Does the call for more sustainable manufacturing practices have you seeking ways to shrink your carbon footprint and waste output?
These efforts can benefit the environment today and in the future, but they also have benefits for manufacturing operations – and your bottom line, such as:
- Assessing operations to find fixable inefficiencies can lead to resource-saving process improvements.
- Investments in sustainable solutions often sets you up for more efficient operations that dramatically decrease overall costs and reduces required resources – immediately.
If you’re searching high and low for efficiency gains, don’t overlook your CNC machine operations. If your CNC operations end with an individual removing the part to deburr and finish it, this is a massive opportunity area for optimization via automation. And that optimization will have ripple effects beyond relieving that person of an arduous, and possible injury-inducing, task.
Once you start analyzing this process, you’ll see the wasteful red flags you could be avoiding. That’s especially if you do a side-by-side comparison of the resource consumption and waste output of your current process versus an automated process using Xebec deburring tools.
When you swap in an automated process with Xebec, you’ll realize:
- Reduced scrap, resulting in reduced material cost and machine time.
- Reduced number of tools required, often from multiple down to one.
- Reduced packaging, shipping and shelf storage required, resulting in more inventory space.
- Reduced waste of disposable tools and abrasive materials, many of which aren’t recyclable or degradable.
- And more.
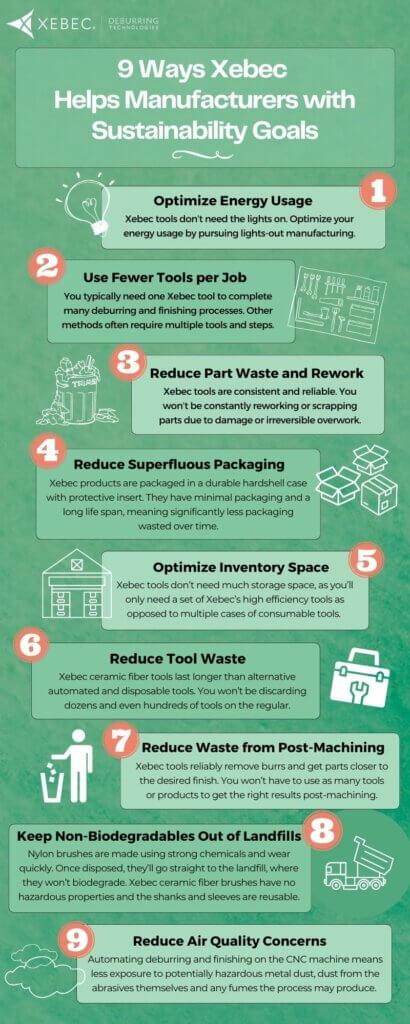
If you already automate deburring on your CNC using wire or nylon brushes, or another automated tool, Xebec tools still offer dramatic improvements. The continuous ceramic fiber of Xebec products achieves a level of quality and consistency that other materials simply can’t, as it means the brush performs more like a cutting tool. And Xebec products have a longer tool life, so you reduce waste and achieve a better ROI on your tool investment.
What Makes Xebec a Sustainable Manufacturing Option for Deburring and Finishing
Save Energy and More with Lights-Out Manufacturing
Xebec tools can “see in the dark.” They don’t need the lights on and they don’t take time off. You can rely on them for precision, durability and consistency. Automating deburring and finishing with these tools means you can reduce energy usage during operations, as well as save time and resources. And you can reallocate the labor time saved to other tasks or additional work.
Work toward lights-out manufacturing with done-in-one machining >>
2. Use Fewer Tools per Job
With Xebec, you typically need just one tool to complete many deburring and finishing processes. The tool deburrs and finishes at the same time and has a long tool life.
Hand-deburring often requires multiple tools and steps to fully remove burrs and achieve the desired finish. Those manual tools wear out quickly, becoming waste that is often unrecyclable, not made of natural products and doesn’t degrade for years. And with less durable automated deburring tools, you’ll still likely need multiple tools and steps to get the part through the full deburring and finishing processes. You’ll also go through those automated tools faster, resulting in continual tool waste.
3. Send Fewer Parts to the Dumpster (or Back for Rework)
Xebec tools generate less waste because the process is automated, consistent and reliable. You won’t be constantly scrapping parts due to damage or irreversible overwork, and you won’t have to send them back for rework due to inconsistency.
With manual deburring, the work is typically done at different times of day, with varying energy levels and by different employees. It also involves a lot of part handling. This leaves room for inconsistency from one part to another, as well as part damage during handling. With automated deburring using tools less durable than Xebec’s, consistency will be less reliable because the tools wear and deform easily as the part wears. And there’s often additional handling to finish off the part correctly post-machining that could result in damage.
4. Waste Less Superfluous Packaging
Xebec products are packaged in a durable hardshell case with protective insert and have very minimal packaging. They have a longer life span than other deburring tools, so you won’t have to replace them nearly as often as other less durable tools. Packaging may seem like a minimal contributor when it comes to waste and sustainability. But look back at the past month and consider how many abrasive pads and disposable tools you went through. Aside from disposing of the used tools themselves, how much packaging material waste was generated?
5. Make Optimal Use of Inventory Space (and Spend)
Xebec tools don’t need as much storage space as disposable manual tools, as you’ll only need a set of Xebec’s high efficiency tools for a process that would otherwise require multiple tools and steps. In most cases, you can store these tools in your CNC tool crib along with others for the machine.
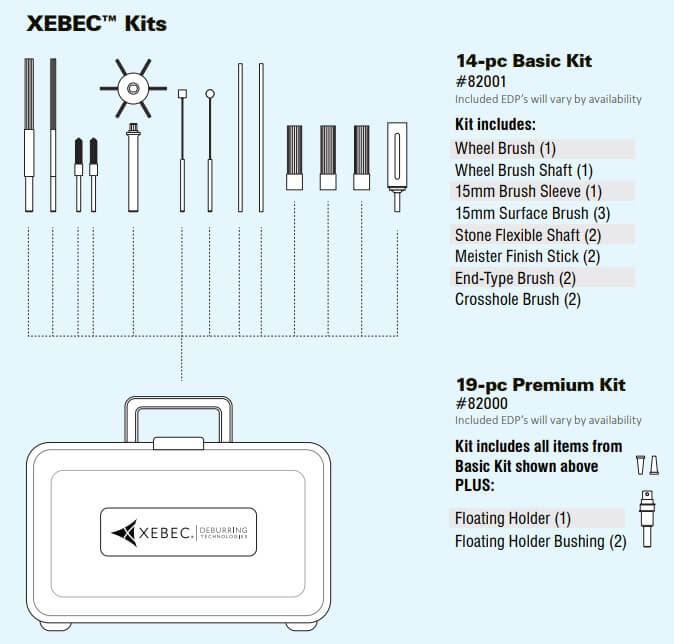
This means fewer inventory transactions and shipping and packaging costs to get those manual tools to your facility, and less inventory space taken up having them on-hand.
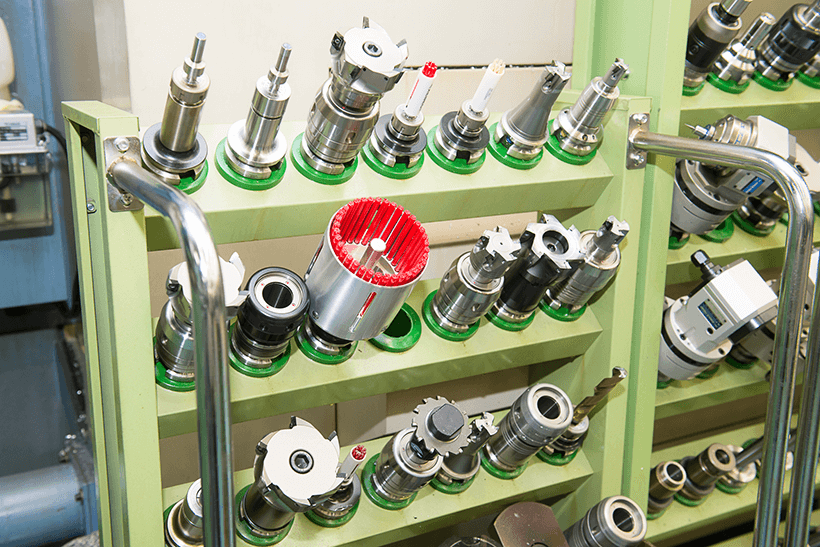
6. Get More Life Out of Each Tool
Xebec ceramic fiber tools last much longer than disposable alternatives like abrasives, nylon pads, flap discs, etc. They also last longer than alternative automated tools, such as wire and nylon brushes. You won’t find yourself discarding dozens and even hundreds of tools on the regular. But, when it is time to replace a worn brush, you are still reducing waste because the sleeves and shanks for the most popular Xebec Tools are reusable – saving you even more money.
7. Use Fewer Post-Machining Tools and Products.
Xebec tools reliably remove burrs and get parts closer to the desired finish than alternative automated tools. As a result, you won’t have to use as many tools or products to get the right results post-machining. For instance, many medical devices and parts require a mirror finish that calls for the use of diamond paste. With Xebec, you can get a higher-quality finish that reduces the time and amount of product you’ll need to get that mirror finish after machining.
>> Read about Xebec’s modern surface finishing and polishing operations in manufacturing
8. Keep Non-Biodegradables Out of Landfills
If you use nylon brushes in your automated process, you’re going to go through them faster – and they’ll go straight to the landfill, where they won’t biodegrade. The manufacture of nylon requires the use of strong chemicals, creating an unnatural material that doesn’t break down easily. Brushes made with abrasive nylon include wheel, cup, end, disc, mandrel-mounted, copper-center, radial coil and twisted-in-wire or tube-type brushes. Xebec ceramic fiber brushes have no hazardous properties.
9. Reduce Air Quality Concerns and Health Hazards
Automating deburring and finishing on the CNC machine means less exposure to potentially hazardous metal dust, dust from the abrasives themselves and any fumes the process may produce. A hand-deburring process releases various elements and dust into the air of your facility, affecting air quality and your employees.
For instance, flap discs produce aluminum oxide dust, which can be harmful and even lead to lung damage over time. And studies have shown a correlation between certain types of metal dust exposure and lung function deterioration. While there is equipment on the market to filter this dust and cleanse the air at your facility, containing the dust at the source is often the best route. Xebec ceramic fiber brushes do not contain any hazardous inhalant fibers.
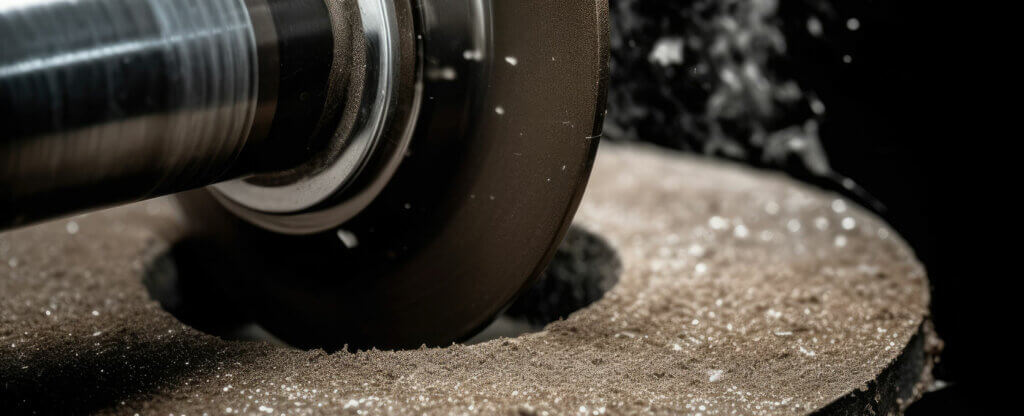
In Pursuit of More Sustainable Machining Processes?
If you’re ready to make an investment in Xebec products part of your sustainability plan in the coming years, get in touch with our team. Our application experts have experience implementing our tools in many varieties of operations. They can help you make the most of your investment, realize the maximum benefits and work toward your sustainability goals, both for the environment and for your own operations.