If you’re a machinist, some of the most common terms you associate with thread burrs could be:
- Issue
- Problem
- Nightmare
- &*#@$%!
Fortunately, Xebec Deburring Technologies provides innovative deburring tools that easily resolve these problems, allowing you to get consistent quality results without labor-intensive work.
Threading makes a mess of burrs. They can form on almost any area of an internal or external thread, no matter the method you use. It’s critical to remove all burrs from these threads to ensure proper assembly or function of the end product. Threaded parts can be as low-risk as a watch screw and as high-risk as an aerospace component.
Learn more about burr types – so they’re less of a thorn in your side >>
Common threaded parts include fasteners (nuts, bolts, screws), pipe fittings and components that drive rotary motion. Often, these parts are used in consequential applications, from water and gas applications to medical devices.
It’s also in a machine shop’s best interest to make their thread deburring process effective and consistent, as thread deburring is one of the last steps in the process. Any errors could lead to scrapping the component – and all the labor and machine time it took to get the component to that point.
Xebec deburring tools are excellent solutions for deburring internal and external diameter threads. For example, the Xebec Surface Brush can automate thread deburring reliably and to quality standards, so the parts are ready to go right off the machine. Implementing Xebec brushes is one high-impact step you can take toward embracing the future of the CNC machining industry.
If you’re curious how our tools can improve your processes, start by having a conversation with one of our knowledgeable application experts.
How Most Shops Deburr Threaded Parts
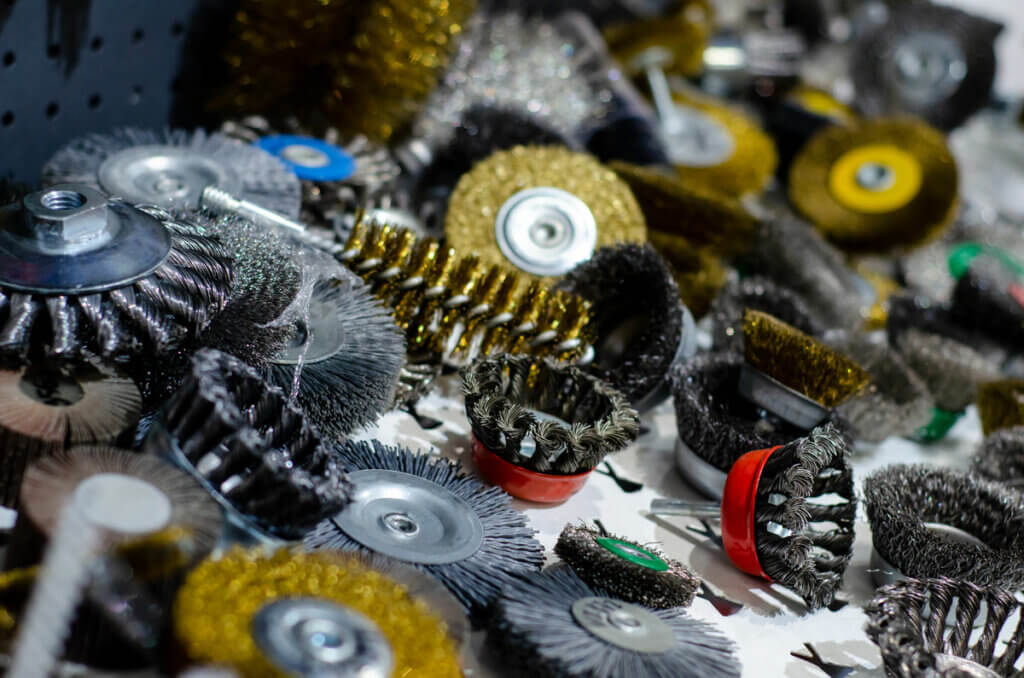
There are several options for deburring threaded parts, including manual processes, mass finishing and automated methods.
Manual Thread Burr Removal
Many shops manually deburr threads by using abrasive pads or sandpaper to twist down into the threads. Some use a fastener itself to deburr a thread, followed by an abrasive pad or sandpaper. We typically see this as a solution to deburring internal diameter threads in smaller holes, as there are few thread-shaped tools available on the market to serve this need.
Shops also use hand drills with brushes, such as twisted-in-brushes and wheel brushes, or radial discs. Such tools could be made of stainless steel, carbon steel, brass or nylon.
Such manual processes typically aren’t consistent or precise, and they’re very labor intensive.
See what manual deburring really costs you >>
Removing Thread Burrs with Mass Finishing Methods

Mass finishing methods include tumbling, thermal deburring and electrochemical polishing, and shops typically have to outsource such work, adding to job cost and timing. Outsourcing adds time, and these methods aren’t always the most efficient. For instance, burrs could simply get pushed into the thread instead of being removed, compromising assembly.
Automated Thread Deburring
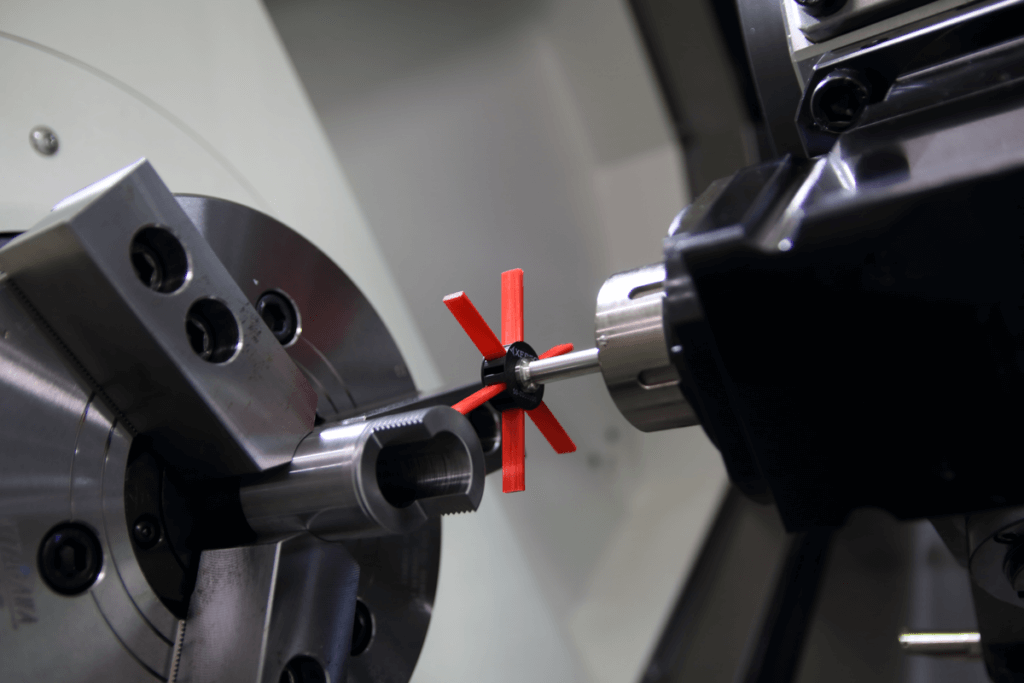
Shops can automate internal and external thread deburring on their CNC machines with specific deburring brushes, such as the Xebec Surface Brush and the Xebec Wheel Brush. Automating the process is more efficient and reliable, and it’s faster than manual and mass finishing methods.
Xebec Wheel Brushes and Xebec Surface Brushes can be used effectively in threaded applications.
The Xebec Wheel Brush is a top choice for deburring internal diameters, as well as deburring and polishing side surfaces.
The Xebec Surface Brush is also a top choice, as it’s incredibly versatile and performs like a cutting tool. It simultaneously handles cutter mark removal, deburring, surface finishing and edges. It offers precise and repeatable cutting tool performance. It can be used in thread deburring applications by turning the threads to the brush using the spindle holding the part, as opposed to rotating the brush itself. You can also use the surface brush as a cross-hole brush where there are threaded holes.
One area where the Surface Brush outperforms our Wheel Brush is in polishing between threads, as the threads can glide more easily between the Surface Brush’s bristles.
After using the Surface Brush to deburr the thread, no additional handling is required and it should easily pass inspection.

The Case to Upgrade to Xebec Thread Deburring Tools

Switch from manual or outsourced mass finishing processes to Xebec deburring brushes and you’ll not only save yourself the headache associated with thread burrs, but you’ll also save time and money, and cement your reputation as a high-quality producer of threaded parts.
Xebec products:
- Can be used to deburr and finish the part right on the CNC machine.
- Are ideal for precision and tight tolerances, meeting expectations and outperforming manual deburring by a landslide.
- Save time as they require less manual labor and less part handling, and they eliminate outsourced thread deburring.
- Allow you to reduce time spent checking specs, as you can do a spot check with a gauge and approve specs off the machine – and throw it in the box to ship.
- Are safer for shop employees, as they don’t have to handle parts with sharp edges to do manual deburring.
Xebec Deburring Technologies is a forward-thinking company. We’re always looking for new ways to use our tools and solve customers’ problems. Consult with us to find a way to streamline and improve your threaded part production.
Looking to make the case for modern deburring at your facility? We’ve got just the thing. Check out our new guide: