Done-in-One Machining at Your Facility: Can It be Done?
Done-in-one machining isn’t a new concept. But it’s also not the most common means of production, especially for smaller operations. However, if you were to adjust your processes so that all steps in the machining process are performed without having to remove a piece from a machine, it would have considerable benefits. At Xebec Deburring Technologies, we’ve been helping manufacturers work toward this goal for years by designing and integrating automated deburring and finishing into their machining processes.
Today, with the challenges the manufacturing industry is facing – and is projected to continue to face – a turnkey solution looks quite appealing. It affects everything from the bottom line to labor along the production line. It can also help manufacturers achieve lights-out CNC machining and lean manufacturing. If purchasing new CNC machines is part of your strategy and budget this year, there are new options on the market that integrate processes such as welding and 3D printing. However, in most cases, you can do more with the machines you already have. And even if you’re unable to reach a fully done-in-one process, getting a step closer by automating deburring and finishing with Xebec deburring brushes for CNC machines improves efficiency and your bottom line.
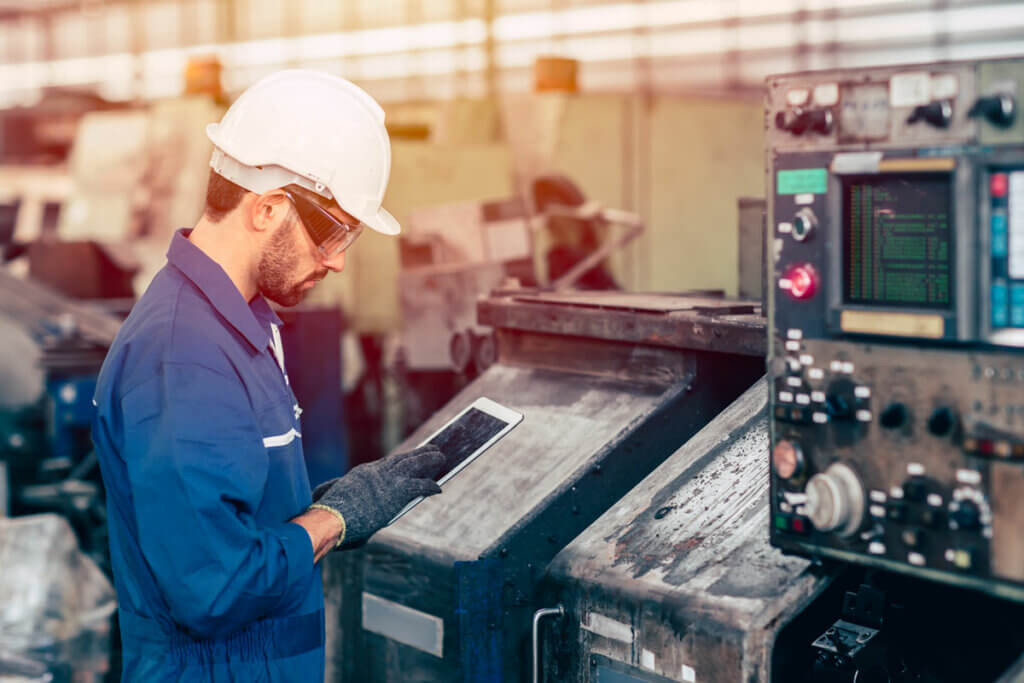
How does done-in-one machining work?
With done-in-one machining, you have a few options for process. You could design around robotic CNC loading, positioning a robot in the center of a multi-machine operation to move the piece from machine to machine. Or you could make your CNCs done-in-one machines, programming production such that everything happens on the same machine without part handling or manipulation. In either scenario, you dramatically reduce touches, which translates to a reduced likelihood of errors and damage.
For instance, if you run a large milling cycle that requires moving the piece to a different station to be deburred, you can integrate automated CNC deburring tools on the machine instead, such as the Xebec Surface Brush. This keeps the part on the machine, saving on net production time. This can be designed following some of your already-programmed paths.
To help you in your decision-making around this opportunity, we put together some common questions and our answers. Our team has experience helping customers design more efficient processes and accomplish done-in-one machining with our automated deburring tools as a component. If customers can’t accomplish done-in-one operations, our tools help them get that one step closer.
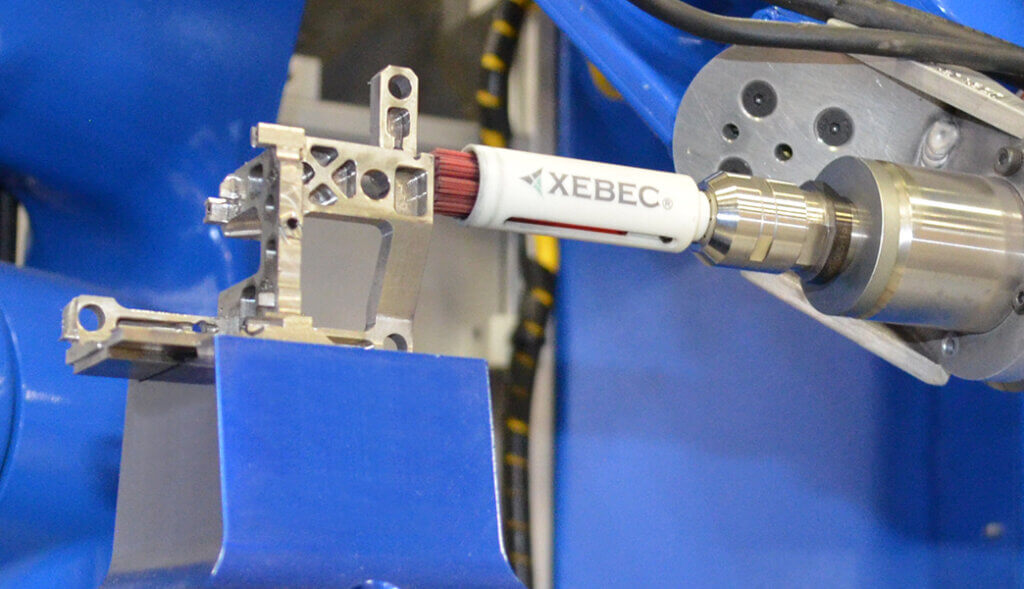
Do I need multi-tasking CNC machines to perform done-in-one machining?
You don’t necessarily need multi-tasking machines to move toward a done-in-one process. You simply may need additional axes. If you have enough room in your tool changer to add a deburring brush, whether it’s a magazine or carousel, you can typically automate deburring and finishing on the machine. Our tools run on the spindle and they deburr and finish at once, accomplishing both tasks without needing two tools.
If I didn’t plan for done-in-one machining, can my existing machines still accomplish it?
In most cases, you can make your existing machines perform done-in-one work. For example, you can easily move your deburring and finishing processes onto the machine even if that wasn’t your original intention.
Operations that involve hand-deburring are becoming less cost- and time-efficient, and many industry professionals are seeking ways to save in that area. Automating this work isn’t as complex as it may seem. Our tools load right into your spindle. Our experts work with engineers and machinists to integrate our tools into the process, so you’re set up for successful runs now and into the future.
What role does fixturing play in whether I can perform done-in-one machining?
Fixturing is a big factor in whether or not you can machine the part in one go. If you don’t have the capability to re-orient the part and you have a complex part that needs re-orienting for various processes, your machine may not be able to accomplish done-in-one machining. However, it’s uncommon for our team to come across a situation where our CNC deburring tools can’t be integrated to automate deburring and finishing. And getting the right fixturing isn’t typically difficult.
So, what is the right fixturing capability for done-in-one machining? It depends on how you’re machining the part. Often, we see parts that need to be machined on all sides. The operator might have two or three different phases to work the piece through, whether it’s on one machine or on a different machine. They’ll run it in one direction, stop, take the part and flip it over or put it in a new set of vices or work-holding fixture, then run it and do all the operations on that side, then flip it. For us, it’s simply about figuring out what’s happening in those stages so we can determine the best placement for our deburring and finishing products, then optimize the workflow.
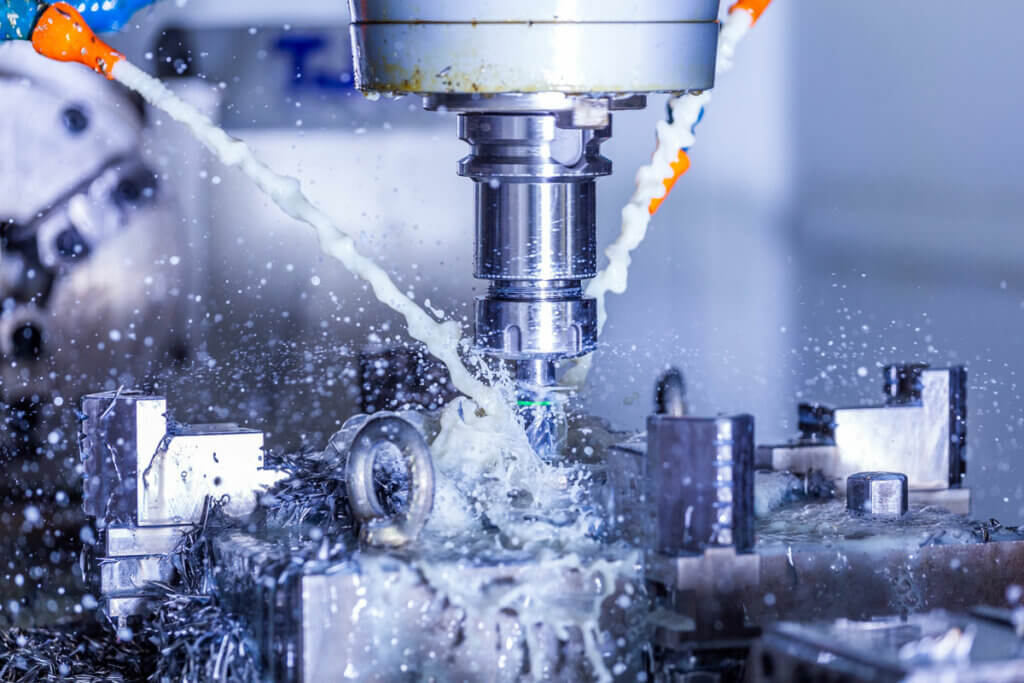
What role do part and process complexity play in done-in-one machining?
For the more complex, higher-end type of products, the milling process can involve several CNC machines. You might mill two sides in one machine, then it goes to another machine and gets flipped to a different face. It’s not unheard of for an operation to involve six to eight machines, with operators moving pieces from one machine to another. This introduces risks of damage. For instance, scratches may result from handling by the time a piece reaches the end of the line. If you have the capability to reduce those touches, it’s best to do so. However, some parts are too complex for done-in-one machining.
If I can’t do done-in-one machining for a part, what are my options for saving time and cost?
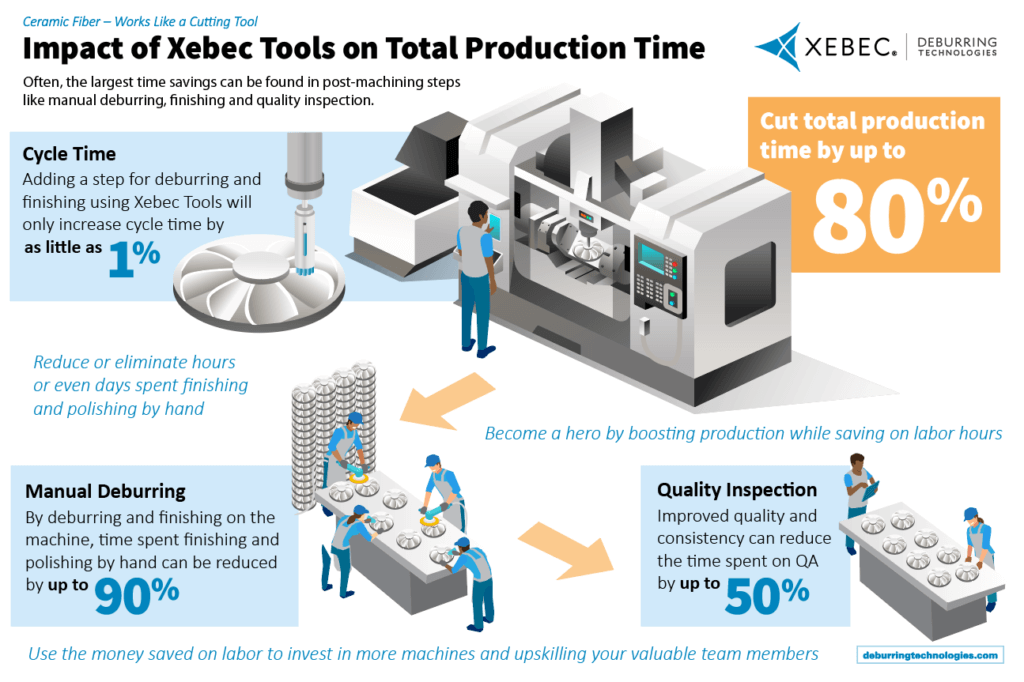
Even in a multiple-machine process, including Xebec deburring tools saves time and cost and reduces the chance of damage from handling. Adding a small amount of time on the machine with our tools drastically reduces net production time for a part, as we explore in the infographic below.
Xebec ceramic fiber brushes are more effective than alternative CNC deburring brushes, in part because they work more like cutting tools than brushes. They offer more consistent quality performance, as they won’t deform over time, and they have a longer tool life. They also work faster than the alternatives.
And automated deburring and finishing is far and away a faster, more efficient alternative than manual deburring and finishing. On top of potential damage from handling and moving a part, you add the risk of overworking or damaging a part during this manual process.
What about using a robotic process for one-and-done machining?
Using a robotic arm to achieve done-in-one machining can be very effective. A robotic arm can move in many different ways, and it has a lot more degrees of freedom and less opportunity to “crash” into other objects compared to in a CNC machine. A robotic arm can also be used with Xebec deburring tools to automate deburring and finishing. Check out this video of automated burr removal and surface finishing of aluminum alloy air rifle rail part using Yaskawa GP8 industrial robotic arm tooled up with Xebec ceramic fiber brushes.
Do you have additional questions about accomplishing done-in-one machining at your facility? Reach out to one of our experts to have a discussion about your machines and processes. Our team has experience advising on multiple aspects of the production process, from optimizing burr formation before deburring to achieving the ideal finish at the end of the cycle.
Contact us to assist you in designing the best milling process from start to finish.