Manufacturers with CNC facilities and machine shops have faced several challenges over the last decade, and many decision-makers have been burned by new software, vendors and processes. Additionally, CNC (computer numerical control) machining demands expensive equipment and software, as well as skilled machinists.
Despite lingering hesitancy, manufacturers and CNC machine shops are tasked with a big decision — increase efficiencies or put their operations at risk.
5 Most Common Challenges Faced by CNC Machining Companies
Be the hero your company needs to overcome these obstacles and gain a competitive edge. Let’s dive into the most common concerns these organizations face regularly. Then, we’ll offer actionable advice on solving them using automated deburring and finishing technology.
CNC Precision and Accuracy
CNC machining departments and machining services are tasked with consistently producing parts that require high precision and accuracy while achieving tight tolerances, specific finishes, unique patterns and complex geometries. To do this, close attention to detail is non-negotiable.
Material Limitations and Compatibility
Different materials have different properties and attributes, and the choice of material impacts the specialized tooling and cutting techniques required. Manufacturers must carefully select the tools and processes that match the material needs and limitations.
High Cost of Equipment and Software
CNC machines can cost anywhere from $200k and up, with some options costing nearly half a million dollars. High equipment costs and expensive software to run these specialized machines can create a substantial burden, especially for smaller enterprises. These costs coupled with those associated with software updates and training requirements for qualified operators and programmers, and the total investment can be overwhelming.
With the high cost of equipment, manufacturers need to pay close attention to both direct and indirect costs to remain profitable. These include:
- Complexity of parts
- Number of parts
- Material used
- Labor and labor overhead
- Tools and equipment
- Machine time
- Deburring process
- Surface finishing
- QA inspections
- Special handling costs
- Transportation and logistics
- General overhead
Skilled Labor Requirements
Skilled CNC machinists are essential to the manufacturing process. They prepare test runs and ensure optimum machine performance, as well as inspect and measure finished products for quality assurance. However, finding and retaining qualified talent has been challenging, given the skilled labor shortage.
High Cost of Market Entry
Due to the high price tags associated with expensive equipment, software and labor, the cost of entry for companies entering the CNC machining industry is a significant obstacle. An obstacle many organizations struggle to overcome. What’s more, the way to deal with changing industry trends is through innovation, automation and sustainability, both for operations and employees — an area where some manufacturers lag.
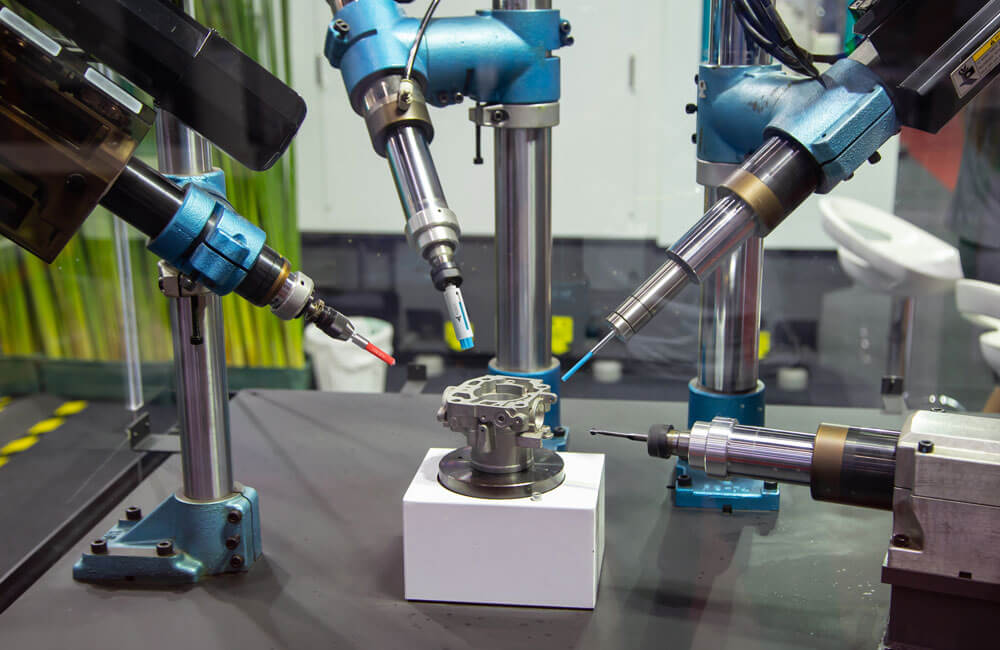
How Xebec Can Help Overcome CNC Machining Center Challenges
Innovative deburring and finishing technology is pivotal in helping CNC machine shops address several of these challenges. Automating the removal of burrs (tiny imperfections and rough edges formed during machining processes) and finishing the piece with Xebec tools ensures the components meet stringent quality standards without the need for extensive manual labor.
The CNC industry has made significant progress towards implementing advanced technology such as automation and robotics. However, the increasing complexity and demand of machined parts have left consistency and quality gaps that prevent manufacturers from getting ahead.
Xebec ceramic fiber brushes fill those gaps.
Why Xebec?
Since the 1990s, we’ve developed deburring technology that outperforms the competition with innovative ceramic brushes with no filler materials that clog or degrade your part manufacturing process. No product on the market can more effectively deburr your parts (and finish them in the same step) while preserving the dimensional characteristics of the workpiece. Our proprietary cutting fiber is the world’s only brush made of continuous ceramic fiber that offers the following:
- Unsurpassed grinding performance
- Consistent cutting performance
- No deformation
We don’t just sell quality deburring tools like surface deburring, crosshole deburring and detailed finishing tools; we take it a step further. Our technical personnel assist you in selecting the proper tools and operating parameters to help you achieve optimum success.
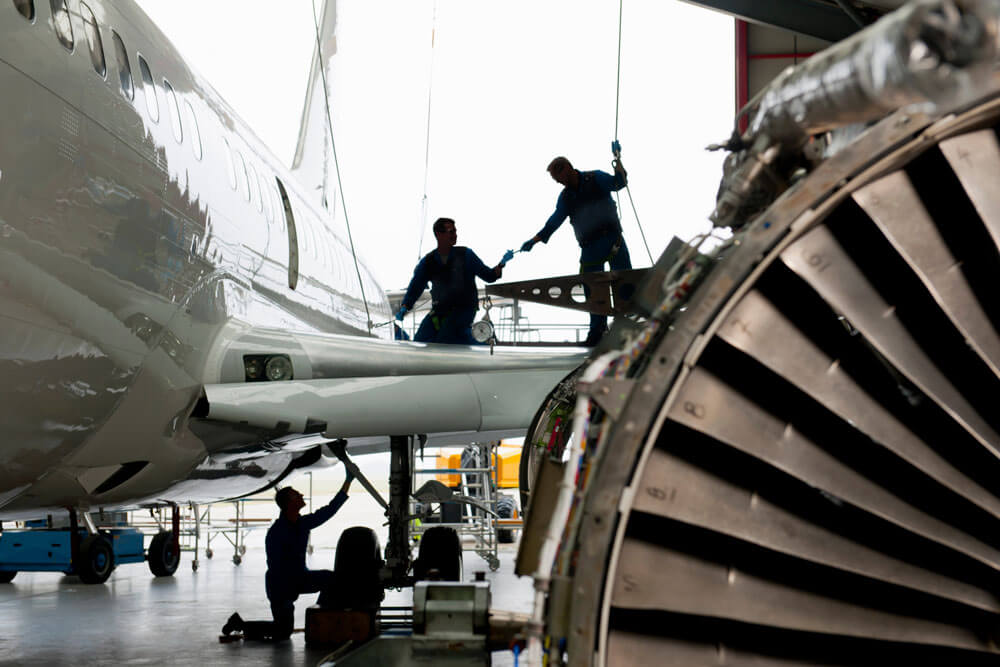
Surface Finish Precision and Accuracy
For parts that require high precision, set your sights on surface finishing. Modern Xebec Deburring Solutions can help you ensure a consistent and accurate Ra and finish every time.
Concerned about meeting surface finish specifications like lay, surface roughness or waviness requirements?
When you use Xebec, in many cases, you can reach the appropriate surface finish without a costly post-machining process like polishing. Not only do you save money by cutting this second phase, but you have more consistency, quality and reliability. Moreover, it’s significantly more efficient and accurate than a manual process.
Due to their high precision, Xebec deburring tools are effective for the manufacturing of aerospace and defense components, as well as other communications and exploration-related industries.
Learn how to improve manufacturing of complex parts with strict requirements, read Surface Finishing for Aerospace, Defense and More.
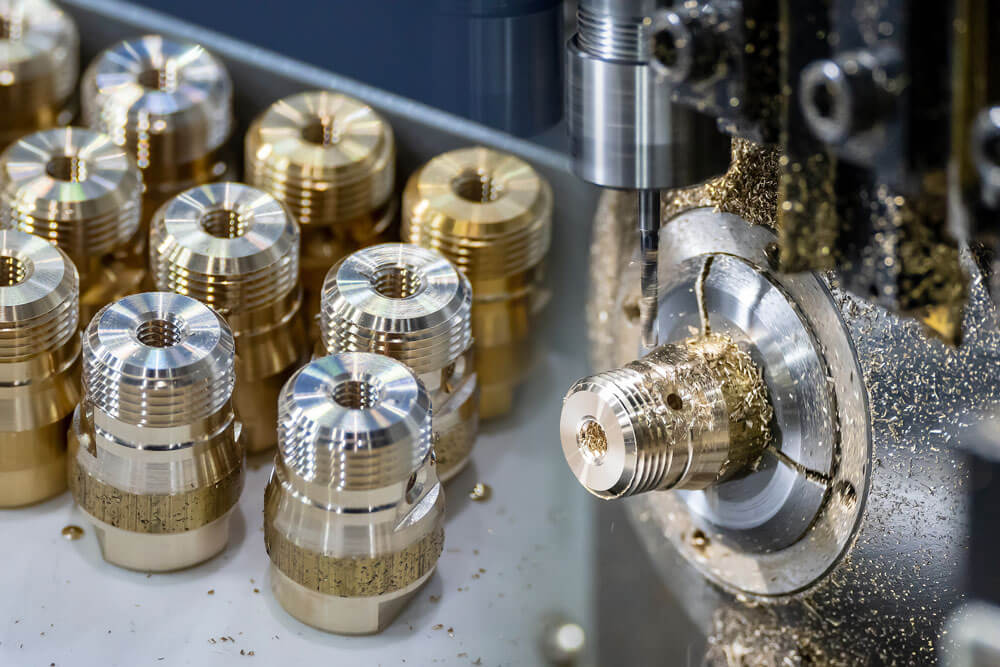
Material Limitations and Compatibility
Automated deburring technology can alleviate the challenges faced by manufacturers.
Burrs form on a variety of different substrates, including metals and plastics when milled, cut, drilled or otherwise machined. If burrs are not removed from a piece, it can lead to trouble down the road, including:
- Assembly issues
- Inadequate or unsafe performance
- Burrs that break off during operation or use
- Risk of operator injury
Some materials are more prone to producing burrs. The composition and characteristics of a material such as hardness, ductility and quantity of parts, should be considered when considering deburring methods. Plus, many other deburring and finishing solutions deform quickly when used on hard materials, unlike Xebec brushes.
Xebec’s automated deburring and finishing tools produce excellent results in a wide variety of applications and on a broad range of workpiece materials. Additionally, Xebec brushes are backed with expert advice and tailored solutions for deburring and finishing almost any material.
For a list of burr-generating materials, read Deburring Different Materials: Metal, Plastic and Beyond.
High Cost of Equipment and Software
Ensure you’re accurately calculating the cost of your CNC jobs. With operational improvements, you can reduce job costs and stay competitive.
Do you see your CNC operators stopping production to deburr or finish parts? Are you seeing increases in returned parts? Increased injury rates among your team due to fatigue and stress?
Automating processes in your CNC machining center, such as deburring and finishing, will reduce labor output and costs, overhead expenses, QA time, and scrap and rework. Our Xebec ceramic fiber brushes offer benefits like:
- Performs like cutting tools
- Consistent performance
- Deburr and finish in one step
- Achieve a finely finished surface
- Do not deform after repeated use
- Have incredible grinding power
Plus, we can help you program your back burr cutter path for optimum efficiency and quality.
Additional measures to improve process efficiency and better manage your resources include changing part material (if possible and reliable), improving CNC machine capabilities and optimizing processing conditions and production.
Get tips for more accurate job costing, read Job Costing for CNC Machining Centers: Challenges and Opportunities.
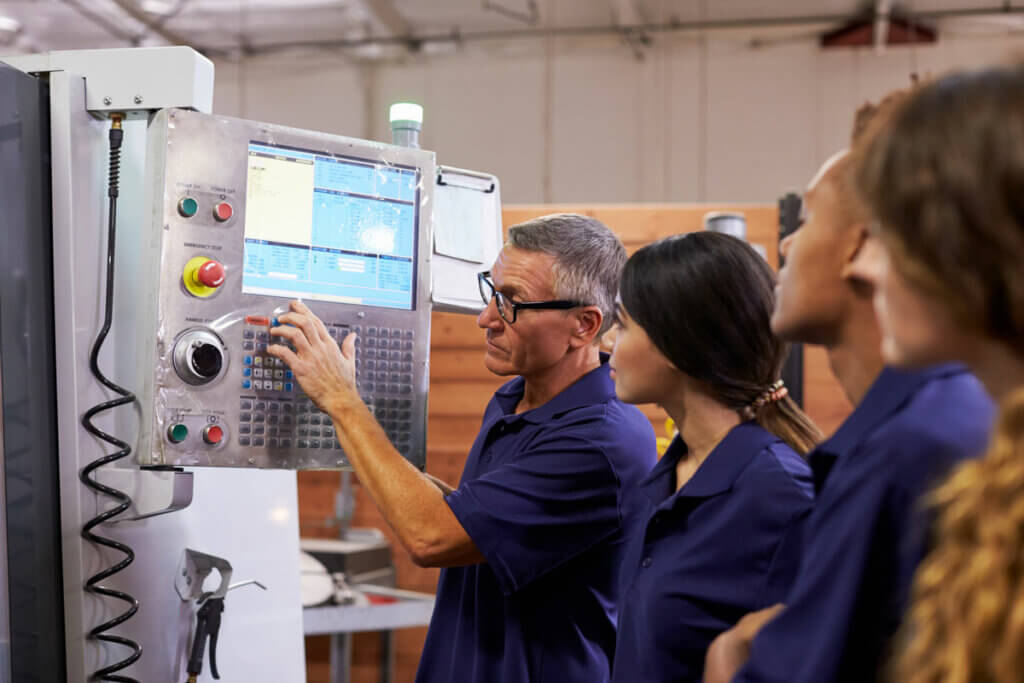
Skilled Labor Requirements
The Fourth Industrial Revolution is dramatically changing the way we work. Advanced technologies, artificial intelligence, advanced robotics, cognitive automation, advanced analytics, and the Internet of Things (IoT) have created a mismatch between available workers and skills needed for open positions.
In fact, Deloitte and the Manufacturing Institute say the labor shortage in manufacturing will reach the highest levels ever recorded.
How can the manufacturing industry prepare for the future, prepare its workforce with the skills needed and make manufacturing more attractive to qualified talent?
One way is through technology. Manual deburring and finishing are tedious and time-consuming tasks. A few things happen when you automate the process with Xebec deburring and finishing one-step solutions. First, you can fill in where labor is short. Second, you can reallocate employees and train them on new skills and profit-generating tasks. Third, you can increase production capacity and throughput while ensuring consistency and quality. And fourth, removing the manual elements of the job increases worker safety and job satisfaction.
Automation isn’t about replacing people. It’s about enhancing capabilities and bridging the skills gap.
Alleviate talent shortages in your business, read 3 Ways to Get Rid of Production Headaches with Automated Deburring and Finishing.
Market Entry
Is manufacturing slowing down, or is it making a comeback? Depending on the source, you’ll find wildly different answers. Regardless, there is one single truth we can all agree on. The need for resiliency has never been more critical than now.
With soaring costs and limited cash flow, manufacturers looking to thrive need to thoroughly evaluate their businesses and identify risks, opportunities and critical issues. Deloitte suggests investing in process-related innovations that optimize production output, inventory and overall costs.
Manufacturers and CNC machine shops can reduce costs, improve operational efficiency and help businesses effectively compete by modernizing their deburring and finishing processes. By using automated deburring tools from Xebec to optimize processes, manufacturers can:
- Increase production output
- Achieve more consistent results
- Improve liquidity
- Respond more effectively to market conditions
- Reduce waste
- Prioritize employee experience
As Deloitte states, “Such process innovations could go a long way in helping manufacturers produce more with less, in turn enhancing efficiency and productivity of their assets and employees.”
We’re already working with companies at the forefront of technology. Read Trends to Embrace and Where We’re Going in the Future of CNC Machining
Calculating ROI
Seeing the value of innovation but need help making the case for modern deburring in your operation? We can help break it down.
The true cost of manual deburring isn’t just about the cost of tools and labor. It’s essential to consider the unexpected steps that occur after production starts. Costs not included in the job quote may consist of extra deburring, unexpected finishing, expensive scrap and parts returned due to burrs.
To calculate the true cost of manual deburring, we need to understand the three core costs — fixed and variable. They include:
- Labor costs: Calculated using the hourly rate of a worker’s salary (plus benefits) and their part production time.
- Tools costs: Calculated by dividing the cost of the tool by the tool life.
- Machine equipment cost (CNC time): Calculated by dividing the hourly machine depreciation cost by the quantity of tools consumed and by pieces produced.
Now that we understand these core costs, let’s calculate the manual cost per piece versus using automated modern deburring. This graphic demonstrates the significant time and money savings to be gained by using automated deburring and finishing brushes by Xebec:
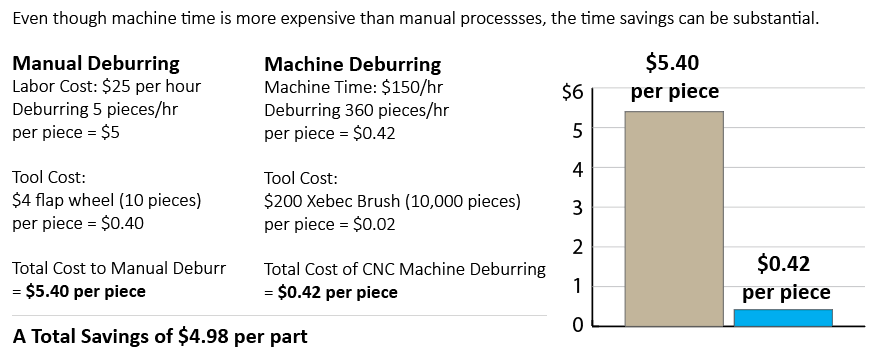
Of course, many other indirect and situational factors affect production costs. We recommend evaluating your current processes to create a baseline of current operational costs and then compare costs against those of Xebec deburring solutions.
For more insights on calculating the costs of deburring, read How to Calculate the ROI on Automated Deburring with Xebec.
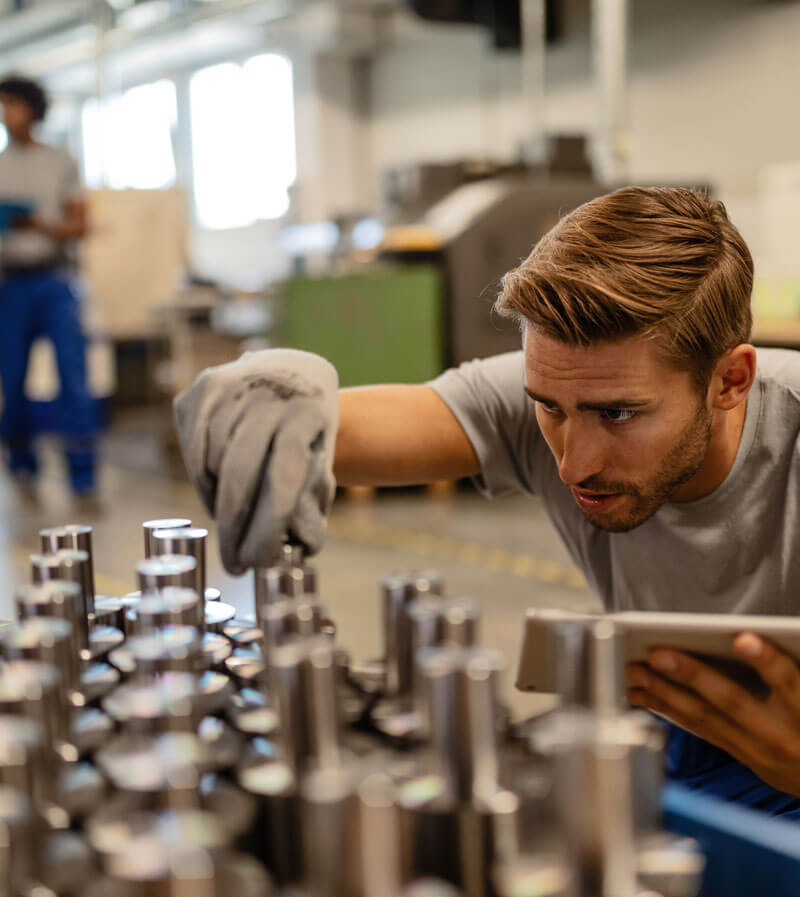
Be a hero for your company and make the case for modern deburring.
Xebec automated deburring and finishing tools clear the way for manufacturers — streamlining the finishing process, while addressing quality and efficiency issues.
Let this be your guide as you develop your pitch for your executive leadership. Once you’ve got their attention, reach out to our application experts to help design the most appropriate, efficient solution for your operations.
When factoring in all the variables associated with your deburring process, the time savings and quality improvements gained by automating with a Xebec solution is a no-brainer investment.
Contact one of our Application Specialists at (800) 434-9775 or online to see how we can improve your total deburring costs and achieve ROI by designing a deburring and finishing solution for your company.