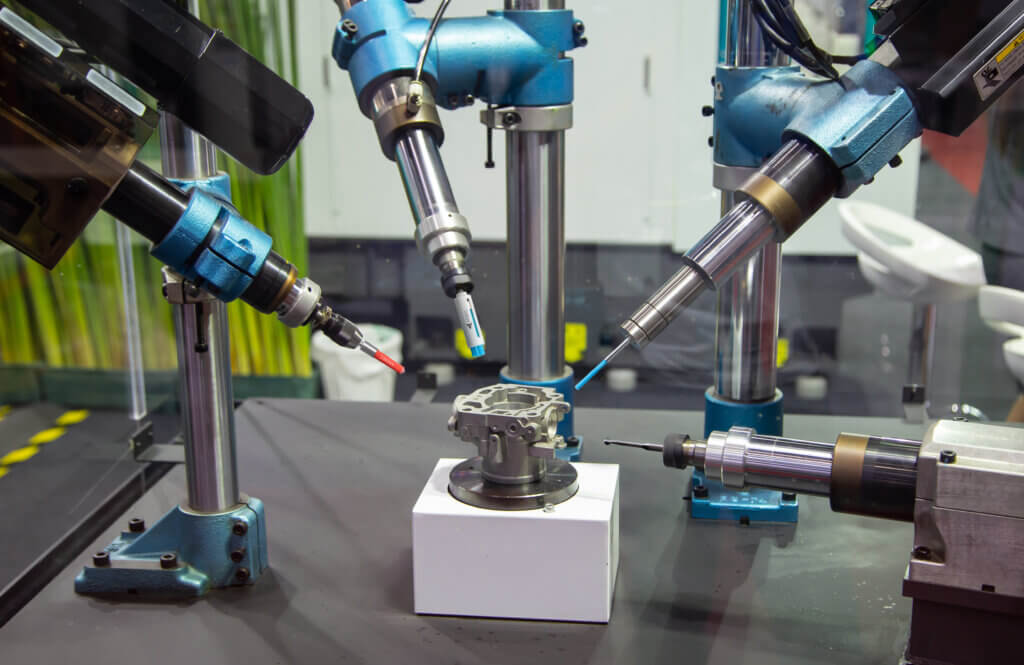
Finally, investing in automated deburring and finishing opens the door for aerospace manufacturers to stay on the cutting edge of manufacturing technology.
Robotics: Xebec tools can be used with robots, as well as CNC machines. Which is best for your deburring and finishing jobs?
Trending and emerging materials: Materials behave differently when they’re machined, and aerospace is witnessing the emergence of new alloys that are harder to machine. Xebec’s proprietary continuous ceramic fiber can help you stay productive against tougher metals.
Additive manufacturing: More aerospace manufacturers are using additive manufacturing for production and prototyping. Automated deburring and finishing can be the perfect process to follow additive manufacturing in aerospace.
Job costing for CNC machining centers: Accurate, consistent quotes directly affect profitability and often mean the difference between landing jobs and losing them. We provide an outline on the many components that go into job costing and discuss how you can improve accuracy.
Download our handy flyer on Xebec’s aerospace use cases.>>
Are you an aerospace manufacturer? Download our comprehensive eBook, Advanced Manufacturing Solutions for Aerospace Parts.
1 thought on “How Xebec Helps Aerospace Industry Manufacturers Reach New Heights”
What a well-written blog! It is a good idea to get aerospace mission-critical components manufactured by AS0100D certified and ITAR-registered company. They can help with torque transfers, test coupons, yaw shafts, housings and adapters. Ultra-precision parts and tools are a must to meet the rigorous standards of the aerospace industry.