The medical manufacturing industry is a growing sector. Driven by aging populations, an increase in the prevalence of chronic diseases and improvements in technology, demand is increasing in the following medical device sectors:
- Implants
- Instruments
- Equipment
Along with expectations for high performance, medical facilities require exceptional quality and durability, especially for Class III and Class IV devices which are used to support or sustain human life or those that present a potentially high risk for a patient. These devices are regulated more stringently than Class I or II products and require additional levels of approval. Implants such as artificial bones, heart valves, hip joint replacements, stent-grafts and pacemakers are examples of Class III and IV specially controlled medical devices.
More research and development is being done around materials for use in the medical industry, part and device design, and more. Innovations are regularly introduced, making today’s devices and implants higher quality with longer lives.
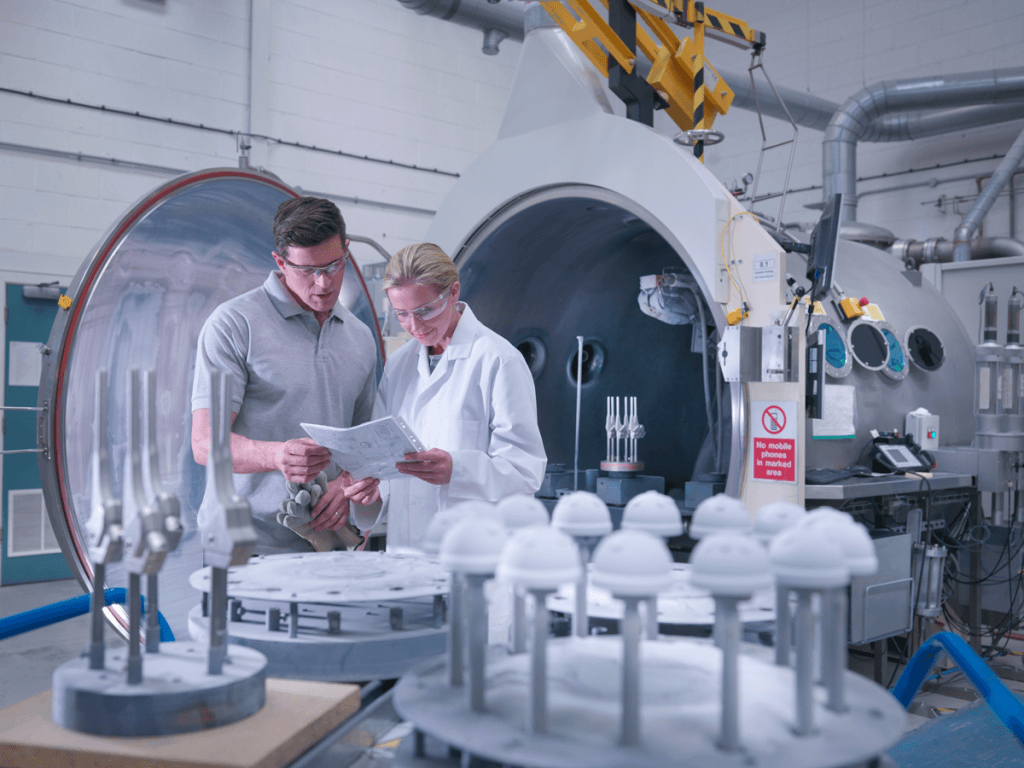
Medical Manufacturing Industry
This overall industry growth is projected to continue, and even steadily increase. By 2032, the value of the global medical device market is expected to reach around $996.9 billion. Medical industry manufacturers with efficient and advanced production capabilities can readily gain from this growth, and others stand to benefit greatly from making the necessary improvements to capture manufacturing opportunities in the industry.
This level of growth calls for manufacturers to explore more sustainable manufacturing practices, not only for the environmental benefits but also for the business benefits:
- Optimize energy usage
- Use fewer tools per job
- Reduce part waste and rework
- Reduce superfluous packaging
- Optimize inventory space
- Reduce tool waste
- Reduce waste from post-machining
- Keep non-biodegradables out of landfills
- Reduce air quality concerns
When evaluating your sustainability goals, don’t overlook your CNC operations. Do a side-by-side comparison of your resource consumption and waste output versus what you could achieve using an automated process using Xebec deburring tools.
>> How Xebec Helps Medical Manufacturers Innovate with the Industry
Deburring and finishing are key processes in medical manufacturing. They help finalize a part for its ultimate use, ensuring performance and reducing the chance of issues downstream. With manual processes or inefficient brushes automated in your CNC machine, it’s hard to consistently meet strict requirements for quality and appearance. Having advanced, automated processes that produce consistent quality results will help you prove out your reputation, reduce cycle time and improve production.
Xebec ceramic fiber tools perform like cutting tools, deburr and finish at once, and produce high quality results manufacturers can rely on. They help manufacturers overcome challenges, capture opportunities, increase throughput and enhance their reputations.
Our customers have spoken. We’ve listened. To help our customers who need to deburr round parts and channeled diameters or deburr deeper bores or recessed surfaces, we added another tool to our arsenal.
The Xebec Stone Flexible Shaft Disc Type can deburr and polish inner diameters of high-precision parts. Its sophisticated design helps our customers reach new dimensions, experienced longer tool life, achieve soft, steady contact, and see greater consistency over time while reducing overall production time.
Challenges in Medical Device Industry
The medical device manufacturing industry faces several challenges today:
Meeting increasing demand: Having capacity to meet demand as it increases is difficult, especially amid labor shortages and other production headaches. It’s particularly challenging when producing just-in-time (JIT) components for medical device implants.
Producing consistent quality parts: Reliable consistency is desirable for medical industry manufacturers because they can be more certain parts will pass inspection, meet requirements and satisfy customers. Consistency reduces costs and helps manufacturers increase productivity.
Meeting tight dimensional tolerances: Parts and devices for the medical industry often demand tight dimensional tolerances having to do with angle, roundness, diameter, contact ratio and more. Achieving this with manual deburring and finishing or with low-quality automated tools is often either impossible or impossibly inefficient.
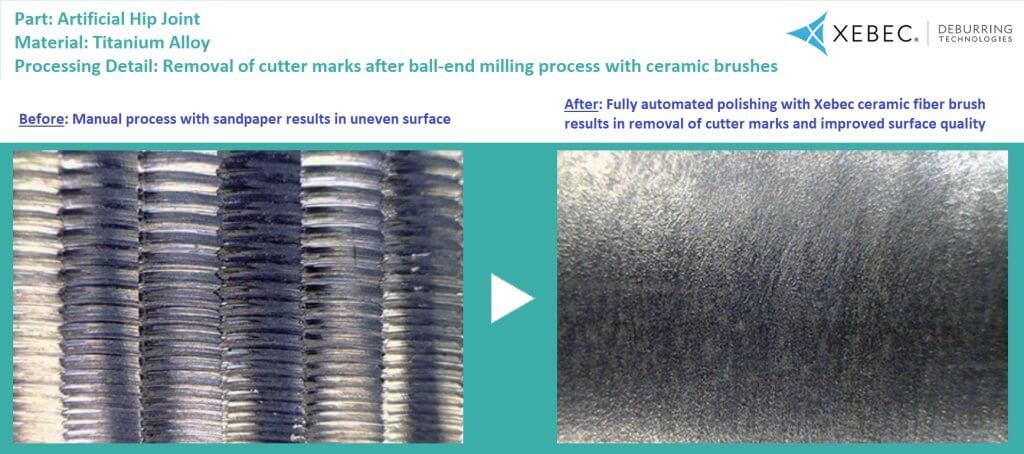
Achieving smooth finishes: Finish is incredibly important in the medical industry. Smooth finishes are necessary to prevent irritation, infection, wear and more. And parts often require additional polishing after the finishing process. Improving your finishing process with quality automated tools can mean better results on the first run and less polishing time when required.
Preventing downstream catastrophes or product failures: Removing burrs and achieving the necessary finish on a medical part or device are critical to preventing issues with parts and products down the line. For instance, the correct finish on a knee replacement ensures it performs as needed and lasts for its expected life.
Achieving desired appearance: Appearance is scrutinized more than ever in the medical industry, even if a part or device is placed where it will never be seen. Visual inspections can send parts back through the line or into the trash. Automating deburring and finishing with Xebec ceramic fiber brushes helps manufacturers achieve excellent finishes, and it can reduce polishing time when additional, fine polishing is needed.
Example: Artificial Hip Joint Manufacturing
Manufacturing artificial hip joints provides a great example of the strict requirements for parts in the medical industry. The surfaces of the hip socket and the hip stem with ball joint must be finished to very precise tolerances to fit correctly and allow smooth performance for the recipient. Both must meet specific angle, straightness, roundness and diameter tolerances and have a specified contact ratio, and each has its own specifications for surface finish.
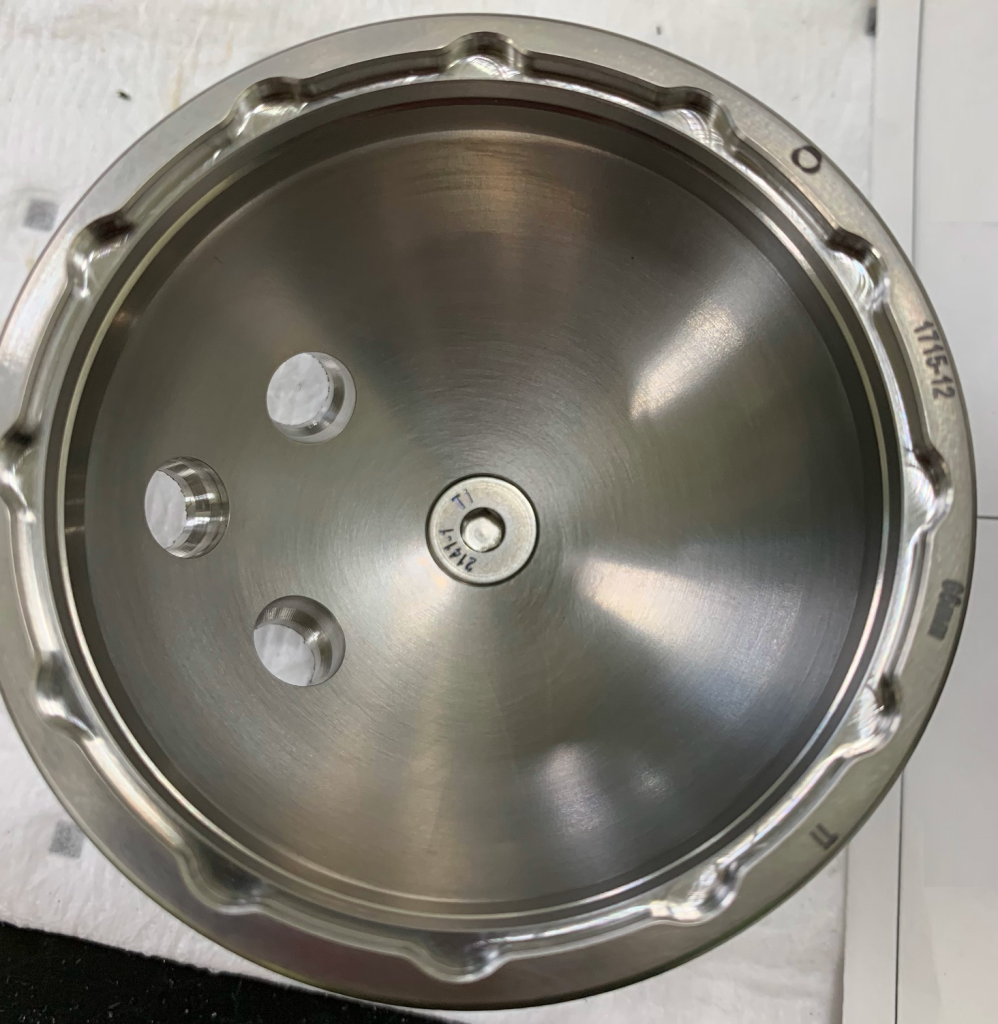
Materials Used in Medical Devices
Materials used in Class III and higher medical devices, such as implants, face intense scrutiny to ensure they meet the requirements of the application they’re intended for. They’re evaluated based on a variety of characteristics, including density, thermal conductivity, melting point and specific heat. For instance, implants must meet strict biocompatibility requirements and be able to resist specific stresses and corrosion.
Common materials used in the medical device manufacturing industry include:
- Cobalt chromium alloys, such as cobalt chromium-molybdenum
- Stainless steel
- Titanium and titanium alloys
- Zirconium
- PEEK plastic
- Thermoplastics and other medical-grade polymers
Different materials will behave differently in manufacturing, so it helps to understand what to expect from a material before you work with it.
Optimizing Medical Device Manufacturing with Effective Deburring and Finishing Applications
Medical device manufacturers can use Xebec deburring tools for a variety of applications, including bone screws, artificial bones, hip replacements and knee replacements (convex surface and medical cup). Here are a few examples of successful applications.
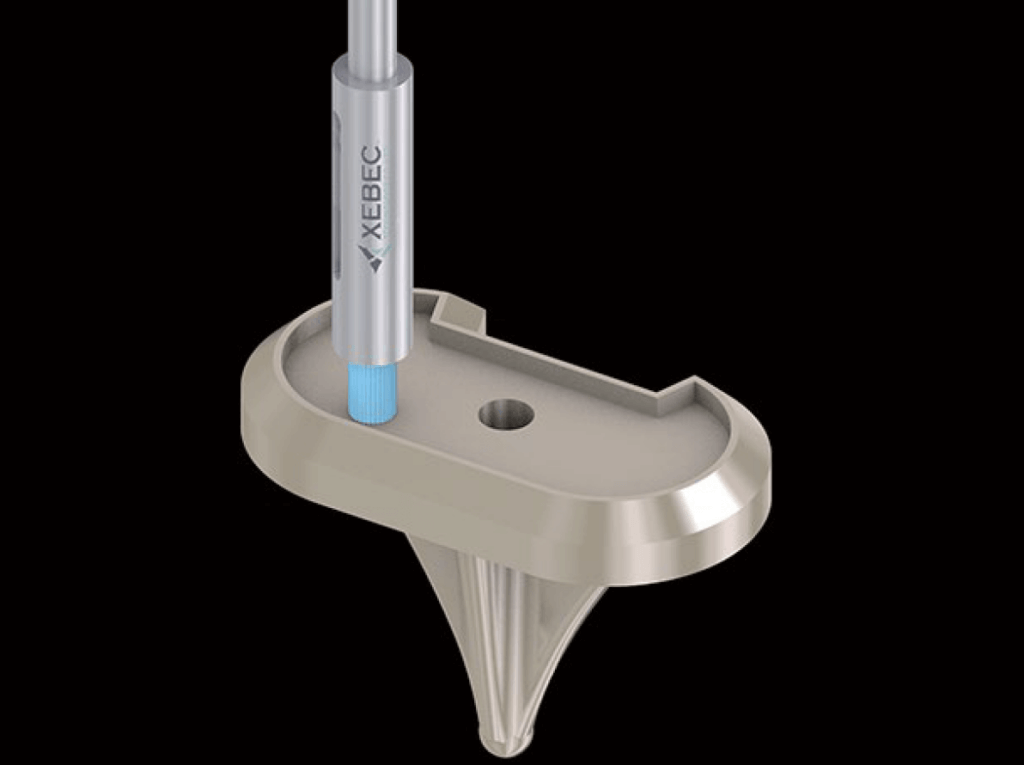
Artificial Bone: A manufacturer used a grindstone and sandpaper to remove cutter marks from and polish stainless steel artificial bone after end mill processing. Manually deburring the part took a lot of time and labor and resulted in unstable quality. The manufacturer replaced this process with automated deburring and finishing using the Xebec Surface Brush and achieved more stable and consistent quality in a shorter cycle time.

Artificial Hip Joint: In one application, a manufacturer removed cutter marks on a titanium alloy hip joint manually using sandpaper. This led to an uneven surface finish and quality. With a Xebec Surface Brush, the manufacturer was able to fully automate polishing and enable complete removal of cutter marks and improvement of surface quality.

Convex Surface: One manufacturer deburred, removed cutter marks, and polished a cobalt chromium-alloy convex surface manually with grindstones and sandpaper, which made it difficult to control dimensional integrity and surface quality. With a Xebec Surface Brush, the manufacturer automated polishing and achieved stable and consistent quality in a shorter cycle time.
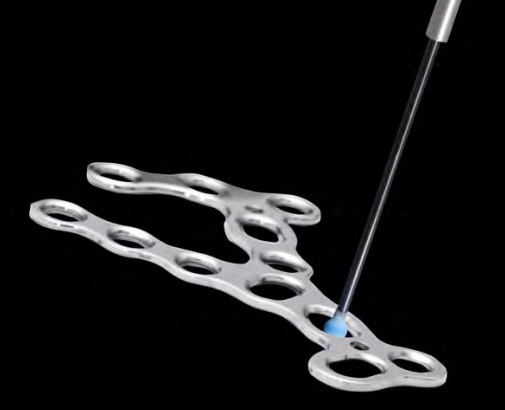
Coronoid Plate: In one application, a manufacturer previously deburred the inner and outer edges of elliptical holes with a rotary bar and rotating tool, damaging edge shape and generating the secondary burr. With a Xebec Stone Flexible Shaft tool, the manufacturer was able to realize a stable edge without generating the secondary burr. The flexible shaft also allowed for soft contact and suppression of subtle vibrations.
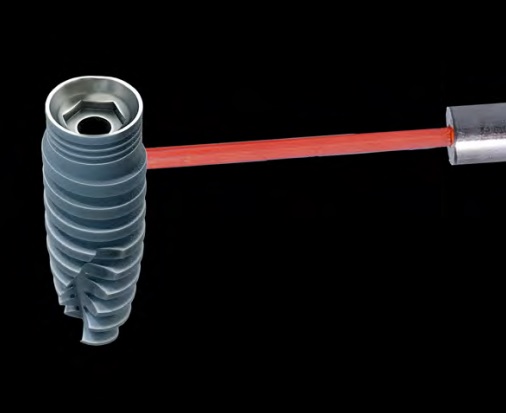
Dental Screw: One manufacturer swapped their manual deburring and polishing process with the Xebec Brush End Type for cutter marker removal, polishing and finishing of parts with narrow features. The result was a more reliable surface quality that could be obtained from CNC machines, robotics or handheld devices.
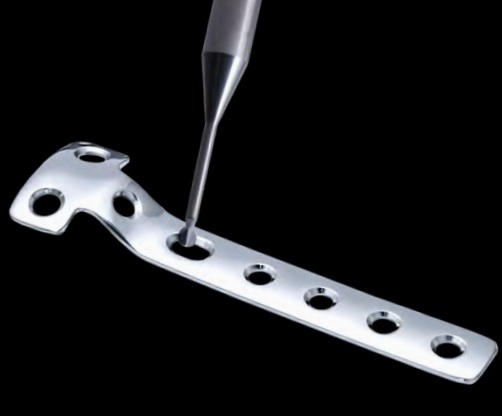
T-Buttress Plates: A manufacturer had been using back deburring tools resulting in poor deburring performance with burrs remaining, secondary burrs and uneven edges. With the Xebec Back Burr Cutter and Path, they experienced uniform CNC deburring without secondary burrs, even in elliptical or off-center holes.
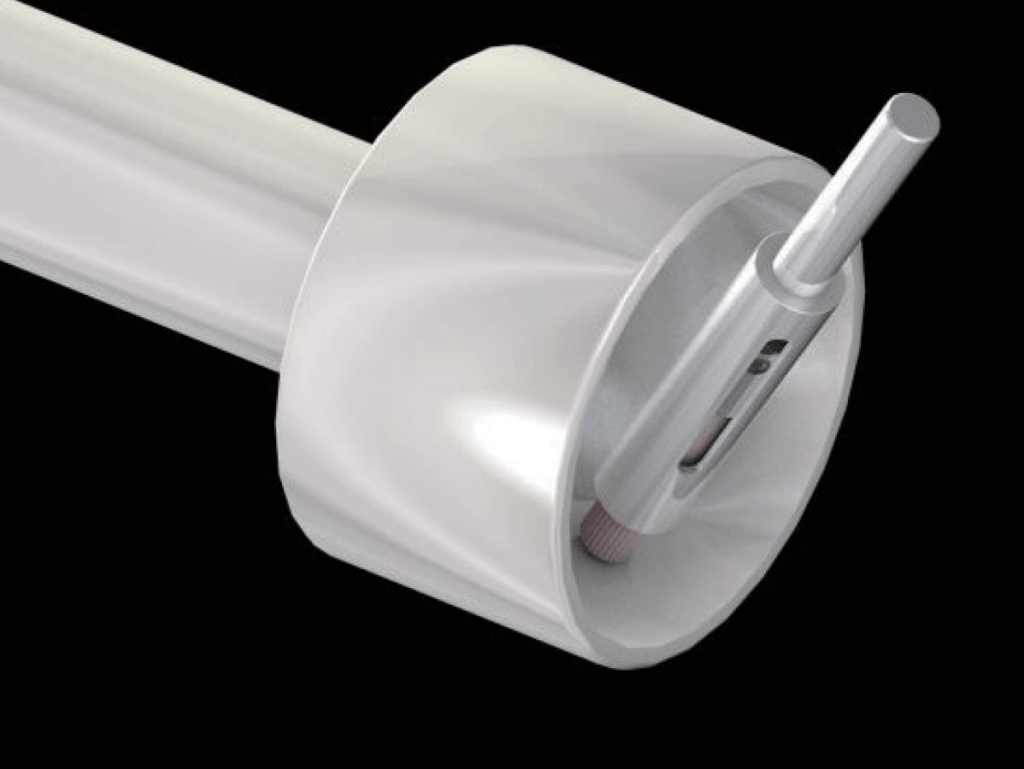
Medical Cup: A manufacturer used manual processes with grindstones and sandpaper to deburr, remove cutter marks from and polish a cobalt-chromium alloy medical cup. This finish quality was unreliable and it was challenging to maintain shape. When they introduced the Xebec Surface Brush in their CNC machining process for polishing, they realized stable quality in a shorter cycle time.
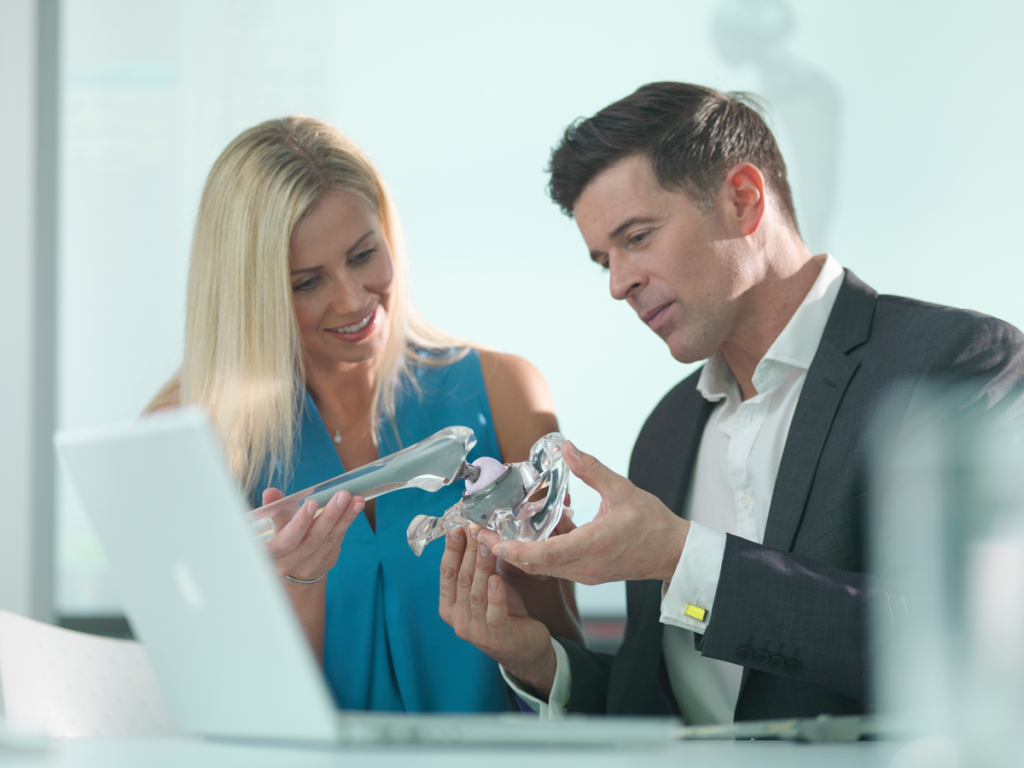
Importance of Medical Device Finishing
Surface finishing and polishing are consequential in the medical manufacturing industry. Devices such as implants must often perform in dynamic ways, such as rolling and sliding. And many perform these actions in a load-bearing application. Abrasiveness on the surface could greatly hinder performance and longevity. It also affects the end user’s experience and health, and surface quality issues could lead to revision or replacement surgery.
The appropriate finish ensures:
- Biocompatibility: Parts must have quality finishes to reduce the risk of contamination and allow for longevity amid chemical stresses and physical pressure. For many parts, a mirror finish is necessary considering its use and critical nature in the body.
- Resistance to Elements and Corrosion: Fine finishes ensure parts don’t have scratches and vulnerable spots through which chemicals and other stressors could penetrate and cause corrosion and wear.
- Performance and Expected Life of Part: When the finish meets the requirement, the part is more likely to perform smoothly and last for its expected life. If the finish is not accurate, friction may reduce performance quality and wear on the part.
Many parts require fine, manual polishing with diamond paste or another abrasive after finishing to ensure biocompatibility and performance. These parts are polished to a mirror finish, which is typically considered 1-12 Ra microinches (µin).
Xebec ceramic fiber brushes can typically achieve 4-40 Ra microinches depending on the material and the number of passes, so you can produce impressive surface finishes in less time than manual finishing or automated finishing with other brush types. And if a manufacturer needs further polishing after finishing, Xebec brushes will save significant time in the finishing process and require far less time to polish considering the surface quality that ceramic fiber brushes can produce.
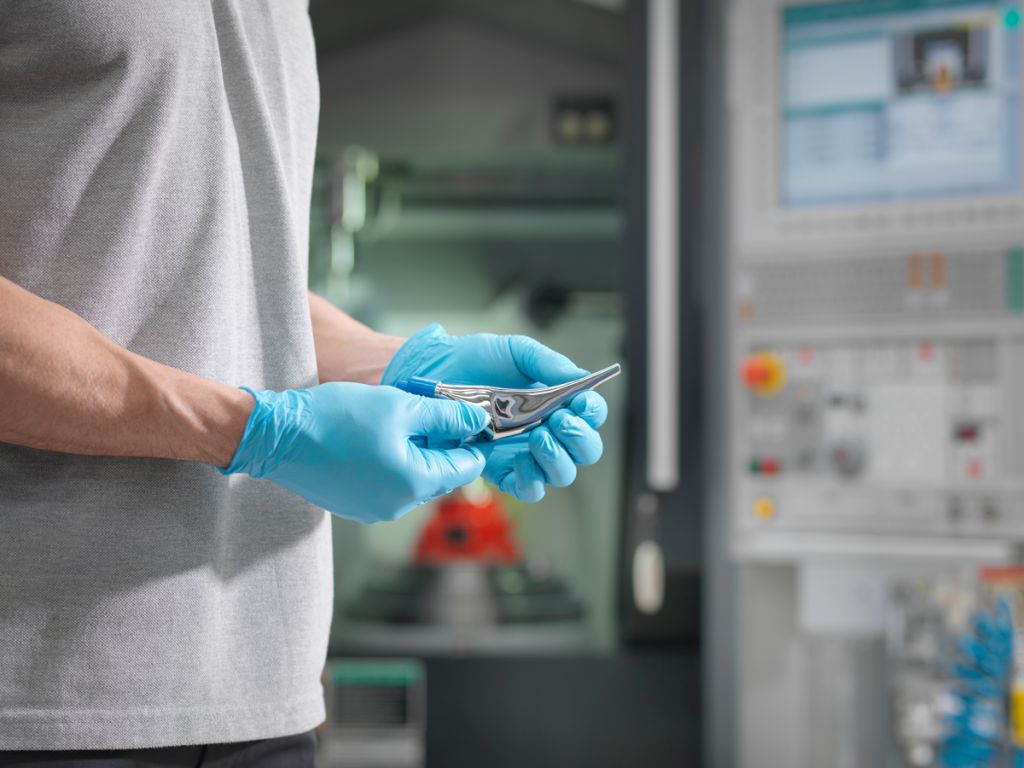
Innovation In Medical Device Industry: Automated Deburring and Finishing
The tight requirements and critical nature of parts for the medical industry present challenges to any manufacturer with manual deburring and finishing processes. Individuals’ capabilities and performance vary throughout the day, week and month. And these parts demand such attention to detail that working them manually takes hours, often with intense visual focus and uncomfortable positioning. One slip of the hand could mean the part is scrapped.
When machine shops and manufacturers eliminate manual deburring and significantly reduce the time for finishing, they experience improvements in production and across their operations, including improved consistency and quality to ensure parts meet tight tolerances and have smooth finishes. This reduces costs and helps you increase productivity, as well as prevent product failure or downstream issues with a part.
Automated deburring and finishing also helps you increase capacity due to lower cycle time achieved and better allocation of labor, allowing you to take on more jobs and increase profits.
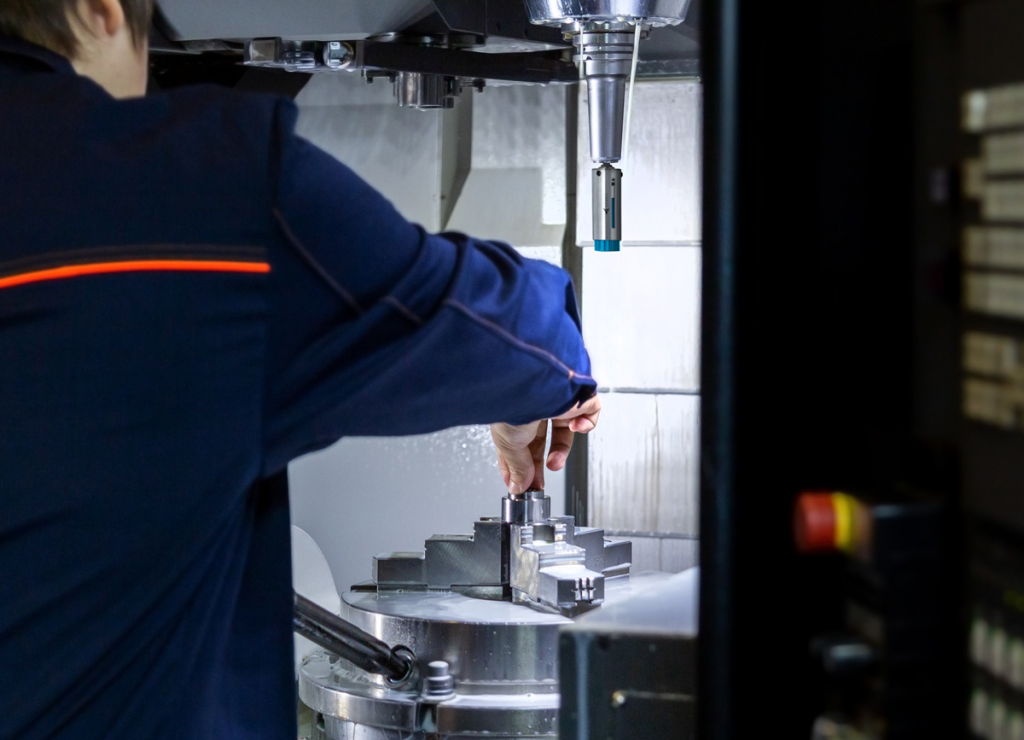
How Xebec Deburring Solutions Help Manufacturers Exceed Expectations
Medical industry manufacturers realize many benefits from switching to automated deburring and finishing with Xebec ceramic fiber products. Xebec ceramic fiber brushes perform like cutting tools and produce the consistent, high-quality outcomes manufacturers need to meet strict requirements in the industry. They help manufacturers:
- Shorten cycle time
- Better allocate labor
- Achieve consistency in quality
- Reduce costs associated with scrap, rework and manual labor
- Capture new opportunities in their field
- Increase throughput
Xebec representatives have experience working with manufacturers in the medical device industry. We understand how to help you make the most of an automated process, from tool selection to job costing and improving cycle times and productivity. Learn the secrets of deburring and finishing success by working with our team.
Contact us online or by calling us at our Ohio operations center at (800) 306-5901 to see how we can help you meet customer expectations for the highest quality medical devices.