Fluid power and motion control are critical to the global economy in many ways. Companies across essential industries rely on fluid power as part of their business models and operations, such as energy, aerospace, agriculture, construction machinery, automotive, factory automation and more. Not to mention, this industry employs over 64,000 people, and those companies that rely on fluid power employ over 845,000 people (National Fluid Power Association).
Fluid power is an active part of the economic machine.
It’s also a consequential part. If hydraulic and pneumatic assemblies don’t operate sufficiently due to substandard components, the outcomes could be catastrophic.
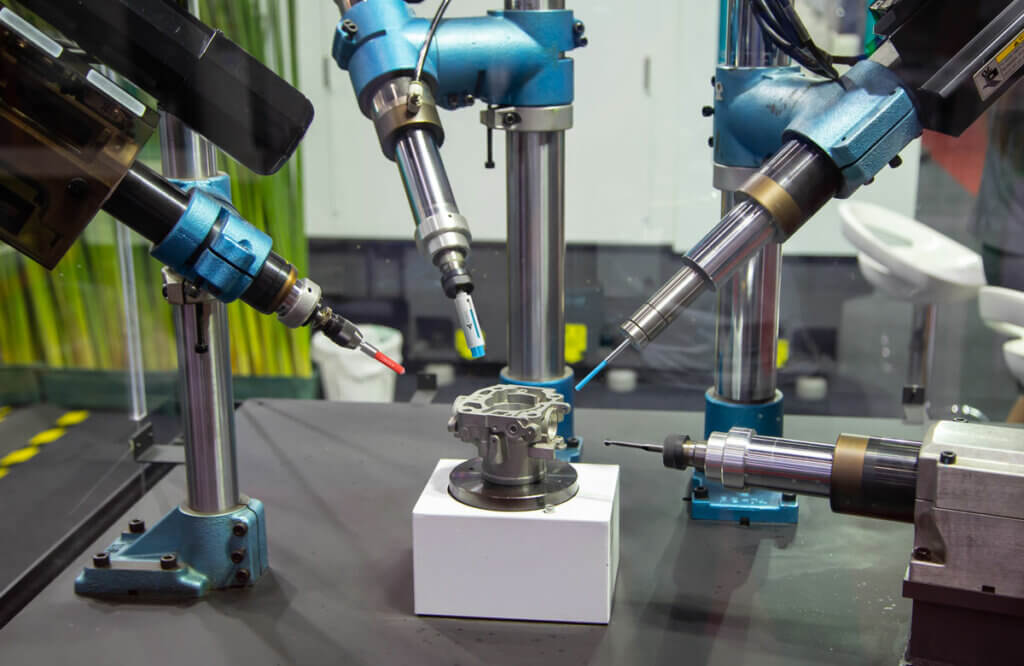
Ensuring proper performance and avoiding downstream catastrophes goes all the way back to the manufacturing phase. If a part isn’t produced to spec and makes it past quality inspection, a number of issues could occur. For example, burrs left behind on a part could come loose and cause damage to the assembly, and an inaccurate finish could mean components don’t seal securely, leading to leakage or contamination. Similarly, if an edge break isn’t to spec on an aerospace part, dire consequences can occur.
Consistent and reliable deburring and finishing on all assembly surfaces, holes, edges, and crossholes, such as with Xebec Deburring Technologies’ automated tools, help prevent such issues.
Why are Burr Removal and Surface Finishing Critical?
Fluid power involves the controlled movement of liquid or gas from one place to another to generate power, whether in a hydraulic or pneumatic application. Hydraulics typically use liquid and pneumatics gas.
Burr removal and surface finishing of metal components that go into fluid power assembly play a key role in ensuring optimal function and avoiding downstream catastrophes. A burr that comes loose in assembly could cause damage on its journey through a hydraulic or pneumatic system, and lead to major trouble down the line. If parts don’t mate and seal correctly due to an inaccurate surface finish, leaks and contamination could occur. And improper surface finishes can encourage corrosion and faster wear on parts.
According to a recent Fluid Power Journal article on the testing of fluid power seals:
“Testing revealed how exposure to various conditions impacts a seal’s performance and overall life. An example is the dynamic hardware’s surface finish impact on seal function and life. Testing confirms that all surface finish factors must be considered to ensure the best seal life and performance. Testing has quantified how both conditions (e.g. surface finish too rough or too smooth) impact the seal’s performance.”
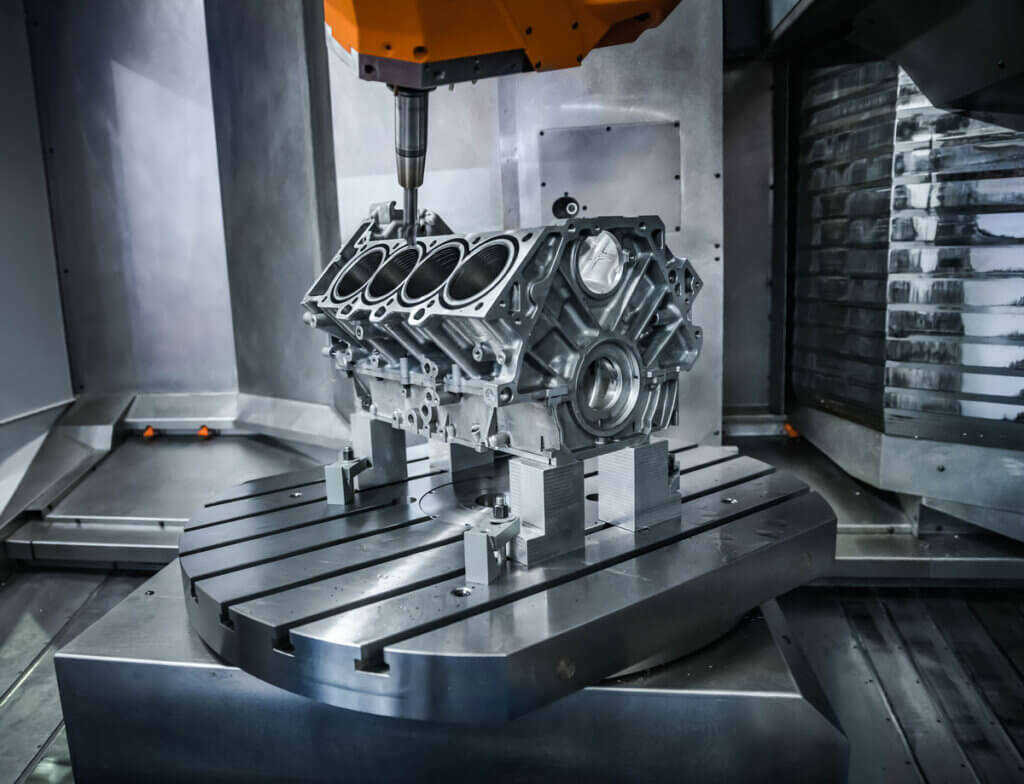
When a part leaves the plant, it needs to be ready to perform in the field as expected. These types of parts are meant to endure intense usage. Removing a part due to quality issues and damage is no easy feat in most cases, costing the end user in ways beyond the price of parts and repairs to significant downtime and stopped service.
Manufacturers who supply fluid power components benefit greatly from deburring and finishing processes they can rely on for quality and consistency. Performing them manually makes it difficult to maintain consistency. One employee feeling overtired and undercaffeinated could miss something or deburr incorrectly, resulting in a scrapped part – or worse, a part that makes it through to the customer.
Automating these processes with quality tools, such as Xebec ceramic fiber brushes, will make your outcomes repeatable and controllable.
Fluid Power Components Compatible with Automated Deburring
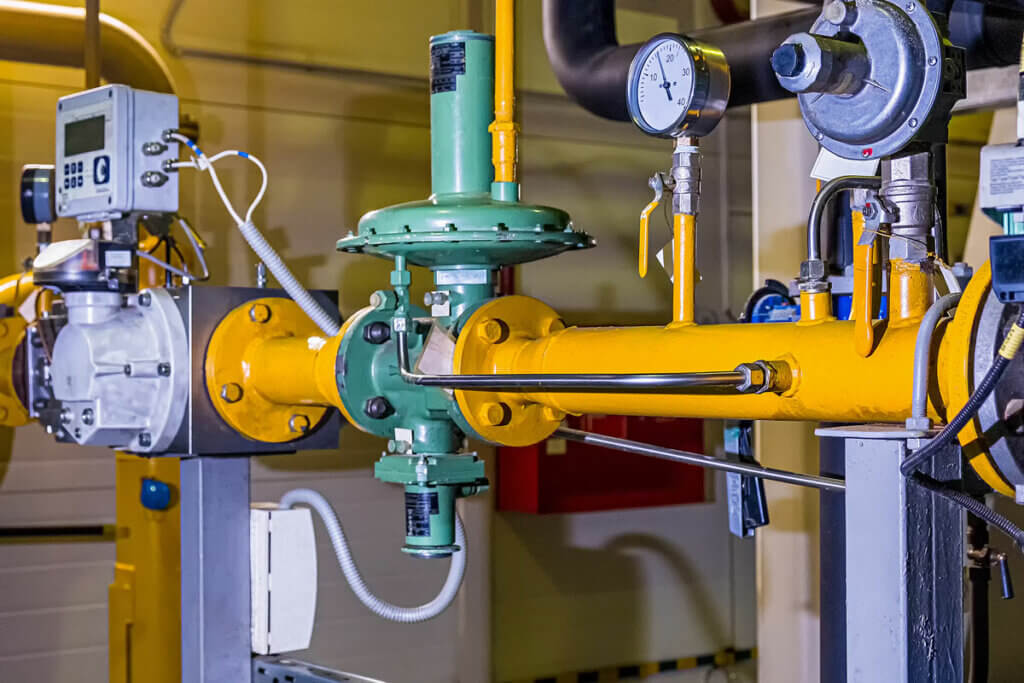
Xebec deburring tools work expertly with components that handle flow-through, such as air, oil, gas, water, etc. We are often presented with pipe valves and fittings, and our products work exceptionally well with valve bodies, pumps and motors. We understand the critical nature of removing burrs and getting the right finish to avoid problems with the assembly and downstream.
The list of components used for fluid power applications is long, and includes:
- Cylinders
- Engine blocks
- Gears
- Housings
- Impellers
- Manifolds
- Pipes
- Pumps
- Piston rings
- Valves
Here are just a few examples of Xebec deburring and finishing applications with fluid power components:
A Xebec Stone Flexible Shaft Type was used to crosshole (blind hole) deburr a hydraulic valve after the drilling process. The former process had involved a rubber wheel and carbide rotary bar on a rotating tool. That process resulted in damage to the shape of the edge and secondary burrs. The Xebec Stone Flexible Shaft allows soft contact with the workpiece as the shaft flexes and will remove burrs while maintaining the shape and dimensional integrity of the edge.
The Xebec Back Burr Cutter and Path was used for deburring the inside and outside edges of the mounting holes with chamfered edges.
An Extra-Large Xebec Surface Brush was used in a surface finishing application for a main hydroelectric shaft. The tool finished the edges and a large surface area.
Cylinder Head Oil Gallery (Crosshole)
A Xebec Extra-long Crosshole brush was used to improve the crosshole deburring and internal polishing of the oil gallery of a cylinder head done by nylon brushes. The Xebec solution ensured the removal of all burrs and cutter marks on the inner diameter.
A Xebec Wheel Brush was used to both deburr and finish surfaces for a threaded compressor fitting. The wheel brush deburred and finished the outer diameter of threads and inner diameter.
A Xebec Surface Brush was applied for the surface deburring and finishing of a valve plate. The tool deburred and finished the edges, achieving a fine surface finishing of detailed parts.
A Xebec Crosshole brush was used on a stainless steel pipe fitting for crosshole deburring and internal polishing after the drilling process (removing cutter marks) in one process with no secondary burrs generated.
Consequences of Compromised Hydraulic and Pneumatic Components in the Field

What issues could arise from a poorly deburred or improperly finished part going into an assembly?
Corrosion: Both unwanted burrs and poor finishing can lead to corrosion of a part. Any burrs left behind could cause friction in the assembly or come loose, score other parts and damage other critical components. A poor finish could also lead to friction where assembled, or it could mean the surface is exposed and unable to withstand corrosion. Corrosion can cause performance failure.
Damage and Wear: The same concerns above will mean a part wears faster than it should due to friction and damage. And a burr that comes loose could wreak havoc along its travels through an assembly.
Leakage: When these issues occur around a seal, they compromise that seal and lead to leakage, whether internal or external, which could be catastrophic when used with highly combustible fuels.
Contamination: Similarly, when seals aren’t properly seated or wear out, outside elements can contaminate the fluid element that moves through an assembly. There is also built-in contamination, where scores and damage inside an assembly lead to internal leakage that compromises the fluid and the assembly (learn more about the cost of contamination in Fluid Power Journal). This type of contamination is common in hydraulic pump systems. Failure due to such contamination could be also disastrous.
Electrical hazard: In some cases, friction with a sharp enough burr can spark a fire or explosion depending on the fluid involved.
What happens after the failure of an assembly? The following examples aren’t for the faint of heart, but if you’re in the industry, you’re surely aware of such potential consequences.
According to Power & Motion, “Having a hydraulic line become severed may result in dire consequences from the jet of hot oil that can spew from the end of an unrestrained hose. Even if serious injuries or equipment damage doesn’t result, cleanup costs can be substantial.”
In another Power & Motion article, the author explores a safety scenario in which a hypothetical maintenance worker is standing on a stepladder to tighten a leaking hydraulic connector, and “the connector unexpectedly failed. High-pressure hydraulic oil burst from the broken connector, striking him in the face and chest.”
Produce Consistent Quality Fluid Power Parts with Xebec
Xebec deburring and finishing tools give manufacturers and job shops the performance and reliability they need to serve such an important industry. The ceramic fiber acts more like a cutting tool, as it doesn’t deform as it works and has superior grinding power. You’ll be able to deburr and finish parts more consistently – and faster and more cost-effectively – with these tools automated in your CNC machine or a robot. Your customers will be able to depend on you to help them prevent catastrophic failures and disasters down the line.
Reach out to learn more and start a conversation about your deburring and finishing operations.