Automating deburring and finishing in your CNC machine, with a robotic arm or in another application can have noticeable – and even unexpected – benefits. That is, if you choose the right tools for your applications, use them properly and optimally, and take measures to preserve and maximize their expected life.
Sounds simple, right? Unfortunately, there are instances where manufacturers aren’t realizing the full potential of their advanced deburring tools due to underutilization, misuse or under-optimized processes. They’ve invested in a tool that can offer great returns, but they’re only receiving a fraction of those returns. Of course, if they knew the issue, they would fix the situation.
For instance, Xebec ceramic fiber brushes are top-tier deburring tools that stand to provide tremendous returns on investment (ROI). They have the longest tool life on the market, and their proprietary continuous ceramic fiber bristles have significant cutting and grinding power. They won’t deform, but they have flexibility to conform to part features. And the patented Xebec sleeve allows for the strength and consistency of a cutting tool. With Xebec, you can expect to be deburring high-quality parts with every run.
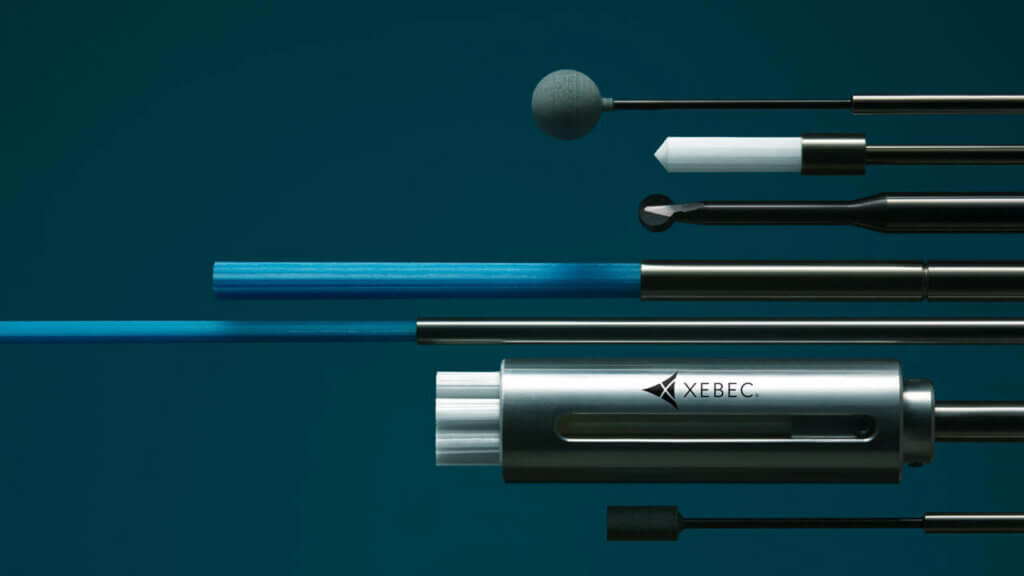
But for a manufacturer or machining center to realize the full potential of Xebec tools, they must use the tools correctly to maximize their tool life and performance. Our application experts work side-by-side with manufacturers to ensure success with our tools, making suggestions and offering expert guidance. With this critical support, we’ve seen manufacturers achieve optimal results and maximum returns.
Here, we’ve put together some information to help manufacturers choose the right brush for each job, apply it correctly and maximize its life. If you have purchased or are considering purchasing a Xebec product and are curious about optimizing your experience, getting input from an experienced Xebec rep is a great place to start. For more details and information, reach out to one of our knowledgeable representatives.
More than a Deburring Brush – a Cutting Tool
First things first: This is not your average brush. A Xebec brush performs more like a cutting tool, especially compared to alternatives like impregnated nylon brushes. Xebec brushes are made of proprietary ceramic fibers that have been manufactured into “bristles,” or rods, of different thickness.
The continuous ceramic fiber gives Xebec brushes 60 times more grinding power compared to nylon brushes. It also makes them more durable, long-lasting, efficient and consistent. They won’t deform, and they can work hard metals. You’ll get high-quality results and be able to perform high-precision work – faster and more reliably.
However, if you aren’t using the brush optimally and as intended, you’re likely selling yourself short on the full extent of benefits these advanced deburring tools can offer.
What Xebec Deburring Brushes are Really Made Of
Xebec brushes are easily automated and can deburr and edge finish, remove cutter marks and polish surfaces simultaneously. Manufacturers use them in processes involving CNC machining centers, robots, custom machines and drilling machines.
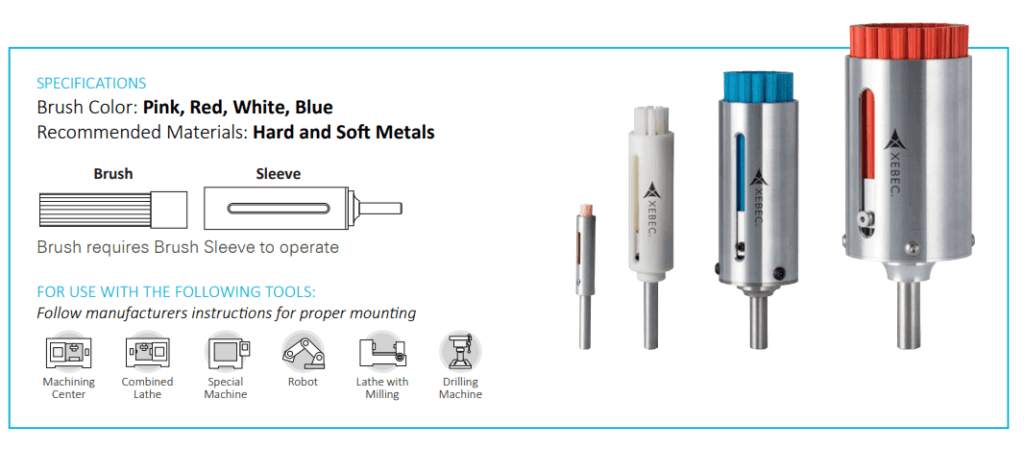
The brushes are available in a variety of sizes and colors to fit different manufacturing applications, processes and material conditions. Depending on the brush type, these brushes can work a broad spectrum of metal hardness from soft to hard. The color of a brush indicates its aggressiveness and grinding power:
- Pink: Pink is the least aggressive brush type and won’t change a part’s dimensions or features.
- Red: Red is the next-least aggressive brush and will conform to slight workpiece variations.
- White: White is a more aggressive brush that can run at high speeds.
- Blue: Blue is 3 to 4 times more aggressive than white.
Further, the ceramic fiber of these brushes really performs. It has a self-sharpening action on the cutting edge, and that continuous cutting edge provides consistent grinding performance. And unlike human operators, they never get tired.
Brush types include:
- Surface Brush – Ideal for simultaneously deburring & finishing edges.
- Extra Large Surface Brush – Ideal for minimizing cycle time by reducing number of passes.
- Crosshole Brush – Ideal for horizontal holes or deep parts.
- Wheel Type – Ideal for deburring & polishing of side surfaces and inner diameters.
- End Type Brush – Ideal for flat and curved surface by preventing undulation.
Selecting the Right Brush for Your Deburring and Finishing Work
With this variety of options available, it can be difficult to narrow down the right choice for your application. The top criteria to consider are:
- Target material: What material are you working with? Some brushes work best with softer materials, such as resins, plastics and aluminum alloys while others can handle hard materials like nickel, titanium, brass and steel.
- Target burr size: What burr root thickness are you working with? Different Xebec brushes can be applied to thicknesses from microfine to 0.008”.
- Target finish: What surface roughness spec do you need to meet? Choosing the right brush will get you there faster and more efficiently.
With these specs in mind, consider the following characteristics of potential brushes or combinations of brushes:
- Aggressiveness: Thicker bristles will have more aggressive cutting action. Do you need an aggressiveness at the level of pink brushes? Blue?
- Flexibility: Your brush needs to be able to conform to the workpiece you’re applying it to.
- Size: For optimal grinding power and efficiency, you need a brush that’s 1.5 to 2 times wider than the width of the workpiece surface. This way, the brush will engage the edge at 90 degrees, and the process will require fewer passes, minimizing cycle time.
Did we say “combination” of brushes? Yes, we did. There are many instances where a combination of brushes is the optimal choice for achieving the best results possible. In several cases, working from a less aggressive to a more aggressive brush results in the best, most impressive finish. This is a key area where Xebec experts help manufacturers select the best combination of brushes and sequence of use.
Right Brush(es) + Right Application = Optimal Results

Aerospace Engine Shell Nozzle: See how a Xebec Brush Surface Extra-Large deburrs and finishes the edges and large surface area of this aluminum alloy engine shell.
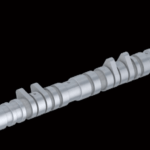
Camshaft: Watch the Xebec Back Burr Cutter and Path in action in this demonstration back deburring a ferrous casting ductile iron (FCD) camshaft, achieving uniform edge quality in shorter operating time than spring-type back deburring tools.
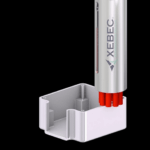
Automotive Control Box: Watch the Xebec Brush for Surface deburr the edge face after the milling process for an aluminum alloy control box, leaving no burrs behind and improving productivity. This as opposed to a wire brush, which left burrs and still required manual deburring.
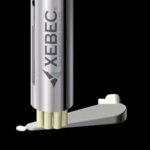
Artificial Hip Joint: See how a Xebec Brush for Surface fully automated polishing and enabled complete removal of cutter marks on a titanium alloy artificial hip joint. Notice the difference compared to manual processing, which left an uneven surface.
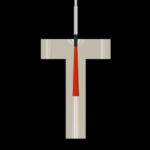
Mold Sprue Hole: See the process for using a Xebec Brush Crosshole to remove cutter marks and polish a mold sprue hole. Compared to a round bar grindstone applied manually, the Xebec tool improved efficiency because the brush fit to the tapered portion of the workpiece.
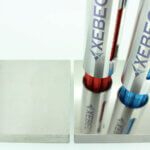
Alloy Tool Steel Mold: See how two Xebec Brushes for Surface polished a material surface of an SKD mold, improving surface roughness.
How to Use Xebec Brushes for Optimal Results
Replacing your existing deburring methods and processes with Xebec brushes won’t be one-to-one. Of course, with manual deburring and finishing that’s obvious. But it’s also true for wire and impregnated nylon brushes. Xebec’s one-of-a-kind brushes are more like cutting tools and it’s important to follow parameters for brush projection, workpiece engagement and other specs.
Brush Projection: The brush projection from the sleeve should be set according to the brush size you use. Below 0.2”, grinding power will increase and the finish may be affected.
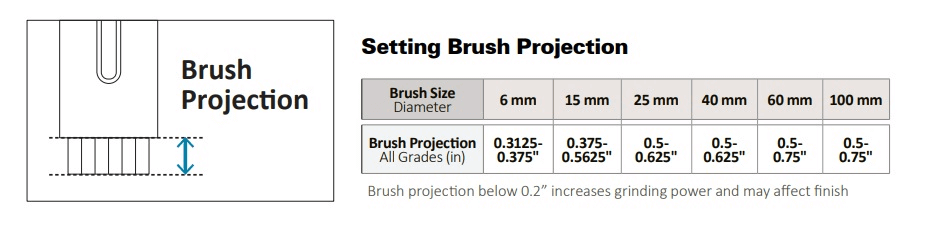
Workpiece Engagement: The workpiece setup and how brushes are engaged makes a difference. It’s critical to operate within the recommended range of maximum speed of rotation, depth of cut and feed rate. Pay close attention and take care with:
- Depth of cut
- Direction of feed
- Feed rate
- Rotational speed
- Rotational direction
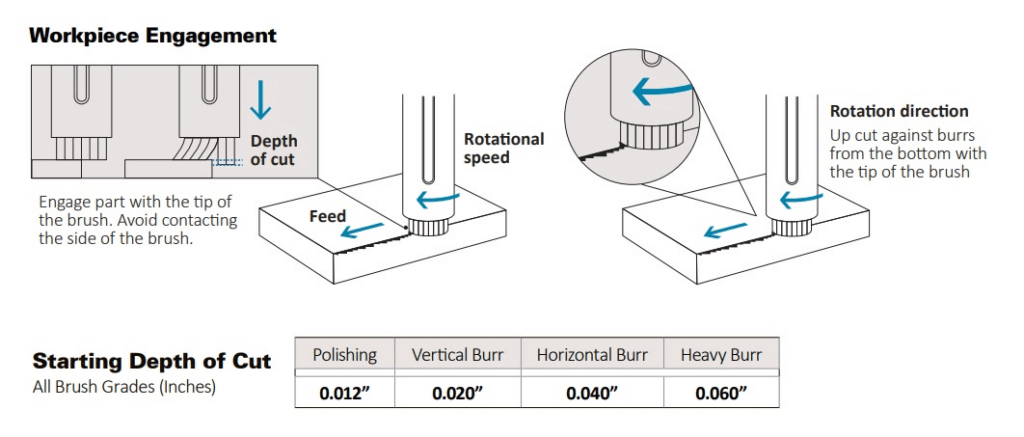
Expert Recommendation: Always perform a test run of your operation before you start. Run the test for one minute or more before starting, and for 3 minutes or more if you’ve changed a tool. Look for abnormalities, including excessive vibration or looseness in the mounting place of the tool.
Maximizing the Performance of Your Xebec Brushes
Xebec brushes are top performers – if you maximize that performance. Here are our tips for doing so:
Tips to Maximize Initial Deburring Operation
- Processing is the most effective using the tips of the ceramic fiber rod (not the sides).
- For the depth of cut, use 0.5mm to 1.0mm as a guideline, up to 1.5mm.
- Increase RPM up to the maximum allowed.
- Decrease feed rate in 10% increments.
- Do not change the original parameters but increase the number of passes.
- Try a more aggressive brush that will increase grinding power.
Adjustments for Improved Results
- Attaching the Xebec Brush to the Xebec Brush Sleeve allows the projection of ceramic fiber rods to be adjusted for fine tuning, flexibility and trackability. Longer projection increases trackability and flexibility, while shorter projection decreases it.
- Increase rotational speed in increments of 25%. Do not the exceed Maximum RPM.
- Increase the number of passes. Each pass will improve finish by approximately one half.
- Decrease feed rate in increments of 10 to 20%.
- Use a more aggressive color of brush.
Adjustments to Increase Grinding Power
- Decrease feed rate
- Increase rotational speed
- Increase depth of cut
Adjustments to Decrease Grinding Power
- Increase feed rate
- Decrease rotational speed
- Decrease depth of cut
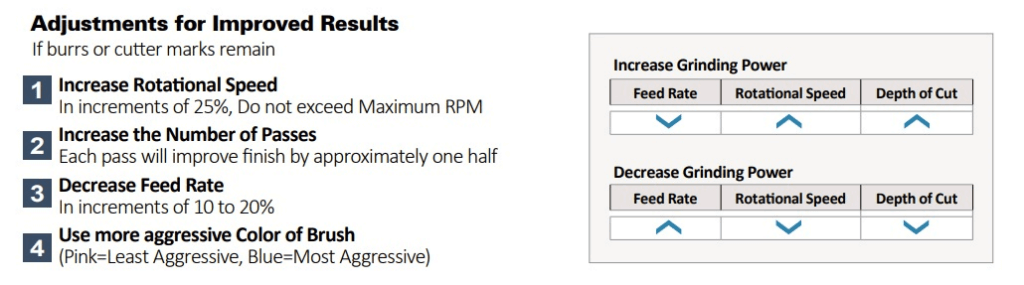
NOTE: Check out page 6 of our technical flyer for starting operating parameters for automated machining.
Maximizing the Tool Life of Your Xebec Brushes
When used properly, like a cutting tool, Xebec brushes have the longest tool life in the market. Here are our expert tips for ensuring longevity and getting the most out of your investment.
- Using coolants or oil will extend tool life and improve the surface finish.
- Usage under excessive depth of cut or grind load will shorten tool-life by pronounced wear and breakage of the fine ceramic fiber rods.
- Usage beyond the projection range of the brush beyond the sleeve may result in damage to the brush.
- If the brush deforms through usage, you can stick some polishing paper onto a board and gently rub onto the tip to adjust the form of the brush. You can do the same for the dressing as well.
- Use a dust collecting device to collect the dust produced during dry processing.
- When using on high precision processing equipment, the abrasive powder may adversely affect the sliding parts, so be sure to collect any dust and keep the equipment clean.
- Do not use the tool at an unreasonable angle or under excessive pressure.
- Securely install the brush into the chuck of the machine and confirm there is no clearance between the end face of the sleeve flange and the chuck. Incorrect installation could break the sleeve shank from abnormal stresses during processing.
Other ways to extend tool life:
- Decrease RPM in 10% increments
- Increase feed rate by 10% increments
- Try another brush color A13 Pink, A21 White, A11 Red, A32 Blue with the same parameters
And don’t forget to ensure operator safety:
Use protective gear: Always wear protective goggles, gloves and masks when operating the tool or entering the work area. Wear long sleeves, tight cuffs, and clothing to minimize skin exposure.
Take precautions: Be cautious in surrounding areas. Use of machines at high speed can cause flying debris within the work area. Dust or debris generated by operating process could be hazardous.
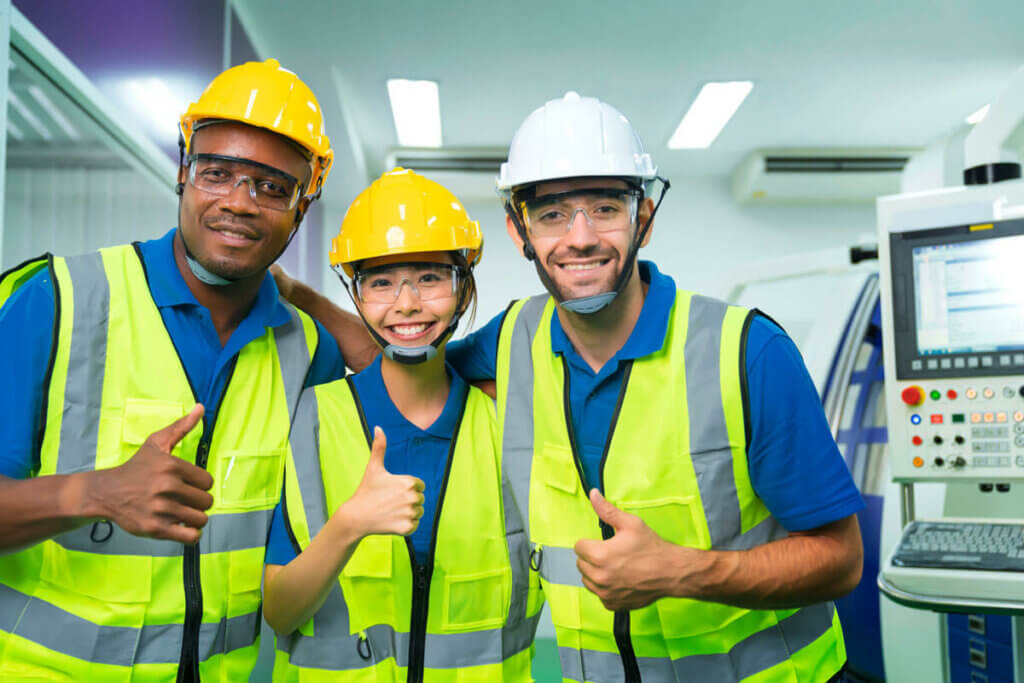
Using sophisticated automated deburring and finishing solutions by Xebec can help you save net production time, outperform competitors, deal with labor shortages, increase productivity and overcome many other manufacturing industry challenges. All of this is key to building resilience in manufacturing and embracing the future of the industry, no matter the current conditions.
To see what this solution can do for you, contact us to speak to one of our knowledgeable reps.
You’d be surprised how grateful manufacturing teams are after one of their own champions introduces Xebec products into their processes.
Ready to be your company’s hero?